Oil and gas solutions company Flogistix has been leveraging an Internet of Things (IoT)-based solution for approximately five years that provides the firm with a view into the conditions of each of its vapor-recovery units (VRUs) and compressors wherever they may be deployed. The cloud-based system enables Flogistix and its maintenance personnel to view each asset’s conditions based on sensor data provided in a digital twin. The sensor data includes the temperature, speed and pressure of oil or gas flow through each compressor. That information is captured via a Verizon Wireless cellular connection.
Recently, the Oklahoma City-based company has expanded this system by using a 3D solution from UrsaLeo, an enterprise software firm that provides oil and gas customers with visualization tools and related products for facility operators. With the solution, which Flogistix began deploying about four months ago, the company can create and interact with three-dimensional digital twins for each compressor, which provide greater visual access to the conditions in and around each asset. The system enables Flogistix to identify and prevent problems before they can occur, says Jerred Wilson, the company’s chief technology officer.
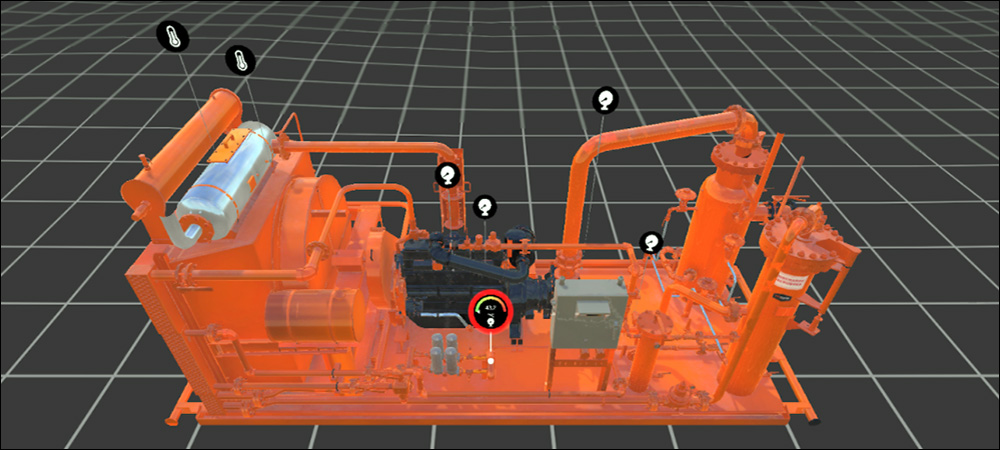
The solution enables Flogistix and its maintenance personnel to view each asset’s conditions based on sensor data provided in a digital twin.
With the UrsaLeo technology, Flogistix can now view a greater amount of sensor information, including the direction of flow through each compressor. The company serves the oil and gas industry with products intended to optimize operations at wellheads. Its atmospheric solutions include VRUs that collect vapor from gas production and eliminate the need for venting and flaring. It also offers a methane or gas leak-detection service with handheld optical gas-imaging cameras and drone-based cameras. The drones can use sniffers and lasers to identify a leak and forward that data via a cellular connection.
Going forward, the company plans to offer a digital line of business products leveraging the virtual flowmeter, with the data the company then provides to its customers for a fee, so that they will be able to view the flow of gas and optimize accordingly. That service, Wilson reports, can include an alert that will be triggered any time sensor readings fall above or below a specified threshold.
For companies that have equipment installed at remote locations, but which lack access to wireless sensors and a digital twin, manual efforts are the only way to ensure the health and productivity of the equipment. In such a scenario, Wilson says, “You’re depending on a mechanic making the rounds, or a notification” from those onsite that there may be a problem—which is reactive rather than proactive. At Flogistix, he says, every compressor or VRU is assigned to a particular mechanic, and the wireless sensor data being retrieved is viewed by that individual remotely. Workers can set up alerts to ensure they receive a notice as soon as a potential problem has been detected.
The company has been growing in recent years. While the pandemic and oil prices impacted the need to manufacture new units, the demand for product and services has been rising more recently. “We are trending up again on unit leases and purchases,” Wilson reports. “We now have almost 2,000 units, leased and customer-owned, being actively managed” in its Flux product line. Flogistix offers a 98 percent run-time aimed at preventing unnecessary trips to worksites, while increasing effectiveness. Maintaining those compressors and other items can be expensive and time-consuming, he notes. In fact, it costs hundreds of dollars simply to send a mechanic to a site.
Traditionally, with its sensors wired to a programmable logic controller (PLC) and a cellular-based connection to that PLC, mechanics could look at individual data points and, in some cases, conduct triage remotely using Flogistix’s existing IoT platform. However, Wilson says, the firm sought greater visibility and functionality. Viewing a unit holistically and visually, he explains, can enable diagnosis often without workers being onsite. “Seeing fluid flow and simultaneous alerting on data thresholds,” he states (such as temperature and speed), “allows a mechanic to determine if a trip is really necessary.”
With the 3D digital-twin technology, data can be visualized with greater detail and with more information via an iOS mobile app, according to John Burton, UrsaLeo’s CEO. The solution leverages the Unity gaming-development software suite to create virtual assets of each piece of equipment in a digital twin that UrsaLeo describes as “photorealistic.” The virtual assets are then paired with supervisory control and data acquisition (SCADA) and machine-learning data. In this way, maintenance personnel and other users can predict equipment or part failures and, in some scenarios, perform remote repairs.
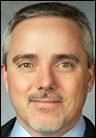
Jerred Wilson
In the future, Flogistix plans to use the 3D digital-twin solution when testing new technologies and training fuel technicians and mechanics. One key feature will be the ability to view the direction of fluids, which can help in training new mechanics unfamiliar with the compressors. The technology will be available for use on mobile iOS devices, thereby allowing greater transparency and collaboration between Flogistix and its customers. The firm expects to have 3D digital-twin ability for all of its Flux units in 2021, Wilson says. To date, UrsaLeo’s solution has been used with two of the company’s half-dozen unique products.
With the new mobile application, Wilson reports, the system will make it possible for mechanics to view data on their mobile phones, wherever they may be located. “We also expect to improve training by using 3D digital twins to further familiarize our mechanics with tedious items, such as PLC wiring,” he states. The new digital twin will provide field service data that was not available in the past, Wilson says. UrsaLeo’s solution, he says, is “an interactive model you can zoom in and out of, replay history, and watch things progress to show where there may be an issue.” He adds, “We’re still playing around with features like the fluid flow.”
UrsaLeo was launched when the oil and gas industry was beginning to capture data from oilfield sites so that it could be managed virtually. Burton, along with cofounder Angie Sticher (now the company’s COO and CPO), got together in 2017 to launch the company in San Francisco, in order to provide a better way for businesses to access that data. UrsaLeo began talking to Flogistix about the solution in February of this year.
The deployment currently enables users to capture and view analysis based on approximately 50 data points measured at each specific compressor. According to Wilson, the benefits will result from a reduced need to visit compressors and VRUs, which can typically cost up to $400 apiece for employees simply to arrive onsite. Additionally, it offers a safety function by reducing the need for mechanics to visit sites more often than necessary. In the long term, Wilson predicts, “We expect to have 3D digital twins at every site for all of our units.”
Flogistix could offer the data as a service to its customers so that they would have a real-time view into the health of their production equipment onsite. Wilson anticipates customers “wanting to model other non-Flogistix equipment that could further help them analyze the effectiveness of their entire site.” He states, “We expect to have this fully rolled out to all units in Q2 2021.”