Christmas is a busy time for a lot of companies. For Grupo Disber, the season is especially demanding. In Spain, the (cesta de navidad) Christmas basket, filled with various foods and alcoholic beverages, is the most popular holiday gift, the company reports. Over the course of a few months, Grupo Disber sells 1.5 million of the baskets to consumers and businesses, making it the nation’s leading provider of such items.
To keep a better eye on the Christmas baskets as they are packed onto pallets and shipped—in order to both reduce labor and increase accuracy—the company has installed an RFID system that tracks the baskets as they travel through the firm’s 75,000-square-meter (807,000-square-foot) complex of warehouses, located in Valencia. The technology, the company reports, has reduced its staffing costs by 10 percent, as well as eliminated 90 percent of shipping mistakes and resulting customer returns. The system was provided by Tag Ingenieros Consultores (Tag Consulting Engineers), an RFID solutions provider also based in Valencia. “They wanted to increase their company productivity, reduce errors and have a total tracking system,” says Javier Muñoz Giner, Tag Ingenieros Consultores’ CEO.
The baskets—which are actually cardboard boxes typically measuring approximately 1.3 feet by 3 feet by six inches (though some boxes are twice that size)—can include cognac, brandy, champagne, sausages, chocolates, nuts, cheese and drinking glasses. In anticipation of the Christmas rush, the company employs between 400 and 500 workers for four months, to pack, store and ship the boxes. Grupo Disber assembles and ships up to 1,000 pallets per day, with an average of 50 boxes per pallet, all loaded onto 20 to 25 trucks. Before the RFID solution was deployed, each order’s accuracy was manually confirmed by employees, to ensure that no gift basket containing the wrong products was shipped out. Employees simply compared each box visually against the paper order. The sheer volume of boxes being shipped led to errors, however, which could include misplacing goods within the warehouse. What’s more, there was no tracking system in place to make sure that each box had been sent to the right customer at the proper time.
After deciding to try an RFID solution, Grupo Disber carried out a test of the system from June to September 2008, in advance of the Christmas season. Once the company determined that the box tags were being accurately read, it installed RFID readers and software from Intermec for the 2008 season. The firm is now in its third season of full-scale deployment. The system includes EPC Gen 2 ultrahigh-frequency (UHF) tags featuring Thin Propeller antennas and Monza 3 chips from Impinj. After a box is packed and closed, Grupo Disber’s staff members attach a pre-encoded adhesive RFID tag over the lid to ensure the box is sealed. If anyone had opened the box, its tag would be torn and become inoperable, thereby serving as an alert that its contents would need to verified. In some cases, the company prints and encodes its own tags using one of the four printers utilized for non-standard or custom products.
Upon receiving an order, Grupo Disber forwards it to the warehouse, where a worker then prints the necessary RFID tags to attach to each gift box in that particular order. When the boxes have been retrieved from warehouse shelves, a tag is applied to each box, and workers read the tags using an Intermec IP30 handheld interrogator, in order to link them with the products being loaded onto a pallet. The unique ID number of each item linked to the order number in the back-end system is sent via a Wi-Fi connection to Tag Ingenieros Consultores’ software, residing on Grupo Disber’s back-end system, and designed to share data with the company’s management system.
The loaded pallet is then stretch-wrapped on one of three stretch-wrapping machines, which rotates the pallet, enabling an Intermec IF61 reader connected to two Intermec IA39B antennas to capture each tag’s unique ID. The tag IDs are transmitted back to the Tag Ingenieros Consultores software via a cabled connection, and the software confirms that the boxes match the order. The order’s status is then changed to indicate the pallets are loaded and stretch-wrapped.
If the shipment contains an error, such as the wrong box being packed on the pallet, the software displays an alert to a screen mounted by the stretch-wrap machine. If the pallet is correctly loaded, that correct status is likewise displayed on the screen.
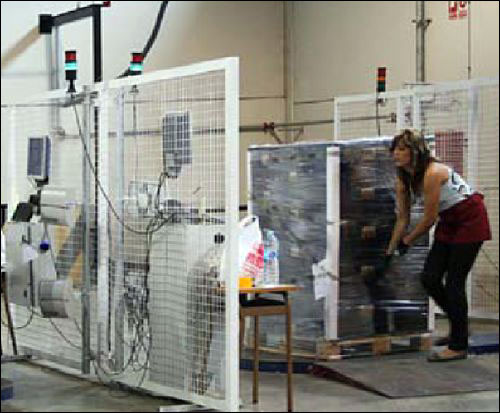
Once the pallet has been stretch-wrapped and the software has validated that orders are complete, the workers transport the pallets to one of the complex’s five warehouses, passing them through automated pallet-transport tunnels (a total of four tunnels extending to the five warehouses) via conveyer belts. Each tunnel, built by Tag Ingenieros Consultores, is equipped with one IF61 reader and four IA39C antennas mounted around the belt, to capture the tags from four different angles.
After the pallet has passed through the RFID-scanning tunnel, the software updates the order status to warehouse storage, indicating in which warehouse the pallet is located, based on the tunnel reader’s identity. The dispatch staff then receives an update indicating the pallet has entered storage, and trucks are dispatched to pick up the orders based on the number of pallets and orders that passed through the tunnels.
When the time comes to ship the pallets, they are then placed in loading areas within those warehouses. Due to the large number of pallets waiting in a large space near the loading docks, the staff at that site use mobile RFID readers. Tag Ingenieros Consultores designed and provided 12 mobile RFID reader stations on wheels, each of which includes an IF61 reader and four IA39B circularly polarized antennas. When a truck is about to be loaded, a mobile interrogator is rolled to the loading area, and each pallet is pushed through the mobile reader station as it is loaded onto the truck. At that point, the information is again forwarded to the back-end system via a cabled connection between the mobile reader and a personal computer installed at the station.
In the event that the boxes are returned from a customer, they again pass through one of the mobile RFID reader portals, identifying which boxes have been returned, while the software updates that data to alert management.
One of the greatest challenges during this installation, Muñoz says, involved providing an RFID tag that could be attached and read from a variety of form factors, since the size and shape of the boxes vary. Ultimately, the group concluded that an inlay consisting of Impinj’s Thin Propeller antenna and Monza 3 chip met the necessary requirements. The extremely fast pace of pallets moving between the warehouse and the loading docks, he notes, created another challenge for devising an infrastructure that would be easy to use and not impair staff movement.
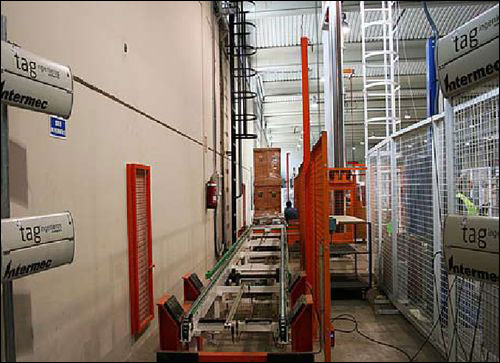
“Many trials were performed during the pilot with different kinds of tags, speed, etc.” Muñoz states.
Currently, the software developed by TAG Ingenieros Consultores shares data with the company’s business-management software through a file-exchange system. In the future, Muñoz says, the firm intends to change its business-management software so that it can receive the RFID reader data directly.