Ed. Note: A version of this article originally appeared at IoP Journal.
In recent years, there have been numerous radio frequency identification advances in Brazil’s cotton sector. Last month, an historic achievement reached the country’s entire agribusiness segment, when ID-Cotton‘s technology was used to ship what the firm calls the world’s first 100 percent traceable cotton cargo. The operation was based at the Port of Santos and was bound for Vietnam, where a spinning mill will now have complete data regarding the raw materials’ origin and history.
“Today, we are certain that we have contributed to a real milestone in the history of Brazilian cotton,” says Flávio Tarasoff, ID-Cotton’s CEO, “shipping the first 100 percent tracked cargo of cotton lint in the world, using ID-Cotton’s RFID technology. There were many challenges and, of course, we have the support of many people, companies and entities that are part of this chain. The cargo will go to Vietnam and will be tracked to the spinning mill, which will carry out processing, taking into account its origin and history from field to port of destination.”
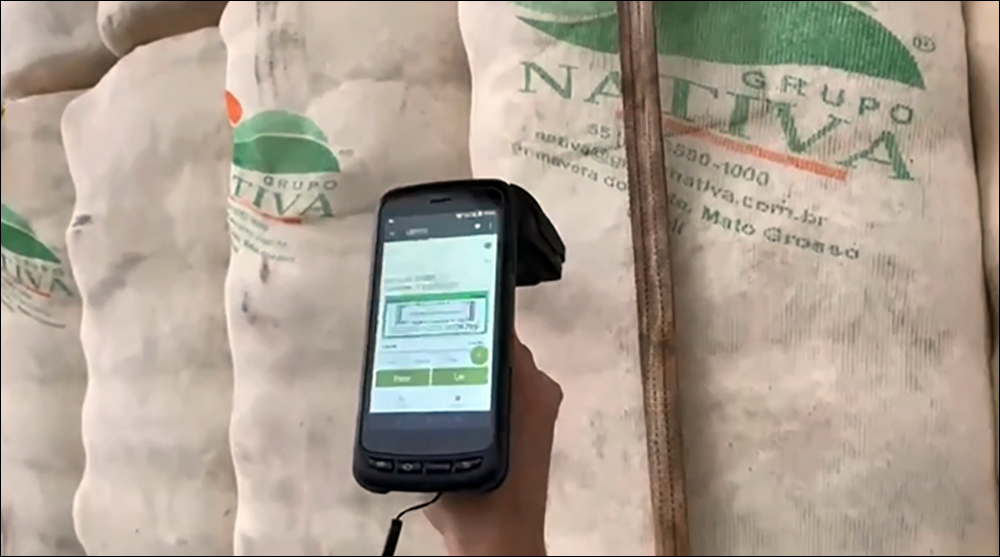
ID-Cotton’s traceability solution is designed to combat flaws in processes for marking and identifying harvested bales.
For the past four years, ID-Cotton has been developing RFID solutions to enable cotton to be traced from harvesting through to processing. Tarasoff says the system is aimed at annual harvests. “We started with a production unit,” he states, “and today we have more than 45 using the solutions.” Bom Futuro Agro Group, Brazil’s largest cotton producer, was a pioneer in the use of ID-Cotton. Then followed Scheffer, Amaggi, Locks and Cortezia Agro Groups, all from Mato Grosso, which together represent more than 20 percent of the country’s lint production.
Before ID-Cotton’s RFID solution was implemented, Tarasoff says, all management in the Brazilian cotton sector was carried out via labels and manual processes, such as barcodes. The deployment follows GS1‘s passive EPC UHF standard, he says, adding, “The main benefit is the traceability of production, operational management, storage and increased gain in the classification of lint when using ID-Cotton’s tools.”
Located in Cuiabá, ID-Cotton centralizes the system’s production, operation, support and sales at its headquarters. “This year,” Tarasoff says, “we formed ID-Cotton Agribusiness LLC in the city of Doral, Fla. The location is strategic, as it is close to the local port and airport, and it will concentrate the manufacture of equipment to be distributed in the international market, with the kits already ready. The proximity to Texas is also a facilitator, as that is the largest cotton-planting area in the United States.”
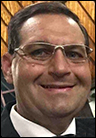
Flávio Tarasoff
ID-Cotton’s traceability solution is designed to combat flaws in processes for marking and identifying harvested bales. The system is intended to eliminate the need for manual labels and handwritten spreadsheets, Tarasoff says, as well as spray-painting on canvas and other old methods of identifying producers, farms, varieties, fields, borders and contaminants. The ID-Cotton system, he adds, is intended to facilitate yard management and processing, prevent the contamination of cotton varieties, ensure product quality and keep cotton lint prices low.
In practice, once cotton is harvested, RFID tags inserted in cotton rolls are read and recognized by means of a tablet and ID-Cotton’s system. This information is synchronized with the company’s enterprise resource planning (ERP) software, which automatically reads the loads of these rolls via an RFID portal. The system collects cotton crop movements as products are transferred to the firm’s processing unit.
“One of the most important factors was the technological change,” Tarasoff says. “Before cotton harvest and transport, barcode labels were used, which had several flaws, ranging from a lack of reading to registration errors, since the process was performed manually.” The solution developed by ID-Cotton offers integration with ERP data, he adds. “By facilitating the marking and identification of bales in the field, the ID-Cotton system increases productivity and reduces staff in the field.”
With bales each receiving a unique identifier, transport management becomes more agile, Tarasoff says, as does the real-time location of each package. “Our technology reduces time in the yard and the use of the scale,” he states. “Finally, the system saves on personnel, labels and manual processes, guaranteeing real gains in the final value of the cotton.” Since it is modular, he notes, the system serves the major players in agribusiness and can be used by farmers, cotton units and cooperatives as well, among others.
“This year, we are importing the data that we recorded on the canvas tags for the new RFID tags,” Tarasoff says. “This will be added to the cotton lint, which can be used for blockage management, laboratory analysis tracking, cargo management, loading and unloading, and classification of the lint at the next step in the production chain—the spinning mills.”
The RFID readings were related to mass and density, the structure of the vehicles that handle cargo, weather conditions (rain, calm and humidity), the bales’ positions on trailers, the variety of trailers used, the angles of the scales during weighing, and failures in manufacturers’ processes. “Since it is a completely new technology,” Tarasoff explains, “there were many challenges, most of which were focused on transport.”
The differences in tare (the weight of a truck without a load) and the structure of the vehicles, as well as the variety of trailers used, each with different heights and volumes, and the positions of the cotton bales, were all analyzed to carry out readings without failures. “Weather conditions, such as rain, sun and relative humidity, also have influence,” Tarasoff says, “and the system had to take these variations into account.” A demonstration recorded by ID-Cotton and narrated by Tarasoff can be viewed here in Portuguese.