- Deploying the System in Less than a Minute
- Low Power and Bidirectional Transmission
- Analyzing Sounds in a Noisy Environment
An international team of tech companies has developed an Internet of Things (IoT)-based acoustic sensor solution that measures the sound from wind turbine blades in order to identify or predict potential damage or the need for maintenance. South African IoT solutions company Lattech Systems is working with acoustics sensor provider Ping and IoT connectivity company u-blox. The solution is designed to reduce the cost of turbine blade repair or replacement, by identifying problems automatically before they can become critical or disrupt power generation. The partners estimate that the system, consisting of two sensors and IoT connectivity, can reduce a wind farm’s costs by 25 percent for blade repairs and 30 percent for replacement.
Lattech Systems designs and manufacturers telemetry solutions to connect companies’ equipment with their monitoring or managing infrastructure. The latest challenge the firm is addressing involves managing some of the most remote, yet critical equipment—namely, turbines at wind farms around the world. Turbine blades are subject to strain and potential damage, according to Truhann van der Poel, Lattech’s founder. Parts can loosen, corrode or be otherwise damaged by weather, he says, adding, “All sorts of things can happen which affect the efficiency of the wind turbine.”
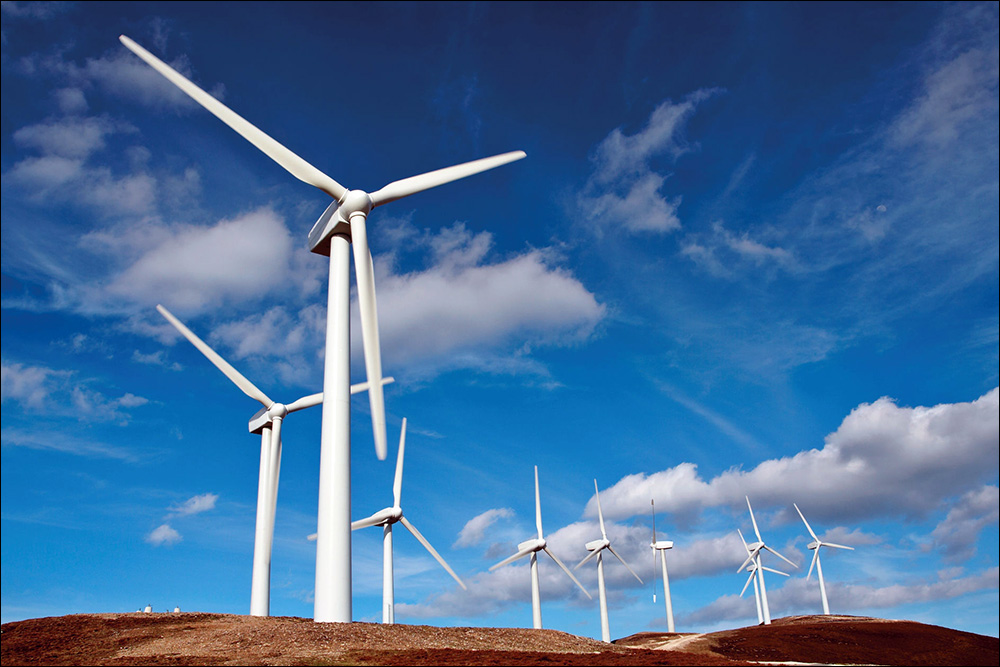
The solution reduces the cost of turbine blade repair or replacement by identifying problems automatically before they can become critical.
For this reason, businesses send inspectors or maintenance personnel onsite to wind farms, typically once or twice a year, to inspect the blades and ensure they are operating properly. Sometimes, drones can accomplish this task as well. When engineers arrive onsite for inspections, they often climb the turbines, a process that carries safety risks. When they complete their report and leave the site, it may be months before they return. If damage occurs in the interim, there is no one there to diagnose it.
Thus, the first alert a wind farm might receive would be a disruption in turbine service. By that time, van der Poel says, the repair could be quite costly. Blade replacement could cost between $200,000 and $1.5 million, whereas damage repairs, depending on the severity, could cost $4,000 to $50,000. One way in which potential problems can be identified is via sound, he adds, since malfunctioning blades can be audible. Therefore, Ping and Lattech Systems developed a predictive-maintenance solution that uses sound to identify changes in operation.
Ping specializes in the manipulation and classification of sound. For this solution, the company leveraged a microphone and developed algorithms built into a sensor device with that mic, to characterize the sounds that the blade makes as it rotates. To transmit data wirelessly from remote sites, Lattech Systems works with u-blox, which provides IoT connectivity via a component built into Lattech’s LS091 power and communication module (PCM) in a weatherproof encasing. U-blox’s SARA-R412M module, built into the device, can transmit via LTE-M, NB-IoT or 2G.
Deploying the System in Less than a Minute
The box is made of ruggedized polycarbonate material, and a customized solar panel harvests solar energy. It comes with a small internal battery and can harvest enough energy to power both the sensor and the telecommunication process 24 hours a day, seven days a week. This means the system does not require an external power source, which is an important point, according to the companies, for while the turbine is a power generator, its power is not accessible to sensors.
To deploy the system, workers at a wind site would simply attach two pieces (cabled together) to the turbine’s base. Both pieces come with a magnet to make application simple. Employees can mount the device on each turbine in less than a minute, the companies report. “This as an easy install,” van der Poel says, and is low in risk. “You don’t need specialized tools. You just put it on there and leave it.”
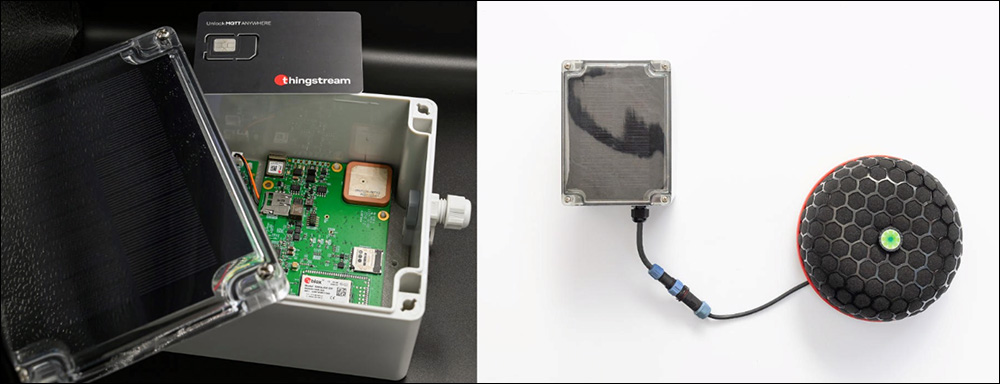
The company leveraged a microphone and developed algorithms built into a sensor device with that mic, to characterize the sounds that the blade makes as it rotates.
Once the system is installed, it begins to transmit directly to the software. The mics can then capture sounds and transmit analytics based on those sounds to the Lattech device, which forwards the collected data via an IoT network. The information is forwarded via technology from Thingstream (a u-blox company) to Thingstream’s IoT cloud platform over an available public cellular network.
Each time the blade passes the Ping sensor, the sensor records the data and uses artificial intelligence to characterize the sound and establish the device’s maintenance status, such as operating normally or potentially requiring attention. Analysis of the sound can be especially challenging, the companies note, due to the variables created by different types of blades, different environments and the height of the blades. As data builds up, it creates a maintenance value that the system can identify and download. The solution then forwards the downloaded parameters back to the Lattech device.
“So what our job is,” van der Poel explains, “is to read these maintenance values on a continuous basis and report that over the cloud.” The Thingstream global SIM in the Lattech device can also transmit via LoRaWAN to a local gateway, or via a cellular network, such as LTE-M, NB-IoT or 2G. The technology is currently being tested at wind farms in Australia, as well as at an offshore wind turbine site in the North Sea, near the United Kingdom.
Low Power and Bidirectional Transmission
Ping had previously built such a solution with another telemetry company, but the device had been unable to achieve enough power to operate fully in areas where the Sun might be obscured for days. Lattech Systems opted for a more efficient communication service, says Neil Hamilton, u-blox’s global head of service sales, while providing bidirectional functionality via the u-blox unit. In other words, the wind farm can send data to the device as well as receive data from it, including new firmware or instructions to transmit. “We use Thingstream for bidirectional transmission,” van der Poel states.
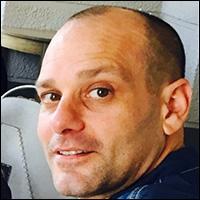
Truhann van der Poel
A future generation of the product is expected to feature all the electronics, including a microphone and an acoustic sensor, as well as power and IoT transmission, in a single device that can be mounted on turbines. “That will make them even easier to install and more cost-effective,” van der Poel says, “because there’s less cables.” He expects that generation to be available later this year. The company can manufacture the devices via 3D printing, making it easier to create custom devices for companies. The future device will also accommodate more sensors so that the system will be able to detect other conditions, such as subsurface moisture and temperature levels, via probes.
For the current wind turbine solution, the system can monitor battery voltage and the device’s temperature, as well as acoustics. The data can also provide analytics, such as identifying when blade health may be slowly eroding, then sharing human-readable information on dashboards to indicate that a problem exists, along with whether or not it requires an immediate response. The collected data can then be used to provide maintenance schedules, urgent repairs or other services.
According to van der Poel, the IoT network can send relatively small packets of data at a distance with low power consumption. The u-blox system operates in most countries, he says, making it relatively inexpensive for use at most sites. To save energy, the solution typically turns the audio sensor on every few hours and analyzes results, and it transmits those results periodically, providing multiple sets of data daily. A catastrophic change in a blade’s acoustics would prompt an alert in real time. The device comes with an accelerometer so Lattech can detect if it falls off or is at risk of falling due to a tilt.
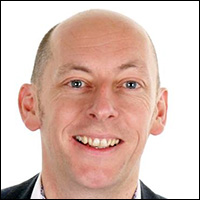
Neil Hamilton
Analyzing Sounds in a Noisy Environment
The technology is the result of considerable innovation on the part of Ping’s engineers, van der Poel reports. One of the biggest challenges was to develop an enclosure that could ensure the mics and the algorithm would not detect or misidentify other sounds, such as wind. The round shape helps to shield the microphones from the audio noise generated by nature. The other challenge involved the data analysis required to detect the normal sounds expected from all kinds of blades, and to identify when a new blade has been installed.
The IoT system’s ability to operate with most cellular networks available globally is relatively unique, Hamilton says. Thingstream can take the data and send it efficiently at a fixed cost, allowing predictability from a cost perspective, as well as the ability to transmit in two directions. The Thingstream data is fully encrypted, he adds, providing a level of security as it transmits over public cell operator networks. “That is absolutely unique at the moment,” Hamilton states.
Key Takeaways:
- IoT technology is capturing and transmitting analytics about wind turbine health with sound sensors and low-power transmissions.
- A wind company in Australia is deploying the system to ensure real-time alerts and analytics regarding the health of its turbines installed around the country.