RFID technology has reduced inventory-management labor time at Italian fine jewelry retailer Matranga by 96 percent, at the company’s stores in Palermo and Trapani, Sicily, as well as in its vault—a secured warehouse in Palermo used to store additional inventory. The system tracks every tagged item at Matranga’s stores and in the vault, not only making the inventory-checking process faster and improving inventory-count accuracy, but also automating the process of creating bridal registries and then managing them as purchases are made.
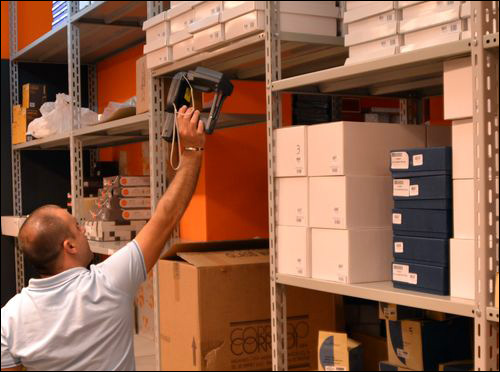
Matranga sells high-value watches and jewelry, as well as silver and china. Its customers include the well-to-do, such as members of royal families throughout Europe. Altogether, its two stores carry an average inventory of 5,000 Rolex watches and 3,000 rings, necklaces, bracelets and other pieces of jewelry. The stores also sell fine silver, cutlery and china, and have approximately 4,000 items on hand at any given time across both locations. The two shops rack up a combined €5 million ($6.8 million) in annual sales, and since each item is of such high value, accumulating excess inventory is out of the question.
In order to ensure that no items are missing, and that no products become out of stock, store employees have conducted quarterly inventory checks throughout the display cabinets and within the vault—a task that typically required 24 man-hours to complete. These inventory checks not only were time-consuming, but also had the potential for errors if workers missed any items. What’s more, the manual inventory auditing process left Matranga vulnerable to security risks, since an employee spent considerable time in the vault area and could remove items without authorization.
To better track the locations of the 12,000 items it normally carries in stock, and to prevent out-of-stocks, the company has now applied an RFID label to each item. The solution, designed and installed by Dynamic ID in July 2011, also helps the stores ensure that all products are available without having to maintain excess stock. The hardware was supplied and configured by RFID Global by Softwork, formerly known simply as Softwork.
The solution employs Dynamic ID’s Jewel-ID software. According to Paola Visentin, RFID Global by Softwork’s marketing and global communication manager, Jewel-ID records the inventory data, links that information to each RFID label’s ID number and manages all read events, updating the status of products accordingly.
At each store, Dynamic ID installed a fixed Feig Electronic MRU200 RFID reader in a storefront countertop, and also supplied Nordic ID Merlin mobile computers. RFID Global by Softwork’s customized passive EPC ultrahigh-frequency (UHF) RFID labels, made with Alien Technology Higgs-3 chips, are attached to each item.
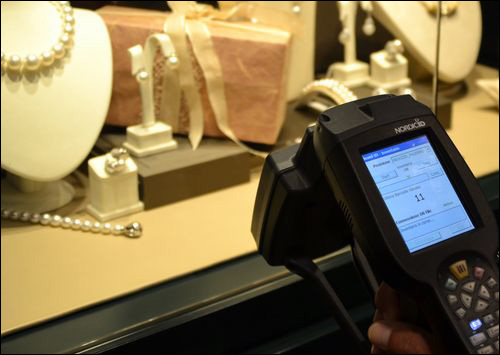
For each new item arriving at either store, Matranga’s staff use a Toshiba Tec B-SX4T printer with a Feig MU02 UHF reader module (integrated by RFID Global by Softwork) to print and encode a label, and then attach it to the item. The staff members then input the item’s lot number and description, and link that data to the label’s RFID number in the Jewel-ID software, residing on Matranga’s server.
When the retailer wishes to conduct inventory checks, that task can be accomplished in two ways. For tracking items in trays stored within display cabinets, a tray (typically containing 30 tagged items) is placed on the counter with the built-in Feig reader. That reader captures the unique ID encoded on each tag, and forwards the collected information to the Jewel-ID software. A handheld reader is used to interrogate the RFID labels of items stored within the vault or in the cabinets, by passing the device near those items.
When an item is sold, a salesperson removes its RFID label and reads it using the fixed built-in counter reader. This deletes that item from the list of available inventory in the Jewel-ID software.
The technology is also used for gift registries. For example, when a bridal couple visits the store to set up a registry, their names and other information are input to create a record in the Jewel-ID software. They then select specific items they would like to receive, which workers place on the counter, above the built-in fixed reader, so that each item’s unique ID is captured and stored in that couple’s registry. If a wedding guest buys an item from that registry, its RFID label is interrogated and the software updates the registry status to indicate that the item has been purchased, thereby ensuring that no one tries to purchase the same gift. At the same time, the software updates the inventory data to indicate that an item has been sold and must be replaced.
Since the system’s installation, Giuseppe Serafini, Matranga’s CEO, says his company has recouped its investment in the RFID system within less than one year, based on reduced labor costs and the assurance that no out-of-stocks occur at either store.
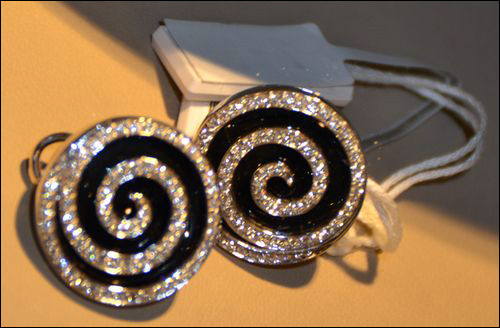
The amount of time dedicated to performing inventory checks at both stores and within the vault has been reduced from 24 hours (involving three workers for an entire eight-hour day) to one hour for a single employee. This also means personnel spend less time in the vault with the jewelry, thereby improving security as well. The firm now completes an inventory check of all items every week, instead of once every three months.
The tagging of jewelry presented a challenge, since ferrous cutlery and silver interfere with UHF RFID transmission performance. Therefore, RFID Global by Softwork opted to apply labels with a decorative string that further separates the tag from a metal object. In the case of cutlery, the label is placed in the box rather than on a piece of cutlery itself.