Grupo Vidrala, a Spanish glass container manufacturer, is employing an RFID system—with EPC Gen 2 readers installed on forklifts, and tags affixed to loaded pallets—at three of its factories, in order to improve efficiency by tracking product from the point of production to when the goods are loaded onto trucks destined for customers. The company plans to expand the system to all 13 of its production centers across Europe by the end of 2012. The solution was provided by JSV Informatica y Comunicaciones, with Intermec hardware. By using RFID, Vidrala’s management has been able to reduce the amount of time required for moving product, and to receive alerts in the event that errors occur.
Grupo Vidrala has manufactured glass containers used by the food and agriculture industries for 45 years. The company has been expanding its operations during the past decade, with the addition of three Spanish production centers, as well as a plant in Italy, in Portugal and in Belgium. Vidrala’s 13 glass-melting furnaces have the combined capacity to produce more than 3.5 billion containers. After introducing a SAP software system into all of its facilities, the firm began seeking other technology solutions that could tie into that warehouse-management system (WMS), in order to improve efficiency and be able to track every pallet.
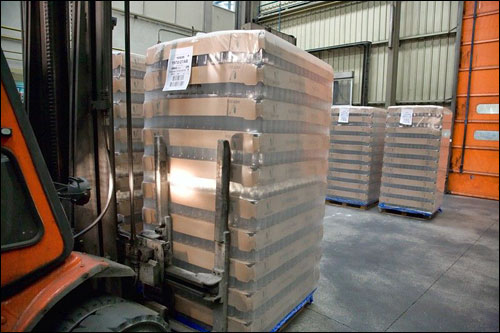
“Our goal is to improve control of pallets, to obtain unitary traceability and to feed our warehouse management system with accurate information,” says José Manuel Delicado, the chief of maintenance and research and development at Vidrala’s factory in Crisnova, Spain. After putting Delicado in charge of the SAP system deployment, the company determined that his Crisnova location would be the best place to start.
The Crisnova facility moves approximately 1,100 pallets daily, with about 300 movements taking place internally (for example, from the production area to storage). Before the RFID system was installed, the warehouse staff had to manually track every pallet’s location and identification on paper. If a pallet needed to be moved, for instance, an employee would retrieve paperwork from the office listing the location at which that pallet was expected to be. This information was based on details previously handwritten by workers as the pallet was being placed at that location, and was then input into the computer by the office staff. According to the company, this tended to be a slow process with a potential for errors.
With the new system, Vidrala loads a pallet, then attaches a UPM RFID ShortDipole RFID label made with NXP Semiconductors‘ G2XM chip to each pallet prior to stretch-wrapping it. As the label is printed, says José Carlos Herrero, Intermec’s chief technical officer, the unique ID number encoded to its tag is linked to data regarding the product being loaded onto it, using an Intermec IF30 fixed reader cabled to the RFID label printer, as well as robots that apply the label and stretch-wrap.
Each forklift is equipped with an Intermec IV7 RFID reader and two reader antennnas that capture the ID number of the RFID label attached to the pallet the vehicle is carrying. The interrogator then forwards the collected IDs to Vidrala’s back-end software, via a Wi-Fi connection. If such a connection is not possible at that time, the information is stored until a connection is detected. The JSV software (which interprets data from each RFID tag read) is integrated with the company’s warehouse-management system. The software sends data to the forklift’s vehicle-mounted Intermec CV30 computer terminal, which displays instructions indicating where the pallet should be placed. If the driver determines that the pallet needs to be moved to a different spot, he or she can input that information via the CV30’s keypad. The new location is transmitted to JSV software, and then to the WMS.
Upon receiving an order for glassware stored on a particular pallet, the office staff can instruct a forklift driver to retrieve that pallet, by sending the instructions and the pallet’s location to the CV30 computer onboard that individual’s vehicle.
The warehouse staff uses an Intermec CN3 handheld computer with an IP30 reader to read the bar codes on the RFID labels in the event that a new label needs to be attached to a pallet. The handheld’s RFID interrogator is also utilized if a problem is found on a pallet. If, for example, a particular bottle is determined to have a flaw, the entire pallet is removed from the warehouse or production area, and is relocated to an area at which any flawed items can be replaced, after which a new label is attached to the pallet and the handheld is used to enter that new tag into the system.
After completing installation at the Crisnova plant, as well as a plant in Aiala, Spain, and one in Gallo, Portugal, Vidrala plans to install the RFID technology in Barcelona by the end of this year, followed by the Belgian and Italian factories in 2012.
“We have seen improvement in many areas,” Delicado states, “but the most important are traceability of every pallet, and no errors in movements and shipping.” The company can more quickly respond to a customer’s order, he adds, by directing the pickup of pallets with the RFID system.