A 1998 RFID application that tracks industrial-sized mixing bowls as they move around the factory floor continues to run smoothly, helping Lebkuchen Schmidt delight sweets lovers with a large palette of baked goods. Based in Nuremburg, Germany, the company turns out gingerbread of all sorts, in addition to almond cookies and stolen (dry German cakes sprinkled with powdered sugar).
Rainer Schmucker, an engineer specializing in food production, led the implementation project nearly eight years ago. He has continued his work as the manager responsible for the company’s entire production process—from the mixing of various doughs and baking of breads, to the cooling and packaging of these goods. At present, RFID is used only in the mixing process—not for tracking racks of cooled goods or finished goods—though the company has considered expanding the system.
At the time of implementation, Lebkuchen Schmidt occasionally faced bad batches of sweets after a worker forgot to add an ingredient, or filled too much or too little of other ingredients, into the 3-foot-high kettles. Schmucker will not say what the error rate was, but indicates the problem was frequent enough for Lebkuchen Schmidt to seek a solution. The company first considered bar-code labels, but rejected the idea because dust from flour and other ingredients could easily cover a label and prevent a bar code reader from scanning it. “RFID was the logical solution, with its contactless data transfer,” Schmucker says.
With the help of systems integrator Hermos Informatik, Lebkuchen Schmidt attached 15 transponders to the sides of stainless-steel mixing kettles, though a total of 20 transponders were ultimately used. Workers then pushed kettles on wheels from mixing station to mixing station.
Glass-covered cylindrical 134.2 kHz transponders, 3.85 millimeters wide and 32 millimeters long and made by Texas Instruments, are sealed inside round, white plastic casings 10 centimeters in diameter. The casings keep out dust and grit from the factory line, while keeping transponders dry when kettles are put through their daily high-pressure washing.
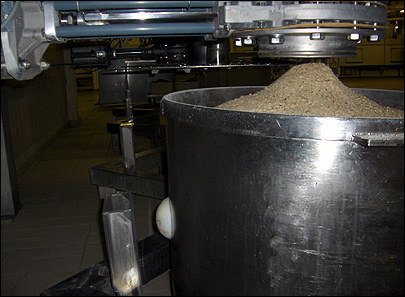
At the start of the production cycle, each transponder’s unique identification code is matched in the system with the batch’s recipe. One worker accompanies each batch from beginning to end, visiting up to eight stations (equipped with a total of eight readers). At each stop, a mounted RFID interrogator (reader) reads the transponder automatically, within a range of 20 to 30 centimeters. The readers, specially designed by Hermos for the application, are waterproof in accordance with standards set by the Verein Deutscher Ingenieure (VDI), the Association of German Engineers.
Data is processed in the system, which uses Proline software developed by Hermos. Employees receive instructions on a Siemens-made screen about how much of each ingredient to add and which mixing station to visit next. At some stations, ingredients are added by hand; at others, pre-measured ingredients are put in the mix automatically.
The data transfer from the reader into the software system is made via a “profi bus,” or a data hub that directs information via cable to the system’s programmable logic controller (PLC). Today, most such data transfers happen over wireless LAN.
Data is fed into Hermos’ Proline software, which has been updated to run on Windows XP and was customized to work together with Lebkuchen Schmidt’s enterprise resource planning (ERP) system.
Workers continue around the factory floor to all stations needed for each recipe until each kettle of dough is complete. Workers don’t necessarily go from Station 1 to Station 8; the first reading of the transponder usually takes place at the flour or sugar station, though from a technical point of view, a baker could start at any point on the factory floor. The order of mixing varies with each recipe, with up to nine different recipes being produced at one time. If a kettle misses a mixing station, the system will notify the worker, who can then wheel it to the appropriate location. At the end of the mixing process, workers receive a notice that a batch is done.
Separately, Lebkuchen Schmidt has three “hand transponders,” encased in the same white plastic but not mounted to a particular mixing bowl. When a small order needs to be filled or a small batch needs to be made, a worker carries a hand transponder and a smaller mixing bowl, moving from one mixing station to the next, as guided by the screens. This system allows personnel to work on small, separate orders without interrupting the flow of mass production.
When the system was implemented, Lebkuchen Schmidt faced no problems with the technology but did have to invest time to retrain workers on the new process, Schmucker says. Now, everything reportedly runs smoothly.
Via RFID, Lebkuchen Schmidt benefits from a more precise mixing process but has also collected valuable information about its overall production cycle. The system can generate reports that show how much of each ingredient was used for which recipes and when. This data can be used to produce a report on the origins of each batch in case Lebkuchen Schmidt is ever investigated under a European law requiring food producers to be able to trace all products.
Schmucker says it isn’t able to quantify the exact return on Lebkuchen Schmidt’s RFID investment because the company calculates the benefits qualitatively—i.e., improvement in the quality of finished products—rather than monetarily. Still, he does say it has incurred fewer expenses linked to batches gone wrong. As an early RFID pioneer, the company says its implementation has cost it about 400,000 German marks, or 204,500 euros ($262,000). Each year, the company invests about 5,000 to 6,000 euros ($6,400 to $7,700) to maintain the system, with assistance from Brooks Automation’s RFID division. Some 19 of the original 20 transponders are still in use.
Despite its long-standing positive experience with RFID, the company has no immediate plans to expand its RFID system. It has considered using RFID to track raw materials when they are delivered to the factory, or to trace the movement of pallets around the factory floor, but it has not yet acted on those plans.