Hay farmers and distributors throughout North America, Europe and Australia are currently using or testing an RFID-based solution for tracking hay bales. The system allows the companies to store and access data regarding a single bale of hay, including its point of origin, date and time of harvest, moisture content, and exact location within a field, as well as any fertilizers used on it.
Harvest Tec, a 30-year-old provider of equipment and products for hay producers, is marketing the solution, which features an RFID tagger that encodes a passive ultrahigh-frequency (UHF) RFID tag and attaches it to hay during the baling process. The solution also includes fixed, vehicle-mounted and handheld RFID readers for use by distributors, and, in some cases, software to manage the collected read data.
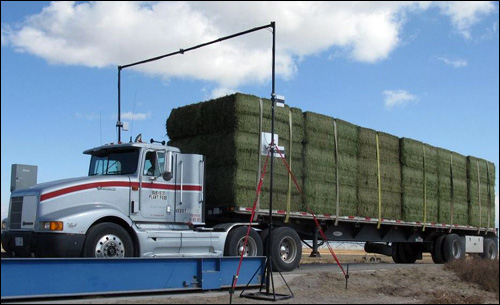
Harvest Tec began developing the system more than three years ago, says Jeff Roberts, the company’s president. The solution, which operates with a variety of hay-baling systems provided by New Holland, AGCO and Case IH, is aimed at hay producers, distributors and buyers—all of whom, Roberts says, would benefit from having accessible data about each individual bale of hay, in order to ensure that all hay delivered is of the type and quality that the buyer or seller believes it to be.
Without such technology, hay buyers or sellers can have little control over the quality and conditions of their bales. The bales tend to look alike, Roberts says, but they are not all the same. Some come from lower-quality hay, have higher moisture content, or include chemicals that a particular buyer might not want. In addition, many bales simply cannot be seen in a large stack of hay being shipped to or from a distributor, or being received by a customer. Sometimes, if a single bale is found to be bad—for example, if a visual inspection reveals it to be too moist—a customer can reject an entire load of product.
For the seller, ensuring that every bale falls into the category required by a buyer—such as a specific age, or exposure to a particular fertilizer—can be equally difficult, as hay bales are delivered to a distributor in truck loads, and are then moved around the facility prior to being sold.
Harvest Tec’s solution is intended to bring visibility into the history of every hay bale, so that those in the supply chain can understand the type of product in front of them.
The technology is used to first identify hay in the field during harvesting. Balers are equipped with an RFID tagger containing a ThingMagic Mercury5Me (M5e) RFID reader. The solution employs an Alien Technology passive EPC Gen 2 UHF ALN-9640 Squiggle inlay, integrated in a sheet of vinyl plastic by WS PackagingGroup. The RFID tagger—which measures 16.5 inches by 16.5 inches by 30 inches, and is mounted atop the bale chamber—holds a roll of 850 adhesive vinyl RFID tags. As the bale passes through the chamber, two arms on the tagger lift the twine and wrap a tag around it, applying one tag per bale. As the bale (typically measuring 2 feet by 4 feet by 2 feet) is pushed out of the chamber, it passes under an RFID reader antenna mounted at the chamber’s rear. The tagger then encodes a variety of data to the tag’s 512-bit user memory, including a bale’s serial number, its average moisture amount (as detected by the baler sensor), and the kinds of preservatives used, as well as the hay’s field name, bale weight (based on the average weight of the three previous bales, assuming the baler is equipped with a scale) and field position, based on GPS data.
That information can then be stored on the baler’s onboard computer, and can later be loaded to software on the user’s database via a USB connection.
When the bale is received at a distributor (sometimes a different company than the producer, or sometimes the same), it can pass through a fixed ThingMagic Mercury6 (M6) RFID reader, providing that distributor with all of the information written to the tag. Hay distributors can also acquire Harvest Tec RFID readers with a built-in ThingMagic Mercury5e (M5e) module, and mount them on forklifts that move bales. In this way, a distributor can learn about all bales it receives, moves or prepares to sell—and have the option of rejecting specific bales at the time of receipt, or to separate those of different qualities. When a truck is being loaded with product to be shipped to a buyer, bales that are wet, for example, can be set aside so that they are not sent to the customer.
This information, Roberts says, guarantees that customers receiving the bales will have a consistent product and thus be less likely to have complaints. The data can also be valuable to customs officials in countries requiring proof of which chemicals may have been used on the hay, he adds.
In addition, producers can collect data about variations from one bale to another in a field (such as different weights). This enables the companies to better manage crops and fertilization accordingly.
The hay farmers and distributors using the technology have declined to comment on the system, indicating that the installation is still too early in the testing phase to determine its immediate success. The challenges related to the solution center around two areas, Roberts says. Having the tag applied consistently on the bale was an early hurdle, he notes, but the technology has since reached a 98 percent rate of application accuracy. The ability to communicate with the tags through hay was the other problem, Roberts reports. “We’re reading tags at an acceptable distance [with] our stationary readers,” he states, by utilizing multiple antennas. Harvest Tec is continuing its effort to increase read range with the handheld reader. At present, the handhelds are reading tags about 5 feet away, while the fixed readers achieve a 20-foot read range and the baler reader has read range of 15 feet.
What’s more, Harvest Tec is currently developing a Wi-Fi version of the solution that would allow handheld or forklift-mounted readers to wirelessly transmit data to a back-end system. According to Roberts, approximately 120 RFID taggers are in use on balers—mostly in the United States—while the company is providing the technology for testing in Australia and Europe.
Although Harvest Tec supplies software that can collect and store data culled from RFID bale tag reads, Roberts says, “most customers have developed their own software.”