Ludwig Pfeiffer, a global structural and civil-engineering firm based in Germany, eliminated the need for its construction foremen to manually track the company’s 6,000 pieces of equipment at dozens of European construction sites, and reduced the amount of time needed for its annual inventory check time by 50 percent, by adopting an RFID-based solution provided by Advanced Panmobil Systems and Reutemann.net. Ludwig Pfeiffer reports that the solution has saved its workers time in tracking equipment, has reduced the incidence of errors related to items’ locations, and is now being used by employees to clock in and out at the job site.
The company, headquartered in the city of Kassel, has approximately 60 active construction sites throughout much of Europe, where its personnel are working at any given time. According to Frank Menzel, Ludwig Pfeiffer’s CEO, the company also provides 6,000 pieces of equipment—including cable drums, excavators and excavator shovels—to those sites, and must monitor when those items are used, inspected, repaired or moved from one location to another, or back to the headquarters.
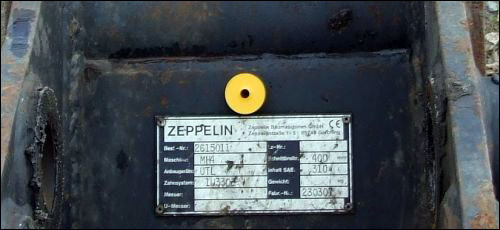
To track all of the collected equipment-based data—both location and maintenance—the company’s staff manually wrote the details on paper and provided that paperwork to the office to be entered into a computer. Each time a piece of equipment was moved, the construction site manager filled out a dispatch note, which was also transmitted to the main office to be transcribed. This process was slow, requiring that employees wait for the paperwork to reach the office so they could input data electronically, and errors were sometimes introduced because digits were transposed or handwriting was illegible.
After reviewing a variety of technology options in fall 2009, Ludwig Pfeiffer selected an RFID-based solution from Reutemann.net and Panmobil. The company attached a passive 13.56 MHz RFID tag, made with NXP Semiconductors‘ Icode chips compliant with the ISO 15693 standard, to each piece of equipment. For most of the equipment, the tags were glued on, but some tags were screwed or riveted on, for items requiring an especially robust attachment. The tags vary in size from 15 millimeters (0.6 inch) in diameter to 30 by 40 millimeters (1.2 to 1.6 inch) in width and length, says Jens Reutemann, the head of sales at Reutemann.net, which provided the tags. The unique ID number encoded to each chip is linked to the equipment’s description, serial number and history in the Reutemann.net software.
Project foremen at each construction site are equipped with Panmobil Scanndy handheld RFID readers that also serve as bar-code scanners. When not being used, the devices are placed in onboard docking cradles installed within work vehicles—typically, the project foremen’s trucks.
When a piece of equipment is being moved or inspected, or if it has a problem that needs to be reported, the foreman first interrogates an RFID tag in his own ID badge, and then reads the ID number on the tool’s tag. Once he returns the handheld to the vehicle’s docking unit, that unit transmits the tag ID numbers, along with its own GPS-based location, to Ludwig Pfeiffer’s server via a GPRS or UMTS connection, says Stefan Leske, Advanced Panmobil Systems’ head of marketing and PR.
The Reutemann.net software, residing on that server, receives those tag IDs, and retrieves that tool’s maintenance and usage history, which appears on Scanndy’s display screen. The foreman can then enter additional information, such as any defects on the equipment, any inspections being conducted and their results, or the equipment’s movement to another site.
If the tool is being issued to a worker for use at that site, or to transport to another location, that individual’s ID badge number is stored along with the location data, creating a record of who is responsible for that piece of equipment until the next time the tag is read. “The user and the site of the equipment is defined by the last scan,” Reutemann says. “The equipment stays in responsibility of the last user, until it is taken over by another one via a scan of the tag.”
If a piece of equipment is leaving the construction site, Reutemann adds, the foreman reads that item’s tag and selects the status “leaving.” At the new site, the foreman in charge then reads the tag and selects “receipt.”
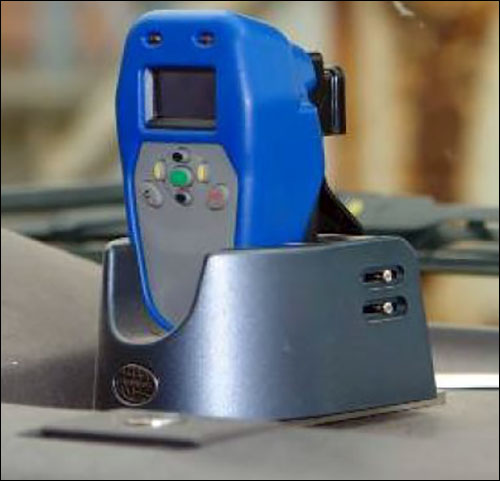
Some pieces of equipment have no suitable space for an RFID tag, and instead are fitted with labels printed with a bar-coded ID number. The bar codes can be scanned using the same Panmobil Scanndy handheld device, Reutemann explains, but when possible, RFID is preferable to bar-code labels. “Civil-engineering equipment has to withstand some rough conditions,” he says, adding that bar codes are not readable if they are covered in mud or if they have some scratches. “RFID tags are much more robust. If you have a clean and dry indoor business, bar codes would work fine, too. But in this solution, bar codes are just a ‘Plan B’ when RFID tags cannot be placed on equipment.”
If an item requires repair, the foreman can send it back to the headquarters, where the repair shop is located. A technician can interrogate the tag and view data on his reader’s screen identifying the problem with the equipment. In turn, once the repair is complete, the technician can input data regarding the work performed to the system using the handheld device, and when it returns to a construction site, the foreman can view details about the repair.
“Most of the staff like the new way, without filling out the transfer forms. It is just quicker and easier,” Menzel states. “And the supervisors can find all equipment they are looking for in seconds.”
The system will also be used for performing annual stock checks, in which personnel conduct a full inventory of all equipment at every site, as well as what is in storage. The process can be time-consuming, but with RFID, the company has been able to cut in half the labor time required for the process.
Although the solution was acquired to track equipment, Menzel says, the firm is now beginning to use it to log workers onto and off the site at the beginning and end of each shift. Like the project foremen, each of Ludwig Pfeiffer’s 200 employees carries an RFID badge on a keychain, with the badge’s unique ID paired to his identity in the software. The foreman reads each tag ID as personnel report to work, and again when they leave, thereby automating the time-stamp process. That data can then be used by the payroll department.