Navistar Defense, which manufactures armored vehicles designed to withstand roadside bombs and other threats, is employing an RFID-enabled real-time location system (RTLS) to help ensure the vehicles are delivered on time to U.S. troops in Afghanistan and Iraq.
WhereNet, a Zebra Technologies company, is providing the RTLS to Navistar Defense, a wholly owned affiliate of Navistar International, a holding company whose subsidiaries produce commercial and military trucks, diesel engines, school and commercial buses, and chassis for motor homes and step vans. The RTLS is being used to help Navistar Defense track, in real time, each MaxxPro MRAP (Mine Resistant Ambush Protected) vehicle as it is assembled, from the time a chassis is delivered to the company’s West Point, Miss., manufacturing facility through the assembly and inspection processes and on to when an MRAP is shipped off to war.
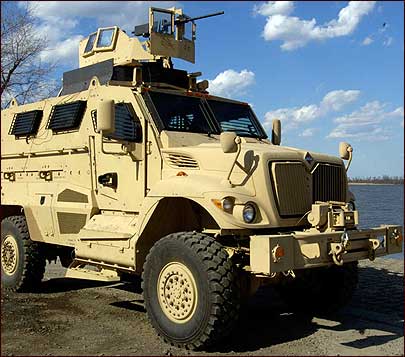
“We have a really aggressive delivery program with this MRAP,” says Rex Baldwin, IT project lead for Navistar Defense. The manufacturer produces approximately 500 MRAPs per month, costing about $500,000 apiece. “Each vehicle looks the same,” he says, “and we found it was taking lots of time to locate the vehicles in the various processes. It was very discouraging to us, and we were using labor to accomplish this.”
Several times per day, two employees had to walk through the company’s yard and buildings—spanning more than 1 million square feet, indoors and out—and write down each vehicle’s location. That information then had to be copied onto papers handed out to managers for review at production control meetings. Because the collected data was only a snapshot of vehicle locations, however, it was often outdated by the time the meetings took place.
“It was all taking so much time,” Baldwin says, “so we began searching for technology to help.” He and his colleagues toured Nissan North America‘s Canton, Miss., factory, where the car maker is utilizing WhereNet’s RTLS to track inbound auto parts, as well as new vehicles rolling off the assembly line (see Nissan North America Installs RFID-based Real-Time Locating System). “That opened our eyes to the possibilities,” he states.
In January 2008, Navistar Defense implemented the RTLS, which includes 400 reusable 2.4 GHz active RFID WhereTag tags, five wireless WhereLAN location sensors and 13 WhereLAN locating access points. A tag is affixed to a vehicle’s chassis, and every four minutes, it emits the unique ID number encoded to it. The location sensors capture that ID number and transmit it wirelessly to the access points. The implementation also incorporates six WherePort exciters that trigger the tag to emit a signal when the vehicle to which it is attached passes one of three gates: an inbound gate, another at the road test site and an outbound shipping gate.
By tracking the vehicles’ location in real time, Navistar Defense can determine where a vehicle is located within a particular process at any given time—such as initial painting, mounting the body and roof, installing the turret, finishing the inside trimming and adding the interior equipment, inspecting the vehicle, or testing it.
In addition, Navistar Defense can review the location data to determine how long vehicles spend in each process. That type of information is currently being used to help the firm improve its processes. “We are looking at, for example, how we can change our paint flow to improve that process,” Baldwin says.
According to Baldwin, Navistar Defense no longer requires two employees to walk the premises and manually record each MRAP’s location. “Now,” he says, “we are able to utilize that manpower in different areas, and that is one savings we can clearly cite.”
WhereLAN locating access points comply with IEEE 802.11 Wi-Fi standards, and can be utilized to create a wireless LAN that works with Wi-Fi-enabled devices such as telephones, laptops and handheld bar-code scanners. By installing the WhereNet system, the company estimates it has saved approximately $40,000 by not needing to install other hardware to communicate with its peripheral buildings.
“Once we did this,” says Jim Mady, an assistant program manager with Navistar Defense, “we didn’t have to add more access points, and now we can communicate wirelessly with the outlying buildings.” The company wanted to be able to communicate with the inspections building, for instance, and it would have cost $20,000 to run phone and network cables to that facility. “WhereNet lets us link to that building and communicate with it wirelessly,” Mady says.
Perhaps the greatest benefit, Baldwin notes, is the assurance that vehicles will be delivered on time. “Before we put in WhereNet, we were always worried that we would come to the end of the month and not be able to locate that last truck to meet our end-of-the-month goal—and you don’t want to be in trouble with the government,” he states. “We kind of laugh, because before WhereNet, we were always running around counting trucks. We wanted to know where they were at all times.”
The implementation has sparked interest among Navistar’s other subsidiaries as well. “The word is out,” Mady says. “Others have heard we have this solution. Our commercial truck subsidiary is looking at how they could utilize something like this.”