U.K.-based aerospace manufacturing and logistical services firm Daher Aerospace is managing its fleet of reusable containers via a radio frequency identification solution provided by Waer Systems Ltd. The system consists of passive EPC Gen 2 ultrahigh-frequency (UHF) RFID tags affixed to containers, as well as fixed readers at key portals through which containers pass, and cloud-based software to manage the collected read data.
Daher Aerospace’s Supply Chain Reusable (SCR) program consists of 22,000 containers (16,000 of which are in transit at any given time) that aerospace parts makers use to transport engine components to assembly lines. The empty containers are then returned to Daher for maintenance and cleaning before that cycle is repeated.
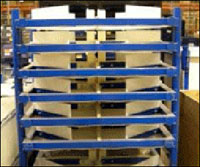
To accommodate the various types of engine components, the company offers the containers in a variety of sizes and materials, such as metal, plastic or wood. Engine-component suppliers require a specific set of containers (known as a kit) to fulfill a particular customer’s order, and if those containers are unavailable, the manufacturer’s operations may be put on hold.
The previous RFID system tracked when each container arrived at and left Daher’s container-maintenance site, enabling the company to capture and store data regarding any changes made to a kit. The low-frequency (LF) tags the company had been using were recognized only by Daher’s own system, and thus served no purpose to others in the supply chain that lacked the same technology. In addition, says Olivier Innocenti, Daher Aerospace’s logistics engineer, the company had been using a Microsoft Excel spreadsheet to manage the RFID data, making the process too time-consuming.
Daher sought a new solution that could reliably read passive EPC Gen 2 UHF RFID tags attached to containers composed of several different materials (including metal, plastic and wood) via fixed readers as those containers passed through portals. The company also sought a tag that could be more permanently attached to containers than the bar-code and RFID labels it had previously been using. Those labels could not resist washing and pressure vapor processes, and could become covered by a variety of other labels applied by suppliers and customers as the containers transported components. During the cleaning process, Daher removes all the extra labels.
In 2007, Waer Systems provided Daher with its Waerlinx warehouse-management solution. Three years later, Waer installed an RFID system that employed passive EPC Gen 2 UHF tags at the sites of several of Daher’s customers, and to monitor Daher’s work-in-progress packaging services, during which 2,000 Daher trolleys are tracked via RFID while moving through a customer’s plant. So Daher requested a UHF system to replace its existing LF technology, in order to manage all of its reusable boxes.
The company tested the RFID technology with read-related data stored on a cloud-based server, prior to installing the solution in a permanent deployment at the end of 2013. “An exhaustive test of all aspects of the system—hardware and software—has been done to check the solution before the ‘go live,'” Innocenti says.
First, a Smartrac DogBone tag is applied to each box’s exterior. The unique ID number encoded to the tag is then linked to that box’s serial number in the Waer software.
As Daher receives empty containers returning from an assembly site for the purpose of cleaning and maintenance, the company reads the tags and updates the containers’ status as “in.” If a container must be placed in quarantine—meaning it requires specific servicing—its tag is again read to indicate which process the container is undergoing. Several other points in the cleaning and maintenance process also include interrogating the tags via a fixed reader. Daher Aerospace and its suppliers are utilizing Motorola Solutions FX7400 readers.
“[Read] locations can be added at any time if required,” Innocenti states. Prior to the new system’s installation, RFID read data was managed via spreadsheets and had to be manually checked by personnel at that location. Not only does the Waer software manage data indicating where containers are located, but it is also designed to ensure that each kit is shipped appropriately. When an aircraft parts supplier prepares to ship a kit back to Daher’s maintenance site, the kit passes an RFID reader. If the software detects that the kit is missing some of its containers, it can issue an alert indicating which containers are absent.
Since the new UHF-based system was taken live last November, Innocenti says, Daher has streamlined the operation and administration of data related to the movements of containers. The system reduces the risk of human error, both at the Daher plant and at supplier sites, and enables the collected information to be shared between Daher, its customers and suppliers, thereby ensuring that containers are located where they are expected to be.
In the future, Daher intends to install touchscreens at read locations. This, the company explains, will enable employees to enter such data as the quantity of containers and validation of an action at each read point.