Among the tasks related to the maintenance of an aircraft—whether commercial or private—the process of tracking tire air pressure is one of the more frequent and time-consuming. Whether the task is performed via a manual pressure gauge or using a wired onboard sensor device, aircraft owners and operators must check that all tires are properly inflated on a regular basis—typically, every day or two. Manually measuring tire pressure on a single aircraft usually requires approximately an hour to complete.
Throughout the past seven years, some airlines and private jet operators have been employing a radio frequency identification-based solution provided by Crane Aerospace and Electronics to track that information. At the request of a major aircraft company that has asked to remain unnamed, Crane is currently seeking Federal Aviation Administration (FAA) certification for the use of its RFID-enabled SmartStem wireless tire-pressure monitoring system (TPMS).
To check tire air pressure, aircraft operators are required to follow the maintenance manual that comes with each airplane. Onboard systems measure pressure and display data in the cockpit, but not all planes come wired for that particular feature, and some operators still manually check pressure since they find the onboard systems to not be as accurate. When the standard pressure manual testing method is used, some air is released from the tire every time that it is tested. Therefore, the tire needs to be periodically re-inflated, in order to replace the accumulation of lost air. Not only can this be time-consuming, says Eric Haas, Crane Aerospace and Electronics’ director of business development, but in the long term, it can affect the length of the tire’s life.
Crane’s solution is a sensor that replaces the wheel’s standard fill valve. The company (or its resellers) provides the sensor to aircraft manufacturers—who then fit the gauge into tires for customers—as well as to the aircraft operators themselves. The gauge is interrogated via a handheld RFID reader that captures temperature and pressure data, along with the sensor’s unique ID number. The technology developed by Crane includes readers and tags supplied by Colorado wireless sensor company Phase IV Engineering. Only the Crane reader can interrogate the gauge’s RFID tag.
The TPMS sensor comes with Phase‘s IV SensIC passive 134.2 kHz chip, which has a unique ID number encoded on it that is linked to details regarding the aircraft itself, stored in software on the handheld. Although the SmartStem system employs LF RFID technology, Crane does not use the term RFID to describe its technology (based on a concern that its customers might incorrectly assume that RFID always uses a high- frequency transmission band). This is a very important distinction, according to the company, since the company’s customers could believe that high -frequency RF transmissions that could interfere with cockpit operating systems.
The gauge also includes a pressure and temperature sensor, and the reader simultaneously captures the measurements from those sensors. The collected data is then displayed on a screen on the front of the device, and the handheld’s data records can be uploaded to a PC for maintenance tracking via a USB or Bluetooth connection.
Identifying the proper technology for the solution proved challenging, Haas recalls, due to the environment in which the sensors would need to operate. The temperature variation, shock and vibration to which the tires are exposed, he notes, have made it impossible to install a device requiring batteries, such as active RFID. Instead, with the passive solution, the reader’s inductive signal powers up the RFID chip, which retrieves temperature and pressure data and then forwards that information to the reader. The chip’s 1024 bits of memory can store other data as well, such as the tire’s location on the aircraft, thereby enabling users to better track which tire is mounted on a particular wheel on the plane, as well as how it is performing, based on the temperature and pressure readings.
Users can also conduct other historic data analysis, using their own software program or a simple Microsoft Excel spreadsheet. In that way, they may determine how well tires are performing, which ones need to be refilled more often, and thus when they may require replacement.
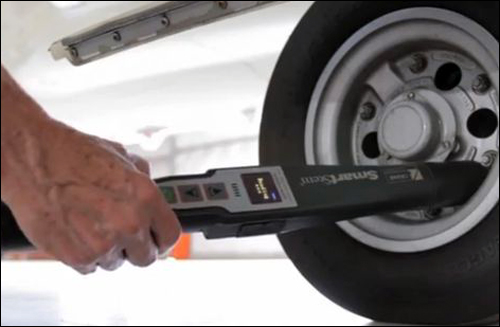
The SmartStem system is already certified for use on certain types of aircraft, Haas reports, and is currently being utilized by several private jet companies and airlines. Private jet operators face unique challenges when it comes to monitoring tire pressure, he says, since that process typically must be performed by an FAA-certified mechanic. In some cases, he notes, “these aircraft are flying in and out of remote locations,” requiring that such a mechanic be transported to those remote locations to test tire pressure before the jet can be cleared to fly. With Crane’s TPMS technology, however, the process can be carried out by a pilot.
Crane is presently seeking FAA certification to install the gauge on several additional types of aircraft—not only for the private jet industry, but also at the request of an aircraft manufacturer. The solution is currently available for the Bombardier Dash, in addition to multiple Cessna and Learjet models. The company expects to soon have the technology available aboard several Boeing aircraft, as well as on Airbus‘ A320 family of airliners.
Users can purchase a kit that includes a handheld reader, a charger and written instructions for use. Crane sells the solution directly to customers, as well as through suppliers or aircraft original equipment manufacturer (OEM) companies.