Micro-Clean, a clean-room services provider based in Bethlehem, Pa., has adopted an RFID system to help it track the status and calibration of the company’s air-testing tools and equipment at its own tool-calibration laboratory and tool warehouse, as well as monitor work performed at customer sites. The company is considering offering the technology to its customers as well, so that they can identify where their own air-filtration and related equipment is located, and when it was last serviced or maintained. The RFID solution, known as Micro-Clean Identification (MCiD), was developed by Verigenics.
Clean rooms are enclosed spaces in which highly sensitive work is carried out, such as the manufacture of pharmaceutical, veterinary or bioscience products (vaccines, for instance), and in which particulates, contaminants and pollutants must thus be kept within strict limits. Companies that operate clean rooms often work with Micro-Clean or other service providers to use tools (such as sniffers that count the number of particulates in the air) to periodically test the air quality within those rooms, as well as the functionality of air filters and other equipment used to ensure the air’s cleanliness. Not only must companies that operate clean rooms be able to provide proof to regulatory agencies, such as the U.S. Food and Drug Administration (FDA), that the equipment is tested and serviced as required, but they also need to prove that the air-testing tools used onsite have been properly calibrated.
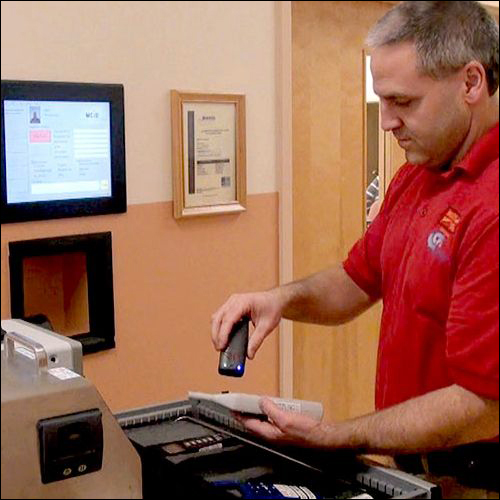
In the past, when it came time for Micro-Clean’s tools to be calibrated, the company’s technicians had to search for those tools, and then refer to a handwritten logbook to identify where those items were last located and who was using them. Calibration technicians often sent e-mails and made phone calls to field technicians to ensure that those tools were always calibrated in a timely fashion. If a clerical error was made, such as the wrong serial number being written down for a specific tool, locating that item and its records could become more difficult.
The rules related to clean-room tool calibration have become stricter throughout the years, says John Wagner, Micro-Clean’s CEO, following recall events in which products may not have been made according to proper clean-room specifications. Consequently, he adds, “We have to have complete traceability for everything we do,” so that the firm can prevent any tool in need of calibration from being used at a customer’s site, as well as provide proof to customers that the tools are calibrated. This requires time-consuming paperwork administration on the part of workers.
However, Wagner says, since adopting MCiD, Micro-Clean has achieved a return on its investment based on labor costs alone. In fact, he reports, clerical labor has been reduced by about 88 percent.
In 2012, the company first began working with Verigenics on a solution. Verigenics is the RFID division of NewAge Industries, one of Micro-Clean’s customers. Wagner brainstormed solutions with Jeff Johnson, Verigenics’ director of auto-ID solutions. Micro-Clean’s technicians, Wagner told Johnson, typically loaded tools specific to each worksite onto carts, and then transported the carts to those sites by van. Wagner posed the idea of employing RFID to track those tools as they went out and were returned, and shared the idea with Micro-Clean’s technicians, whom he says were enthusiastic. Verigenics then began tagging several thousand tools with high-frequency (HF) 13.56 MHz passive RFID tags compliant with the ISO 15693 standard. Verigenics uses a variety of metal-mount, nylon or epoxy-encapsulated tags provided by multiple vendors, Johnson says.
Verigenics installed three reading stations at Micro-Clean’s tool warehouse and calibration laboratory—one at each of the two tool check-in and check-out areas, and the third on the lab’s workbench. Each reading station consists of a touchscreen mounted on the wall, a tablet computer built by a third-party manufacturer according to Verigenics’ specifications, and a Datalogic Element Bluetooth handheld reader (the Element reader is no longer being sold by Datalogic).
A field technician first fills a cart with the tools to take to a particular customer site, then wheels that cart to Micro-Clean’s checkout station, enters his ID number via the touchscreen and uses the reader to capture each tool’s tag ID. When a tag is interrogated, the station’s touchscreen displays a description of that tool and its serial number, based on the tag ID stored in the MCiD software. The software determines whether that tool is nearing its calibration date and indicates an alert if it is.
Once all of the tool tags are read, the technician presses a prompt to end the checkout process, and the software, residing on a local server, stores data indicating who has removed the items, as well as when this occurred. The system then prints a manifest for the technician to take to a customer’s site to prove that the tools have been calibrated.
When returning the tools, the technician uses a similar process, by following the prompts on the station’s touchscreen, reading each tool’s tag, and indicating whether that tool is being returned to storage, or is being sent to the calibration area or service department.
When conducted with pen and log books, the manual check-in or checkout process typically took about 15 minutes per cart. With RFID, Wagner reports, the same task now takes two to three minutes to complete. This alone has saved the company approximately $200,000 annually, he says.
At the calibration lab, a technician uses the reading station to capture a tool’s tag ID, and the MCiD software then shows which calibration tasks need to be carried out. Once the work has been completed, the technician uses the MCiD software to record which tasks have been performed, and then returns the tool to the warehouse. The RFID-based documentation process takes about one minute, while filling out paperwork related to each tool calibration required about three minutes.
This year, the company launched into the next phase of the deployment, by attaching RFID tags to equipment in the clean rooms serviced by its technicians. Thus far, Micro-Clean’s technicians have tagged about 6,000 items. In the past, the company simply attached an adhesive sticker with its name and contact information printed on it, at the customer site. Now, its technicians are applying RFID sticker encoded with an ID number linked to data regarding the customer and the piece of equipment to which that sticker is attached. When Micro-Clean’s workers visit a customer’s site, they bring a tablet with a built-in RFID reader to capture each tag’s ID and conduct their inspection and tests, and then input information into the tablet about the service being provided. The tablet has a Wi-Fi and cellular connection so that it can send synchronized data back to Micro-Clean’s server on a regular basis.
Previously, Johnson says, technicians prepared their reports by entering equipment and customer information into a form on their laptop, which required five to six minutes to complete. That process now only takes about 20 seconds, he adds.
At any time, technicians can upload the RFID-based data indicating what was done at each customer site. In that way, Micro-Clean can store the history of each piece of equipment for the customer, as well as for its own needs.
In the future, Wagner speculates that Micro-Clean could sell the RFID functionality to customers as a value-added service. This would be the third phase of the MCiD deployment. In that case, a customer would pay a fee to access data related to each piece of tagged equipment within its clean room. The customer’s own workers could use an RFID reader or RFID-enabled smartphone to interrogate the RFID sticker of a particular piece of equipment, and then view that item’s service history and the dates on which it is due for testing, servicing or replacement. The system could also enable a customer’s workers to read a tag on an air-filtering unit, for instance, and view which components are installed inside it, thereby enabling them to locate a specific item they seek, such as a recalled filter part.
Wagner notes that some of Micro-Clean’s customers have thousands of air-cleaning units onsite, and that tagging each of these units, or the components inside them, could make their management easier not only for Micro-Clean, but also for the customer. The company is now discussing this option with its customers and will proceed according to their interests.