Computers & Communication Technology (CCT), a Beirut-based developer of business process management (BPM), enterprise content management (ECM) and 3D-based project-control solutions, is overseeing a variety of pilot projects involving the use of passive and active RFID tags to manage construction sites operated by global construction firm Consolidated Contractors Co. (CCC).
Computers & Communication Technology, a subsidiary of CCC, provides integrated automatic data acquisition software using mobile technologies. The company is currently testing a combination of passive and active RFID tags in an application for managing the movement of CCC’s personnel onto and off of its sites within the United Arab Emirates (UAE), while also monitoring the locations of pipe spools—fabricated sections of piping—at an oil and gas construction site in Qatar. In addition, CCC launched a pilot in Oman earlier this year that utilizes passive ultrahigh-frequency (UHF) RFID tags to track personnel, and it intends to track thousands of spools at a site in Siberia by this summer. CCT also provides RFID consultancy and systems integration services to other companies.
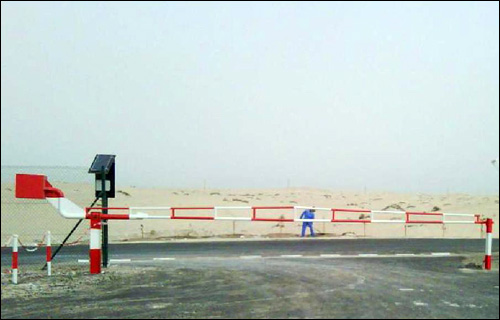
Headquartered in Greece, CCC operates construction sites throughout the world. The company currently has approximately 22 projects underway, including new oil fields, airports, sewage systems and electrical grids. In 2004, the firm began seeking ways in which to increase efficiency, by automating the capture of data regarding the arrivals and departures of personnel onsite, as well as the locations of pipe spools and other materials received (and, in some cases, painted or sanded), and then used on a worksite.
In the UAE, CCC is employing passive EPC Gen 2 UHF RFID tags attached to vehicles, in addition to proprietary active 2.4 GHz RFID tags embedded in personnel badges, in order to monitor who enters and exits CCC’s construction site in Abu Dhabi, according to Khaled Al Shami, CCC’s RFID deployments project manager and CCT’s software development project manager. CCT began by testing passive UHF RFID tags on the badges of personnel passing through an entrance gate, then battery-assisted passive (BAP) tags and finally active tags to track the movements of individuals and goods at a series of sites. CCT, he says, has employed a variety of RFID hardware vendors for the CCC deployments, and continues to experiment. By tracking who comes and goes from the site, the firm is able to reduce the amount of time consumed at entry gates, as well as calculate payroll and ensure that everyone has been evacuated from the site in the event of an emergency. At this point in the project, however, the company is still testing technology to simply ensure that tags can be read as people come and go, and that CCC’s software can store that data.
Every worker at the UAE site wears a badge containing an active RFID tag that transmits a unique ID number linked to that individual’s identity in the back-end software. A total of 500 people are carrying the badges as they arrive and leave through a gate, in both cases riding in an enclosed vehicle. Although the company tested passive and BAP tags, it found that only active tags provided the read reliability required for an individual moving through a portal while in a truck or other vehicle. There are six gates in use—three at the construction site and three at the workers’ camp—each about 15 meters (49 feet) wide. At every gate, CCC installed two RFID readers, powered by a solar panel and featuring 3G communication technology to transmit data to the back-end system. “There are no wires at all,” Al Shami explains. Passive UHF EPC Gen 2 tags are also applied to the exterior of some vehicles, and the gate readers capture each vehicle tag’s ID number, which is linked to information about that vehicle’s operator.
The company has had to consider its processes, as well as the hardware’s functionality, in order to ensure that the system functions properly. For example, Al Shami says, to encourage workers to always carry their badges, CCT has linked the tag read data to payroll, to provide payment to staff members automatically—but only if they are carrying their badge to prove they were present. To ensure that no one brings an extra badge for an absent worker, a guard can be stationed at the gate to count the number of individuals within each vehicle, and then compare that headcount against the number of tag reads displayed on a computer running the software.
In Oman, CCC is presently carrying out a pilot project employing passive EPC Gen 2 UHF RFID tags worn by staff members. In this case, workers arrive in buses, not in individual vehicles, and disembark from those buses before walking through a turnstile entrance, where each tag is read at a range of about 1.5 meters (5 feet). This pilot, Al Shami says, is still in its early stages, but will include 3,000 workers at three sites.
Additionally, CCT is working on a project utilizing RFID to manage materials at worksites. The company has begun testing the technology in this use case by applying active RFID tags to pipe spools, which arrive at a construction site in sections that are painted, sandblasted and inspected prior to installation. Tracking each process, as well as locating spools onsite as needed, is critical but can be time-consuming. Prior to RFID’s deployment, the company exclusively used pen and paper to manually track which materials entered the site, in addition to which processes have been undertaken on those spools, and when each was used for the construction project at that site.
Initially, the company applied bar-coded labels to pipes and spools to be used at industrial sites, including oil facilities, and workers utilized scanners to create a record of where parts were located, or when they were used for the construction project.
That system, Al Shami says, provided a good record of material arrival or other processes. However, he notes, “There were some limitations with bar codes. The labels could get scratched.” What’s more, he adds, when stored in laydown yards, the materials could become damaged by humidity or sunlight, or end up covered in snow, ice, sand or mud, making the labels that much more difficult to read.
The spool-tracking solution, called Pipe Guard, is being provided by Dhatec, and consists of active 2.4 GHz RFID tags known as Smart Points, readers called MicroRouters, and a gateway to receive read data and link it to the Web-based Pipe Guard software. Data can be accessed via a smartphone, tablet or PC at any location at which there is an Internet connection. In the future, CCT intends to integrate the Pipe Guard software with CCC’s Talisman software for tracking construction materials, so that RFID data could be used to update material inventory and process reports at the construction site. In July 2012, Al Shami says, the firm began attaching the tags to some of its spools, which are then stored in a single laydown yard about the size of a soccer field. There can often be tens of thousands of items within a laydown yard, he notes, that are moved through various processes, such as painting and sanding, before being built into the facility under construction (in this case, a gas liquefaction plant).
When goods are tagged, employees input information about the spool, such as its dimensions, and store that data, along with the tag’s ID number, in the Pipe Guard software. A network of readers have been installed around the laydown yard and processing areas (such as the paint shop). Each tag also comes with a motion sensor. When stationary, the tag remains dormant; however, if the sensor detects that the tag is moving (for example, if an item is lifted by a truck to be delivered to another area), the tag begins beaconing, thereby providing its ID number. The readers capture that ID at a distance of up to 50 meters (164 feet), and the software determines that tag’s location based on triangulation, as well as by the strength of the tag’s signal as received by each reader.
The Pipe Guard software can then display the real-time locations of items within the laydown yard or processing areas. The software also stores status data about each part, based on its location. For example, if a spool’s tag is no longer read in the paint shop, the software can update that spool’s status as having been painted. In this way, management can view which parts may be delayed, and which are ready for the next phase, such as being built into a construction site’s structure.
The company intends to use the system to track more than 10,000 items at a Siberian construction site beginning in May 2013.
To date, based on all of the projects underway, Al Shami says the RFID technology shows promise as a means to automatically identify materials and personnel. “I’m very motivated when it comes to RFID,” he states. The major concern for which the company continues to test is the hardware’s durability. The harsh conditions, including temperatures of 60 degrees Celsius (140 degrees Fahrenheit) in Qatar and -40 degrees Celsius (-40 degrees Fahrenheit) in Siberia, pose a challenge both for tags and readers.
CCT presently seeks a partnership with a company that could assist with the further development of solutions in material management. “We don’t need an (RFID) manufacturer—we want a solutions provider,” he says, noting that developing a working system requires some work onsite that takes into account the conditions at that location and the processes used by workers. “If you just buy an RFID system without knowledge [about how it will be used], it will not be deployed properly and it will fail,” he states.