Having completed proof-of-concept tests over the past few years that resulted in the Federal Aviation Administration‘s decision to allow passive RFID tags to be placed on aircraft components, Boeing and FedEx have begun a proof-of-concept test to seek the FAA’s approval to place active UHF RFID tags on aircraft parts. This approval is important because without it, a carrier would be liable if equipment on a plane did not function properly due to interference from the active tags.
On Wednesday, representatives from the two firms installed a total of 50 Identec Solutions IQ-8 battery-powered UHF tags on various components of an MD-10 cargo plane—the same plane used for a proof-of-concept test for high-frequency (13.56 MHz) passive tags in 2003, and for tests involving ultrahigh-frequency (UHF) passive (915 MHz) tags. As that plane took off Wednesday night, it was the first non-military cargo aircraft on record to carry transmitting UHF RFID tags, according to the companies.
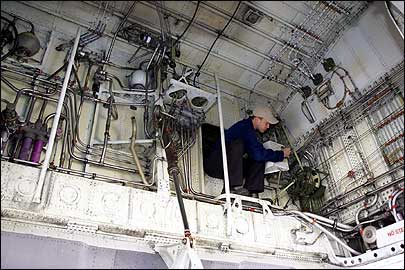
“We are making history,” says Ken Porad, program manager of the automated-identification program for Boeing Commercial Airplanes Group. “If we can use active tags on flights, that sets the stage to begin deploying wireless sensor networks, in which things like temperature sensors could be attached to the tags and used to monitor perishable goods in transit.”
Such technology could provide significant benefits to shipping companies such as FedEx, as it would allow greater monitoring of goods in transit. For Boeing, the use of active tags with sensors would improve visibility into the conditions to which airplane parts are exposed during flight. “We could watch things like the gravity forces on landing gear,” he says.
Some of the IQ-8 tags used in the test have integrated temperature sensors, so these will also log the ambient temperatures in their vicinity.
Of the 50 tags installed on the plane, 40 are set to beacon mode, transmitting a signal once every three seconds. “This is showing a worst-case scenario,” says Barry Allen, Identec Solutions’ vice president of engineering. That is, having the tags transmitting data almost constantly allows the proof-of-concept test to create the potential for causing electromagnetic interference with a plane’s instrumentation and communication systems.
If tags were being used for a real business purpose, such as for parts tracking or supply-chain management, they would not be set to beacon mode during flight because there would be no business benefits in doing so. There would also not be any business value in interrogating the tags during the trip, since the parts, assets or products to which the tags would be attached could not be removed to have maintenance done to them while in flight.
Because the RF power emitted from the tag is measured at 1 milliwatt, the FAA believes the tags will not result in any interference with the plane’s electronic flight instrumentation and communications systems—either on the ground or in the air.
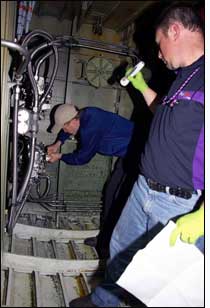
Porad and James Ford, manager of engineering support for FedEx, both assert that the probability of active tags interfering with the plane’s electronic instruments and communication systems is virtually nil. “A tag transmits one one-thousandth of a watt,” says Porad. “Compare that with a cell phone, which emits 500 milliwatts.” The FAA agrees with the assessment that transmitting tags are likely benign to a plane’s operation, at least enough so as to condone the presence of transmitting tags on the in-service plane used in the test.
Still, FedEx will watch for any anomalies that may occur during the plane’s day-to-day flight schedule during the 90 days for which the tags will be transmitting an RF signal. The IQ-8 tag operates at 915 MHz, a frequency unused by any crucial on-board avionics or satellite communications equipment. FedEx will report any irregularities to the FAA. According to FedEx, the pilots would be alerted to the presence of the tags on the plane.
Throughout the 90-day period, FedEx engineering staff will inspect the tags to ensure that they remain securely fastened to the parts. To attach a tag, staff cleaned a section of the part. Once the part was dry, a layer of silicone adhesive was spread on the part, atop which a tag was manually applied. The IQ-8 tag has a plastic housing and can withstand both high and low temperature extremes. Neither Porad nor Ford expects the tags to suffer any environmental damage from exposure to heat or cold during flight.
In mid-August, at the end of the 90 days, the 40 beaconing tags will be switched off beacon mode. The 10 remaining tags—newer versions of the IQ-8 that can not be set to beacon—will be utilized for the second part of the test, which will last from mid-August to mid-September. This part of the test will entail reading and encoding data to the 10 tags, which hold 8 kilobytes of memory apiece.
The parts chosen for this and the previous tests are all repairable devices that FedEx must regularly put through a maintenance cycle. In the future, if FedEx deploys an active or passive RFID system for parts-tracking, it may track some of these items, as well. For the purposes of the test, however, the parts picked to tag were chosen because they are easy to access. The company is also studying the possible benefits of using RFID to track spare parts in inventory, as well as assets in maintenance facilities.
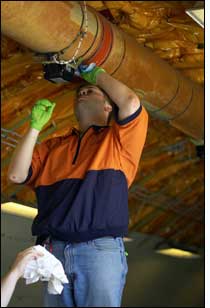
“We’re hoping RFID can improve parts visibility and parts lifecycle visibility,” says Ford. “The aircraft records department keeps track of hundreds and hundreds of parts, and if we could throw RFID tags on those parts, it would reduce the workload [generated by tracking them] significantly.”
“We want this test to be successful because we’re sick of chasing parts,” said Ray Hanshew, senior data technician for Federal Express’ air-operations division.
Following the protocol of the passive tests, the testers will ensure that the data encoded to the tag—its serial number, the name of the part and the area on the plane where it is placed, such as flight deck or main cargo compartment —can be read. They will additionally test that the tag can be written to. FedEx is not yet sure what additional data testers will write to the tag.
For the purpose of the test, FedEx engineers will use a laptop containing an Identec Solutions i-CARD 3 RFID interrogator card, which fits into the device’s PC card slot, and an external antenna to read and write to the tags. Silverstroke, a German provider of auto-ID middleware and application software, has written demonstration software specifically designed for encoding and reading the tags being tested.
After the 120 days of testing, Porad will work with the FedEx staff to collect the results and comments generated from the project, and collate them into a write-up for the FAA. “I’ll submit a report, asking for certification from the FAA [to allow active UHF tags to be placed on flights] within 30 days of the test’s completion,” Porad explains, adding that he’s hoping for a quick response from the FAA.