During the past decade, RFID has emerged as a valuable way to track assets and inventory, manage processes and oversee supply chains. But beyond the documented benefits, including boosting efficiencies and lowering costs, is an entirely different but important value proposition: tapping RFID to improve regulatory oversight and compliance.
“Organizations find it increasingly difficult to stay on top of regulations and put the necessary processes in place to manage compliance risk,” states Anthony Monaco, a partner and service line leader for regulatory compliance at auditing specialists KPMG. “RFID can play an important role.”
To be sure, the list of government and industry regulations worldwide expands daily—it includes the Sarbanes-Oxley Act, U.S. Department of Defense and U.S. Food and Drug Administration regulations, Federal Aviation Administration and European Aviation Safety Agency requirements, national programs to monitor livestock and the European Union’s Forest Law Enforcement, Governance and Trade plan to address illegal logging. For organizations venturing into the global arena, the risks, challenges and responsibilities are multiplied. RFID can improve accuracy while dramatically reducing the time required for auditing. “It represents a giant leap forward,” says Michael McCartney, managing principal at QLM Consulting, which specializes in supply-chain management.
Some organizations, large and small, are adopting RFID specifically to meet government regulations. The Hong Kong Housing Authority, for example, mandates that all contractors use RFID to control the quality of building materials, track the building process and make building maintenance systems more efficient. Contractors must collect logistics and manufacturing information and deliver the electronic records to the Housing Authority. Hillsborough Community College, in Hillsborough County, Florida, adopted RFID to track nearly 17,000 assets on five campuses to meet annual state and federal government audits.
Other organizations are adopting RFID to drive operational efficiencies and then finding they can use the system to meet government regulations. “In many cases, a compliance project that incorporates RFID can grow out of existing RFID systems,” says Patrick Javick, GS1 US‘s industry engagement director.
Mining companies worldwide, for example, are using RFID to automate manual processes, streamline production and reduce costs. With an RFID infrastructure in place, they are also using the technology for personnel tracking, which is required in Sweden and other countries. Brazil’s Alog Data Centers deployed an RFID solution to automate its operations and processes at four facilities, to improve inventory accuracy. The solution also provided a more efficient way to comply with new international standards mandating periodic fixed-asset reporting and auditing for IT service firms that have public companies as clients.
Companies that are developing a business case for an RFID project—or those piloting an RFID system—should factor in the cost of complying with government and industry regulations. “RFID in conjunction with sensors and data analytics introduces highly accurate monitoring and reporting functions,” says Diana Hage, CEO of RFID Global Solution. “Today, corporations must look to meet regulations in the most cost-efficient manner, and the technology exists to dramatically improve processes.”
Although many organizations haven’t yet begun to use RFID to automate compliance processes, significant opportunities lie ahead. “Over the next few years,” McCartney says, “we will begin to see RFID used far more extensively for managing regulatory compliance.” But developing a strategy and building a framework to support an advanced compliance model requires careful planning. As with any RFID project, it’s essential to thoroughly understand underlying processes and workflows and where opportunities to automate data collection exist. It’s also critical to choose the right hardware, software and data-sharing framework to support an initiative.
Managing Risk
For many organizations, regulatory compliance is a hit-or-miss proposition. Conducting audits with manual counts or bar-code scans typically produces inconsistent and undependable results. In addition, spreadsheets and specialized compliance software often take a cookie-cutter approach that doesn’t address an organization’s specific requirements. Another challenge is that “many legacy systems do not provide any information about the physical location of an asset,” says Tom Manzagol, president and founder of RFID Global Solution, “and this often makes it difficult to correct a problem.”
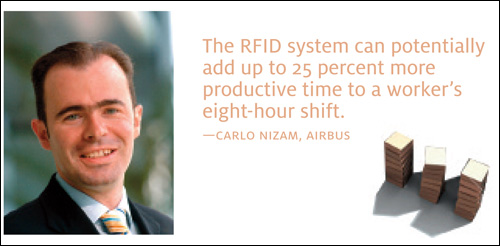
The end result is data that provides an incomplete view or lags behind actual business conditions by days, weeks or months—and, consequently, interferes with an organization’s ability to take action quickly and decisively when a compliance issue arises. This, in turn, may lead to public health or safety risks, government fines and other penalties, bad press, lawsuits and, in the end, a tarnished brand image and financial losses.
The problem is compounded by the fact that many organizations, especially those that operate in a global environment, aren’t set up to track new regulations and implement required compliance systems in a timely manner, KPMG’s Monaco points out. During the time an organization is playing catch-up—sometimes weeks or months—risk can spiral out of control. Manual counting systems and spreadsheets hinder a company that needs to move rapidly to get critical compliance capability online, he says, and they aren’t cost-effective at reducing risk in a systematic way.
RFID automates manual processes, which are error-prone and inefficient, and it reduces or eliminates inaccurate inventory audits. “Suddenly, it’s possible to know that you’re nearly 100 percent compliant,” Manzagol says. “There is a significant reduction in risk.”
In addition, RFID standards have been solidified and the technology has matured to the point that tags, readers and other equipment work seamlessly, and past compatibility issues no longer exist, says Monty Cook, VP of sales at GlobeRanger. This includes the emergence of GS1 standards for capturing, handling and storing data.
Developing a Smart Strategy
In fact, now that there is a robust RFID framework in place, GS1’s Javick believes RFID is about to take off in the regulatory and compliance space. In retail, for example, it can aid in tracking where goods originate, what countries they pass through, where additional processing and work is taking place and where the goods arrive for sale. Producing compliance records and tax data is greatly simplified. The end result is “faster and far more automated processes related to validating manifests and handling government filings,” he says. “RFID can provide very granular data about processes and how they intersect with regulations.”
Pharmaceutical manufacturers and their logistics providers are using RFID sensor tags to monitor temperature-sensitive biomedical supplies and other life-sciences products. Cold-chain experts believe pharmaceutical and biomedical suppliers will increasingly turn to RFID and other technologies to support regulatory requirements. “If you distill things to a basic level, regulatory bodies want organizations to demonstrate that they have a risk-based approach when it comes to handling pharmaceuticals or biotech or diagnostic products,” says David Bang, CEO of LifeConEx, a DHL Global Forwarding cold-chain-services subsidiary.
Government mandates are also driving adoption in the perishable foods sectors. Growers and manufacturers are gearing up to meet the FDA’s Food Safety Modernization Act, which goes into effect in 2016, and similar EU regulations that require traceability to facilitate recalls. “Growers and food manufacturers will have to tell the story, so it’s possible to know precisely where contamination or a breakdown in processes took place,” McCartney says. “If a company uses RFID effectively, then the entire process becomes a laborless method of tracking inventory.”
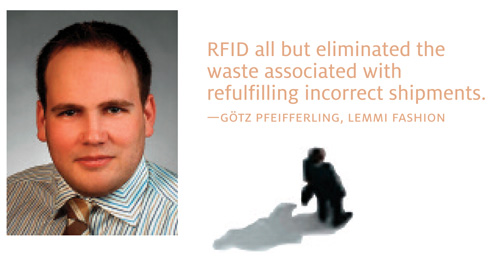
The airline industry is also turning to RFID to address inefficiencies and compliance. Every flight originating in the United States requires an inspection of the life vest located beneath each seat, GlobeRanger’s Cook says. “Every day, for the first flight of the day, a mechanic must check under the seat and make sure the floatation device is in place,” he says. “In a large aircraft, such as a 747 or 777, a mechanic must get down on his or her knees to make sure it is intact and report on it.” Today, the report is typically submitted on paper. What’s more, “if the seal [on the life vest] is broken, the plane cannot leave the gate or the airline faces a stiff fine.” A new sealed life vest is required.
But RFID changes the equation in a major way. “Instead of a mechanic taking 45 minutes to physically check the vests, it’s possible to automate the process and complete it within a few minutes,” Cook says. With the appropriate approvals in place, the RFID-generated inspection report becomes the formal means of compliance with maintenance instructions. “A company can submit a report for FAA compliance simply and easily,” he adds.
In 2013, Delta Air Lines began RFID-tracking oxygen generators to improve inventory visibility and reduce waste associated with expired devices. The solution also reduced the time it takes to verify expiration dates on devices installed on planes from roughly eight man-hours per plane to 45 seconds RFID is being employed to monitor commercial, industrial and hazardous waste. Canadian logistics and engineering company Can/U.S. Enviro-Energy, for example, began using RFID in 2008, to track its battery inventory and provide its telecom customers with visibility into the disposal of their batteries. Before implementing the RFID solution, the company received frequent phone calls from customers asking for paper documentation, which they needed to submit to the Canadian government. The RFID system improved warehouse management and automated data collection, making disposal information available to customers online.
Since SOX was passed in 2002, public U.S. companies have struggled to comply with the law passed to prevent fraud and misreporting of financial statements—and that includes verifying that assets and inventory are in place. “RFID has the potential to provide big benefits for companies, especially those in the financial services sector, that must track IT assets and have accurate counts for specific items,” Manzagol says. This includes servers, storage systems, mobile devices and “ghost assets” that remain on a company’s books even after they’ve been decommissioned.
In the horticultural sector, companies are RFID-tracking returnable transport items to improve operations. European firms can tag trolley shelves and link product data to the trolley’s location, to meet a new EU directive that will require companies to trace edible plants within a couple of hours in the case of recalls, says Léonard Smits, Container Centralen‘s RFID implementation officer. Colorado, Oregon and Uruguay are among the states and countries that have legalized the sale of marijuana and are using RFID to regulate the market. Growers need to tag each plant so it can be tracked from the greenhouse in which it is grown to the store where the drug is sold.
While there seem to be an endless number of government rules that organizations in myriad industries must meet, there also are innovative RFID solutions to address them. India, for example, regulates the storage of grain harvested in that country, to ensure only safe, clean grain is sold for food. Adani Grain Logistics, which operates several grain storage facilities in India, implemented an automated, RFID-based system for receiving, testing and tracking food grain harvested in the states of Haryana and Punjab.
The British government adopted the Construction (Design and Management) Regulations, the Health and Safety Executive’s new body of tougher construction-industry regulations, including stiffer inspections of equipment used in hazardous environments. Metal Decks, a leading U.K. structured decking and flooring specialist, deployed an RFID solution to track maintenance performed on safety nets designed to protect employees from high falls.
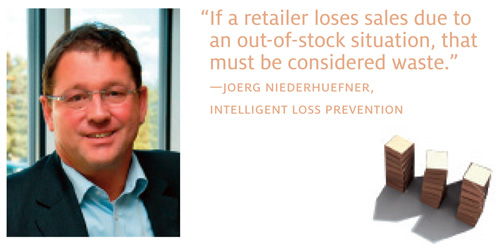
Dominion East Ohio delivers natural gas to 1.3 million customers. One of the company’s responsibilities is to ensure that all aboveground pipelines are properly maintained. According to state and federal regulations, the firm must inspect all pipelines exposed to the atmosphere at least once every three years. The energy firm deployed an RFID solution to reduce the time workers spend collecting and storing inspection data.
Implementing RFID for Compliance
Developing a comprehensive strategy and thoroughly understanding the processes and workflows that intertwine with regulatory and compliance issues is the foundation of a successful initiative. “You have to document every step and process to understand where the tags must be applied, how the data is collected and stored, and how to put it to use effectively,” QLM’s McCartney explains. In many cases, the process may extend to business partners, shipping and logistics firms and others. The end goal is to ensure that no gaps exist and data is accurate and dependable.
The good news, Javick says, is that existing RFID systems already capture most of the data required to manage compliance, and they are able to accommodate reads of items, totes and containers at line speed. It’s simply a matter of identifying the critical data and inserting it into the right software system.
But, Javick notes, it’s still important to turn to an RFID provider that offers a comprehensive solution that’s optimized for your industry or business. “It’s critical to communicate with technology partners about what you’re attempting to do and ensure they have the right framework and focus to generate essential data for compliance and put it to use,” he says. “They also need to understand the differences—and nuances—of regulatory frameworks.”
A strong technology framework may require an organization to modernize databases and software, GlobeRanger’s Cook says, and design better reporting and analytics capabilities.
It may also be necessary to ensure that underlying wireless infrastructure is equipped to handle the data flow. This may mean examining existing cellular and Wi-Fi networks, but also looking to protocols and technologies such as Bluetooth and ZigBee to handle data transfers in specialized locations or when connectivity is interrupted or unavailable.
To connect all the digital dots, organizations need to facilitate discussions that span different departments or groups, including those using RFID and those not yet using it, KPMG’s Monaco says. The evolving business environment requires executive oversight that extends beyond traditional enterprise boundaries, he adds. Particularly at larger firms, there’s a growing need for a chief risk officer, chief compliance officer or director of internal audits to tie together compliance and regulatory requirements with other business initiatives.
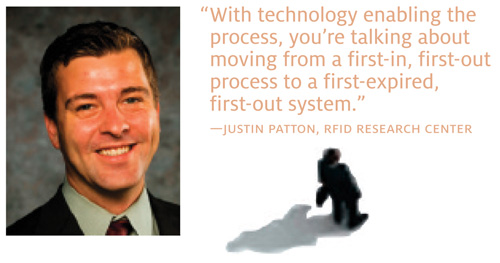
What’s more, to plug in RFID and use it effectively in the compliance space, there’s a need to review and remap existing processes that may be woefully outdated or simply not work in a more technologically advanced environment. “It’s an issue many organizations must revisit,” Monaco says. “It’s really about people and processes more than the technology. There’s a need for a gap assessment as a starting point.”
Another critical issue, Monaco says, is many organizations have crumbling data silos and disconnected systems. As a result, a business may require clouds, specialized APIs to connect systems, and other tools and technologies to break down silos and eliminate spreadsheets and paper records. This, in turn, may require data analysts and data scientists who understand how to put the data to work and match the needs of regulatory agencies and/or industry organizations. “It may require training so people understand processes and workflows, how to use the software and systems, and how to generate data that’s accurate and useful,” he points out.
Monaco says that because many regulations and standards are still in the formative stages and RFID technology is relatively new in the compliance arena, it’s important for businesses to provide feedback to industry associations and state and national governments regarding draft regulations and how RFID can be used effectively. Playing a role in the development of the future regulatory framework can ensure that workable government industry standards emerge, he says.
“Many companies in various industries are going to discover, during the next several years, that it will become increasingly difficult to manage regulation and compliance tasks without RFID,” QLM’s McCartney says. “RFID is ready to tackle the task. The technology is mature enough to move beyond asset-tracking capabilities and address sophisticated regulatory and compliance challenges. It’s now up to business and IT leaders to put the technology to use.
“We’re still in the early stages of adoption in terms of regulatory compliance,” McCartney adds, “but RFID technology has the potential to unlock dramatic cost savings and efficiency gains.”