Aircraft are becoming lighter as composite materials replace metal in their components and airframes. Commercial aircraft component manufacturer ATK is employing a variety of new technologies to innovate the construction of aircraft parts and structures made with composite materials—which, compared with metal, improves an aircraft’s fuel efficiency and increases its payload capacity. In commercial aircraft, the percentage of carbon fiber used in 1980 was less than 5 percent; it is expected to become the dominant material by 2015.
To accommodate this expected growth, ATK implemented a radio frequency identification system provided by OATSystems to track perishable composite material and associated tooling. Frozen composite material is being tracked via RFID, thereby ensuring that it is moved efficiently through the component-fabrication process. RFID reader portals are also being used to track the location of tooling, which the company utilizes to form the aircraft components, prior to the items being cured at high temperatures and pressure.
The solution, ATK reports, will help it create what the company calls a “visual factory,” making it possible for employees to view work-in-progress based on RFID tag reads. With the RFID system, the firm can meet requirements from such customers as Airbus and Boeing, which will produce more than 8,000 fuel-efficient composite aircraft combined over the next six years. RFID automation will enable ATK to further ramp up production 12-fold to meet the aggressive delivery targets for Airbus’ A350 XWB. As of this month, ATK indicates, Airbus has received 616 pre-orders for the new aircraft, which is scheduled for first deliveries later this year. At peak production, ATK expects it will produce enough composite components each month for the A350 fuselage alone to stretch 25 miles in length.
Manufacturing composite parts requires a process of cutting, forming and curing advanced composite materials, rather than using metal components. To track this process at high volumes, ATK installed the RFID solution at its Aircraft Commercial Center of Excellence (ACCE), located in Clearfield, Utah. The facility is where ATK fabricates composite airframe and engine components for the A350 XWB, as well as composite engine components for Rolls-Royce and General Electric Aviation.
Prior to installing the technology at the ACCE in April 2012, ATK and OAT tested RFID technology on a smaller-scale project at an adjacent ATK manufacturing facility, where composite structures for F-22 and F-35 military aircraft are produced (see RFID Takes Wing at Composite Aircraft Components Plant). As part of that test, ATK applied EPC Gen 2 passive ultrahigh-frequency (UHF) RFID tags to composite materials used to fabricate curved structural components, and read those tags via fixed interrogators as they moved into and out of storage freezers. The company’s priority was to gain visibility into material location and remaining usable life. The materials are highly perishable, and must be transported, stored and monitored at subzero temperatures. Generally, if a piece of composite material spends more than 700 hours out of a freezer, the material degrades and must be discarded.
By using data related to the reading of tags on materials as they are moved into and out of freezers, the software tracks each unique item’s out time. During the pilot, OAT and ATK tested various locations at which to install the readers, as well as directional algorithms for antenna transmission, and the integration of read data with ATK’s shop-floor and enterprise resource planning (ERP) systems. As the pilot was carried out, ATK found that it needed to add additional readers and antennas at each freezer, in order to determine the directionality of the materials moving into and out of the cooling units.
The company had previously utilized bar codes to track the movement of composite material, so the RFID system was tested against bar codes. “The initial read results were in the 95 to 100 percent range,” says Jim Morgan, program manager for ATK’s aerospace structures project management office (PMO). After additional testing and system enhancements were carried out to increase read rates, ATK opted to install the system throughout the ACCE facility. The solution was taken live in April 2012.
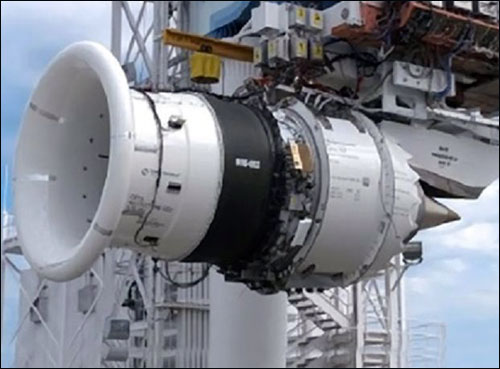
The ACCE’s system consists of Zebra Technologies RZ400 printer-encoders to print the RFID labels and encode their embedded Alien Technology Squiggle inlays. The labels are then applied to rolls of composite material via AS3 freezer-grade adhesive, as the rolls are received. Impinj Speedway R420 RFID readers at the dock doors read the newly tagged composite materials, thereby tracking when those items were received. The tags are again interrogated as the materials enter and leave the freezer, thus creating a date and time record for each event.
In addition, ATK is attaching Xerafy MicroX II tags to the tools on which its composite products are formed and cured within autoclave ovens at high temperatures and pressure. The system enables ATK to identify the number of times a tool has been used during the forming and curing processes, and to ensure that the tool is recalibrated once it has reached the specific number of uses authorized since its most recent recalibration.
Because each tool is unique to the part or component being fabricated, the reading of the item’s tag at the entrance to the ACCE’s various work cells (work stations) at which the tools are used provides the company with a record of when each specific type of component has been formed, bagged (placed in a plastic bag and compressed via a vacuum) and cured, and when it is then ready for the final manufacturing processes prior to shipping. Once the component is removed from its tool, the part’s bar-coded label serves as the unique identifier that is scanned through the remaining workstations. ATK is currently testing the feasibility of embedding a UHF RFID tag in the components, in order to eliminate the bar-code labels.
Altogether, the system installed at the ACCE consists of 115 Speedway R420 readers, 460 Impinj far-field reader antennas, 15 RZ400 printer-encoders and seven Motorola MC9090-Z handheld readers, to be used for exceptions, cycle counting or locating tools and materials.
RFID read data is received, interpreted and integrated with ATK’s existing management systems by OATSystems’ OATenterprise software. Part of that suite, OATxpress, manages RFID devices—including printers and readers—and also generates RFID labels for attachment to composite materials, for tracking those materials’ movements into and out of freezers. The OATxpress software pushes data to the shop floor and ERP systems, and then forwards real-time material-tracking data via messaging to OATSystems’ software at the ACCE.
“All objectives are related to measurable efficiencies,” Morgan states. “If we know where tools and materials are, we enhance our efficiency, and we don’t have operators looking for tools or materials.” In addition, he says, the system helps the company detect expired material before it can be used. “If material has expired, there is an indication on the visual monitor in the work cells.”
RFID has been a critical asset for the company, according to Brian Andrus, the IT director of ATK’s aerospace structures division. “Without the ability to automate the tracking of these innovative manufacturing processes,” he explains, “it would be difficult to deliver on commercial contracts, which have significant production-rate increases over the next couple years.”