Workers at the aggregate-recycling facilities in Edmonton, Alberta, are wearing RFID-enabled vests and helmets that make it possible for heavy-equipment operators to be alerted about the presence of other personnel before an accident can occur. The solution, installed on six vehicles late last month, enables drivers to know when they may be in danger of backing into someone. The technology was provided by Scan-Link.
The city of Edmonton’s aggregate-recycling facilities receive rubble material from construction sites, and create material used for road construction within the city. The facilities received 5,000 metric tons of material in 1978, when the program began, and have since processed 4.5 billion metric tons of asphalt and concrete, thereby saving the city $7 million to $9 million annually, by reducing its use of landfill and creating new material for road construction.
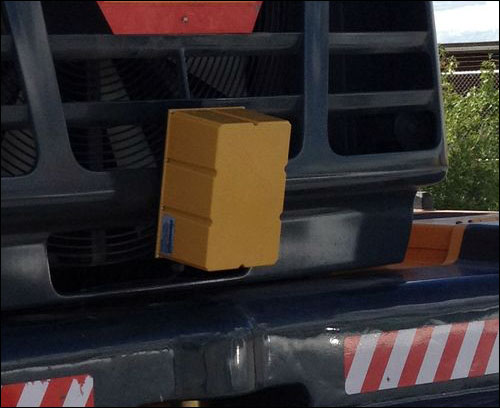
Edmonton operates two aggregate-recycling sites, says Blair Buchholtz, the program’s general supervisor, who adds that the work itself can be dangerous. A combination of contract loaders and city-owned loaders and skid-steers move around each facility, while 10 to 50 tractor-trailers deliver material on a daily basis. “The primary risk on our site is from traffic,” Buchholtz explains. Heavy equipment can provide a driver with limited visibility behind it while backing up. Therefore, the city has mounted a camera on the back of each vehicle, with a video monitor installed in its cab to afford the driver a rearward view. Operators do not always look at that screen, however, and might be glancing away at the moment that an individual steps into harm’s way.
Scan-Link’s RFID solution, known as Armour, consists of an integrated reader and antenna array installed at the back of the vehicle, as well as a display unit mounted in the cab. Workers are provided with RFID-enabled helmets or vests. If the reader detects an RFID tag within the vicinity, it transmits that information to the display unit, which then emits an audible sound and flashes a row of red lights.To ensure that the reader can always detect a worker’s presence, regardless of which direction that person may be facing, each vest and helmet is fitted with multiple RFID tags. Every vest comes with 14 ultrahigh-frequency (UHF) passive EPC Gen 2 RFID tags, according to Jonathan Fava, Scan-Link’s president, which are sewn into the vest at the point of manufacture—eight on the front, and six on the back. The helmet is encircled with 10 RFID tags affixed inside it.
When Scan-Link encodes each tag with a unique ID number, it programs the reader’s software to differentiate the tags on the front of a vest or helmet from those on the back. In that way, the system can determine whether or not the individual is facing the vehicle, based on which tags were interrogated.
When a vehicle operator shifts the engine into reverse, the reader enters active mode and begins seeking any tags within the vicinity. If the device comes within approximately 5 meters (16.4 feet) of an RFID tag on a worker’s helmet or vest, it recognizes the tag’s ID number and issues an alert message, via 2.4 GHz, to the Armour display unit located within the vehicle’s cab, which then sounds the alarm and flashes its lights. This warning continues until the tag leaves the read zone.
Currently, read incidents are not saved or tracked. However, the company reports, the Trans-Link software platform, being developed for release in September 2012, will provide greater functionality. With the new system, the data could be saved on the reader device, and a laptop could be connected to that unit to upload a history of read events at the end of each day. The solution could also transmit that information in real time, via a Wi-Fi connection.
The Scan-Link software, which would reside on Edmonton’s back-end system, would enable aggregate-recycling facility managers to not only track the number of events that occurred, and the direction in which the involved individuals were facing, but also identify those workers and vehicles. In this way, the managers would be able to study work-site behavior—and provide further training, if necessary.Scan-Link, which designed the reader circuit boards and software, manufactures the reader units at its Canadian facility using off-the-shelf RFID components. The company offers the solution to construction sites and oil fields.
The system cost Edmonton about $3,000 to $4,000 per tagged vehicle, Buchholtz says, and five vehicles on the city’s two aggregate-recycling sites are currently equipped with the reader units. The city also utilizes an additional mobile unit that can be attached to any vehicle on site, as necessary. Twelve employees presently wear the vests or helmets, while the sites have extra helmets and vests for use by visitors.
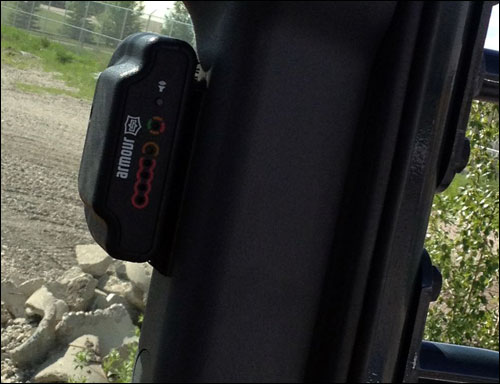
The system has been in operation for approximately three weeks, Buchholtz reports, and has detected no near-misses to date. “That’s good news,” he states. “We run a fairly safe site, so we haven’t had any incidents yet.” However, he notes, “the operators say it gives then the extra view they didn’t have before. It’s like an extra set of eyes.”
The city’s aggregate-recycling program is also considering using the technology on its conveyors, Buchholtz says, in order to detect when someone enters a restricted area—at which time the system could shut off the conveyor equipment, as well as sound an alarm. He adds that the city has other work sites, unrelated to the aggregate-recycling program, where it could opt to deploy the technology in the future.