Ameya Logistics has been employing an RFID-based freight-container tracking solution that it designed and co-developed, and has been sharing data collected by the system with its customers, in order to enable them to locate their containers stored at Ameya’s container freight station (CFS), at any time, via the Internet or on a mobile phone using SMS text messaging. The system—which tracks each container’s whereabouts via an ultrahigh-frequency (UHF) EPC Gen 2 passive RFID tag—benefits both Ameya Logistics and its customers, by helping the company know each container’s location within its yard, as well as which empty slots are available for newly arrived containers.
The most immediate benefit, according to Ameya Logistics, has been a reduction in the time required for workers to search for containers stored within the yard when they need to be inspected for clearance, or shipped out from the CFS. While finding a container among the approximately 5,000 on hand could take a long time in the past, with the RFID system it takes only a matter of minutes, the firm reports. Employees can now simply view the software, identify where a particular container was last placed, according to the RFID data, and then proceed to that location.
The solution—developed jointly by Ameya Logistics’ IT department, under the leadership of Amol Jumde, the company’s IT and business process manager, and technology solutions company C&B Electronics—was installed in October 2011. C&B Electronic also provided the hardware for the implementation.
This project was conceived and initiated by Percy Vapiwala, Ameya Logistics’ CEO, who says he wanted to reduce human intervention within the CFS’ high-risk operational areas, “and at the same time ease the tracking pain of our customer.” The deployment was also aimed at improving operational efficiencies. In addition, Vapiwala says, Ameya’s managing director, Ashish Goel, “wanted to provide value-added services to customers at no additional cost, and the entire team rose to the challenge and implemented the RFID technology.”
Ameya Logistics’ CFS, located at the Jawaharlal Nehru Port, near Mumbai, stores and delivers import, export and bonded containers and cargo to more than 200 different customers (the shippers). It has been in operation for about three years. Approximately 5,000 to 6,000 containers are located at the CFS at any given time, with each 20- or 40-foot container remaining on site for an average of 10 to 12 days. While at the yard, the containers imported to India must be inspected according to that country’s customs requirements—usually by customs agents, who complete the import customs requirements for the shipper. Upon arriving at the yard to conduct an inspection, an agent must be escorted to that specific container.
Containers occasionally must be shifted in order to allow the movements of other containers. As a result, most are moved between two and six times while at the yard. Each container’s location prior to the system’s deployment had to be manually recorded on paper, and then entered into Ameya Logistics’ management software on its back-end database.
Because of the storage yard’s complexity and high volume of containers, Ameya Logistics sought an automated system that would enable its staff, as well as shippers, consignees and customs inspectors, to know where a container is located within the yard at any particular time, based on its location the last time it was moved.
“The issue for Ameya,” Jumde explains, “is to effectively manage container yard space, reduce container shifting, and thereby reduce operational cost.”
Ameya Logistics built a ramp at its gate through which containers enter and exit the yard. Workers use that ramp to reach the top of each container, on which they then attach a Hawk RFID tag, manufactured by C&B Electronics. An RFID reader, custom-designed by C&B Electronics, is also installed at the gate, in order to read each container tag entering the yard. Staff members then input the container’s details into Ameya Logistics’ management software, and as each container is transported into the yard, the interrogator captures its tag’s unique ID number and transmits the information via a cabled connection to the software, where the ID is married to such shipment details as the container’s serial number and the customer’s name.
Once in the yard, the container is transported to an open space by one of Ameya Logistics’ nine mobile cranes, known as reach stackers. Each stacker is equipped with a C&B Electronics device that incorporates an RFID reader, a GPS unit and a GPRS radio. The reader’s antenna is installed to the underside of the boom that lifts the container, in order to capture the tag’s unique ID number, and the GPS unit ascertains that container’s longitude and latitude coordinates. All of this data is then sent via GPRS cellular transmission to the back-end Hawk software. The reader continues to interrogate the tag as the stacker moves the container, until that container is deposited within a specific area of the yard, at which time the reach stacker drives away and thus no longer reads the tag. The software then calculates the exact time at which the tag ceased to be read, and links that time with the location, within one meter, based on GPS coordinates, after which the tag is not read again until the container is moved once more with a reach stacker.
“This gives 100 percent coverage,” Jumde says, “since each and every movement is recorded in the system.”
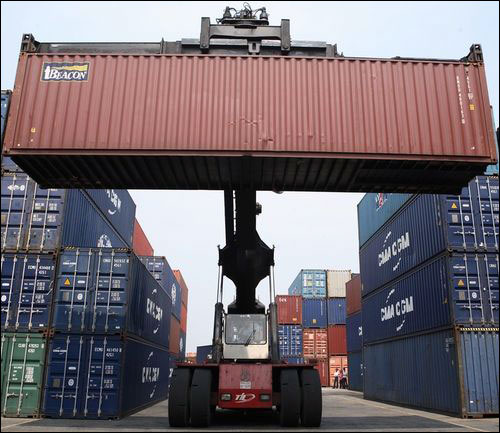
There are two different types of software that Ameya Logistics uses for managing all yard operations, Jumde says. “One is the core ERP [enterprise resource planning system], which was already operational,” he states. “The other is the Hawk software system specifically developed by C&B for this RFID-based container-tracking and yard-planning solution.” Once the tag ID has been read, he explains, the Hawk software “fetches all other required data for that container from the ERP.” The Hawk software not only provides real-time container-location data, but also enables data analytics about the movements of containers, as well as those of the reach stacker itself, which provides the company with information regarding the efficiency of the yard and its staff.
The Hawk system accomplishes two tasks, according to Nitin Sirohi, C&B Electronics’ technology director. “It provides real-time container-location interfaces on mobile, Web and SMS,” Sirohi says, “and second, it applies data analytics to provide meaningful real-time yard-operations-related information as various reports on a very attractive dashboard.”
When an agent or customer arrives at the yard, either for inspection or to retrieve a container, that person can utilize a mobile phone or a tablet PC to access Ameya Logistics’ server and enter a password to learn a particular container’s location, based on its serial number. The system can retrieve location data for up to 10 containers at a time. Each container’s serial number can also be sent to the server via an SMS message, enabling users to obtain information via a mobile phone.
When the container is shipped out, its RFID tag is removed at the gate and reassigned to another container. If not removed, the tag will be read by the interrogator as it passes through the gate, and an alarm will be sounded, indicating to the gate staff that a tag is leaving the yard.
Since the system went live, Jumde says, it has reduced the amount of time employees spend searching for containers within the yard—from several hours, in some cases, down to mere minutes. The software also allows Ameya Logistics to create reports, including a “machine-utilization report” that provides visibility into the work being performed by each reach stacker every day. What’s more, with the RFID data stored in the software, the yard-operations department can plan the placement or movement of containers based on cargo deliveries requested for a given day, as well as on existing locations of containers, and thereby provide more precise instructions to yard operators.
Customers do not pay for the RFID-based data, Jumde says, noting, “This is a value-added service to our customers.” That added value includes Internet-based information about containers’ locations, thereby decreasing the time inspectors spend seeking specific containers, as well as more efficient shipment of containers out of Ameya Logistics’ yard.
C&B Electronics has completed four similar implementations in India, Sirohi says, in partnership with other companies. During those earlier deployments, however, C&B’s role was limited to providing the necessary hardware components.