Brazilian company Beeight Group, located in Cianorte, Parana State, manages four brands certified by the Brazilian Textile Retail Association (ABVTEX), which includes carrying out an audit to certify production standards and guarantee the dignified working conditions of its employees. The brands are Six One, Yonders, Club Denim and Beeight. The group sells more than two million items per year, and it decided to invest in a radio frequency identification solution from iTAG Etiquetas Inteligentes to boost agility, control and reliability at its distribution center.
In addition to exclusive collections, the company develops apparel for major retail chains throughout the country. All of this production is generated at its own facility, which is divided into four units. The plant spans more than 10,500 square meters (113,000 square feet) and employs approximately 700 direct workers, making it one of the largest job generators in the region and the fifth in its host city.
Through the use of RFID technology, Beeight achieved agility in the process of parts entering and leaving its DC. According to Anderson Dias, an executive at the company, “A process that used to take 20 to 30 minutes can now be done in five seconds, and balances that used to take a day to do now, with the aid of the RFID reader, can be done in half an hour.”
Here’s how the iTAG system operates: The RFID tags are printed by the warehouse and sent to the finishing area, where the tags are affixed to clothing. After that, the parts are sent back to the finishing area, where they undergo the DC’s entry and dispatch process. “The process is carried out by reading RFID on a portal in that area,” Dias explains, “which already integrates parts into the ERP [enterprise resource planning] stock count.”
Based on this stock count, orders are generated, which are then prepared for invoicing. This is carried out with the help of two RFID portals, which read the labels and provide quantity information and verification to confirm that each order was consolidated correctly. “Then the parts are packed and sent to our customers,” Dias states. “The gains already achieved with RFID involve more agility at the entry and exit areas, which has met all of our expectations.”
iTAG’s Monitor middleware has as its main functions the control of portals and the integration of information from the ERP system used by Beeight Group. “Assistance with integrating the system, with specialized technical support and a supply of labels, was the main benefit offered by iTAG,” Dias says, adding that he had no problems with the integration of the iTAG system with the ERP, even though the database is located at a data center. He foresees continuing investments in the technology. “Now, we are working on an anti-theft system in our stores, using RFID.”
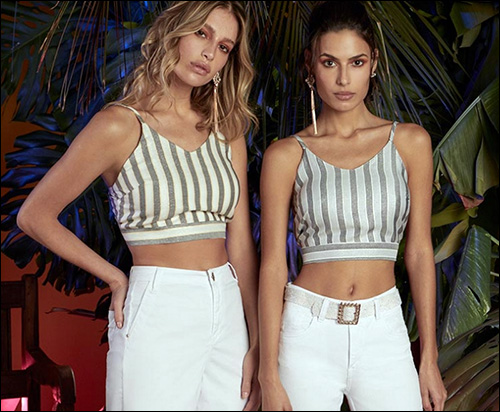
The company develops apparel for major retail chains throughout Brazil.
Before the RFID system was deployed, all goods had to be handpicked manually, Dias says, using barcodes. “With RFID,” he adds, “we can read up to 40 pieces per box in less than five seconds.” The RFID implementation follows GS1‘s passive EPC UHF RFID standard. “Today, we have three portals for reading products with tags, and the readings are made through iTAG Monitor, which integrates the reading of the portals with our system. There are four Zebra Technologies readers, and we use iTAG’s 74X20 adhesive labels, each with an Impinj chip, for the 80,000 pieces per month.”
At the beginning of the deployment, Dias recalls, the biggest challenge was the creation of new tags on which the RFID tags would be glued, since they could not be metallized or else they would cause reading interference. “Training our employees was one of the challenges,” he states. “However, as it is an interactive system informing the beginning and end of the readings, we did not have many problems.”