According to Statista, the number of Internet of Things (IoT)-connected devices in use is projected to total 75.44 billion worldwide by 2025, a fivefold increase in ten years. Within a rapidly growing subset of the Industrial Internet of Things (IIoT), asset intelligence, the simultaneous reduction in cost and increased performance of tracking devices—either Bluetooth- or GPS-based—is expected to see more and more businesses take advantage of the operational intelligence provided, to help them keep track of their key assets.
For blue-chip organizations with multi-site, global manufacturing operations, the reduced costs and increased capability of devices will be an enabler for transition from a pilot study or siloed implementation to full-scale adoption across their operations.
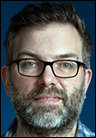
High-Value Asset Tracking to Mitigate Risk of Loss
In its simplest form, asset intelligence is a process by which sensors are placed on items to help companies pinpoint their locations. Supporting fast-moving industries in which the rapid, flexible redeployment of assets is demanded, this minute-by-minute data allows businesses to track high-value assets. As replacing an asset is an expensive decision, businesses can minimize the financial risk by using accurate location data, while also reducing the amount of downtime employees spend looking for missing equipment.
Using technology to track assets is an approach that existed before the advent of the IIoT. But while passive systems such as RFID and barcodes have historically been used to track individual assets, increasingly more manufacturing businesses are moving toward the adoption of advanced, active technologies within the IIoT domain, allowing them to have greater visibility over their entire suite of assets, both within their facilities and across the global supply chain.
Specific technological advancement of facility-tracking sensors includes the move toward LoRa and other lower-power consumption components—for example, helping businesses to eliminate the need for power infrastructures and increase the potential area in which they can track assets. While this intelligence is helping to reduce asset wait time, businesses can quantify this impact by trying to produce a “total-cost-of-waiting” metric. To do this, they should ask themselves such important questions as: Do I know where my assets are? How long have they been there? When was the last time they were used? What condition are they in?
Once a business has an exact figure for what waiting is costing, and thus how much money could be saved by working more efficiently, that company can then justify the upfront costs for implementation, as well as identify a set of shared assets that are critical to multiple processes and operations within the facility.
Predictive Maintenance and Environmental Monitoring
While facility tracking is helping to improve processes within single (usually indoor) locations, a large proportion of manufacturing businesses have assets that travel off-site and, in many cases, across borders. Using GPS technology, businesses can maintain the operational visibility of an entire set of assets, wherever they are throughout the world.
Alongside the benefits of global tracking from a logistics and supply chain perspective, one emerging use case of GPS tracking is to predict and prevent the breakdown of industrial engines, known as predictive maintenance. Pathfindr recently launched a major program with MTU Rolls Royce by which GPS trackers, as well as bespoke software which interprets and displays the resulting data, enable the performance of engines to be monitored wherever they are located. But the wider possibilities are vast, and the same capability could also enable transport providers to save time and money by identifying technical issues before they can arise or become more serious.
The integration of IoT technology can seem like a daunting prospect for businesses. However, with continued innovation helping to drive down the cost of IoT technologies, many organizations are starting to recognize the benefits successful implementation can have. Alongside some of the IoT’s wider-used capabilities, such as location tracking, firms are increasingly assessing how they can benefit from more sophisticated intelligence through data, including temperature, humidity and air pressure. We expect the adoption of IIoT devices to continue at pace, driven by a desire to gain operational intelligence that enables organizations to boost efficiency and remain highly competitive.
Steve Crowe is an electronics design engineer at Pathfindr. The company’s award-winning Industrial IoT solutions provide customers with real-time insights into their assets and processes. From indoor and outdoor tracking to environmental monitoring, Pathfindr’s consultative approach has transformed businesses around the world. Pathfindr works collaboratively to continuously improve its software and, with zero infrastructure required for its hardware installation, it is accessible to all.