Several Russian companies are employing an RFID-based conveyor system to provide users with quick access to garments in cloakrooms or uniform storage. When a person checks a coat or other garment, he or she receives an RFID-tagged badge or bracelet encoded with a unique ID number linked to that item’s location. The company that provided the technology—Fresh—now has a U.S.-based division, Fresh USA, that is selling the solution in North America. The system includes the conveyor system for storing and retrieving the garments, as well as RFID readers, tags and software to identify which coat or garment is associated with each claim.
Resort and casino Tigre de Cristal and Izmailovo Concert Hall, both in Russia, are utilizing the technology to manage garments at their facilities.
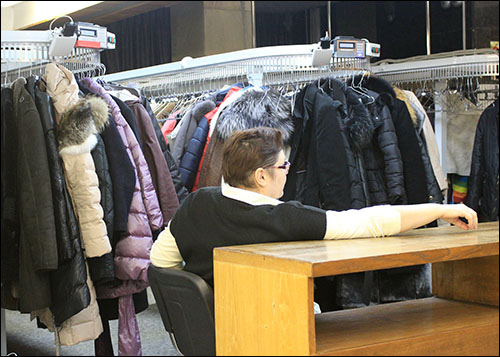
Tigre de Cristal has deployed Fresh’s RFID-based solution to manage its coat-check service, as well as its uniforms. The resort and casino opened in mid-2015, and the system was taken live at the time of that opening. Tigre de Cristal has deployed one Fresh conveyor system for managing as many as 6,000 of its guests’ coats, and another to manage uniforms for up to 1,000 employees.
At the cloakroom, guests leave a coat with a worker at the casino employee. Each guest is then handed a plastic card containing an NXP Semiconductors high-frequency (HF) 13.56 MHz Mifare DESFire EV1 4K RFID chip, according to Leri Tomin, Fresh USA’s CEO. Staff members tap the card near the reader—manufactured by a third-party supplier in China—which is built into the conveyor’s controller box. The reader captures the card’s unique ID number and forwards that information to software that links the ID to the empty hanger space located nearest to the employee at the drop-off counter. Upon returning for his or her coat, the individual hands the plastic card to the worker, who then reads the tag, and the conveyor automatically transports the coat in that hanger spot to the front, where the clerk can access it.
The system for managing and laundering uniforms is fully automated. All uniform items, like shirts and trousers, have a washable ultrahigh-frequency (UHF) RFID tag, Fujitsu‘s WT-A521, built into them. In the Fresh software, the tag’s unique ID number is associated with the employee who uses that garment. At the end of that person’s shift, the worker turns in her uniform to be laundered, placing her RFID-enabled ID badge in front an RFID reader to unlock a compartment in the conveyor.
The reader captures the ID encoded to the card’s passive HF 13.56 MHz RFID tag (compliant with the ISO 15693 standard), which is linked to her name in the Fresh software. The system forwards her ID number to the software, which confirms that she had access to the cleaning system and thus unlocks the door. She places her garments inside and closes the door, and the software then links that compartment with the employee’s ID.
A UHF RFID reader installed at the conveyor, made specifically for the application by a third-party manufacturer, captures each garment’s tag ID number. The software then updates those items’ status as having been received for washing.
Once the clothes have been laundered, dried and folded, they are returned to the conveyor, where the UHF RFID reader again interrogates the tag IDs. The reader instructs the controller to move the compartment associated with those garments to the location where the uniforms are being reloaded. A staff member then places the garments within that compartment.
When the employee returns for her uniform, she again places her ID badge against the HF reader. The controller sends the compartment associated with that individual to the door, where she can retrieve her clean uniform.
Mikhail Tureyskiy, Tigre de Cristal’s casino facility manager, says that the system was installed to coincide with the new casino’s opening. “We wanted to have all the new technologies,” he explains. “The speed of customer service—this is important.”
The Izmailovo Concert Hall is also using the technology, which it installed early last year, to manage its attendees’ coats. The technology replaces its previous manual method for storing and accessing costumes. “Earlier, we had the usual large wardrobe [storage room] with simple hanging clothes and coat hooks,” says Igor Mikhailovich, the concert hall’s deputy director. “In earlier times, we had a large queue in the wardrobe before the concert and at the end.”
The software not only helps Izmailovo’s staff identify coats and other garments quickly, and to correctly match them to their owners, but also creates a record so that the company knows how active the cloakroom was.
According to Tomin, the system triples the efficiency of a typical cloakroom or uniform storage area that might have otherwise utilized a manual tracking method. The company opened its U.S.-based office this year, he adds, and is currently in discussions with several potential users. The system is customizable for each end user, Tomin notes, and is RFID hardware-agnostic.