Most distribution centers these days are required to ship items bearing RFID inlays to customers, but few are reaping the benefits that can be achieved from utilizing radio frequency identification in their warehouse-management system (WMS) software. With the increase of demand for RFID, most DCs have some sort of method in place for reprinting or encoding a replacement label when necessary. Some are also performing quality checks of RFID tags (inlays integrated with the UPC label) that are attached to products.
The University of Auburn’s RFID Lab has published several white papers illustrating the value of using RFID to maintain the correct inventory levels of products at a distribution center. Some of the first areas that come to mind with regard to deploying RFID are receiving and shipping.
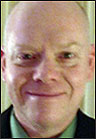
If a distribution center uses an automated conveyor to receive product shipments, then an RFID tunnel on this conveyor would allow the DC to identify any shortages (cartons that are not packed to meet the item’s requirements). At other DCs, a portable conveyor is rolled to the dock door to unload the truck. In this instance, an RFID panel could be installed at each door, but doing so can be very expensive and create problems involving misreads. A better alternative would be to have a mobile wireless RFID tunnel that can be temporarily placed in front of the door where the vehicle is being unloaded.
The area in which the biggest inventory errors can occur is the pick-and-pack area. This is where an employee can scan one item, then tell the system he is placing multiples of that item in a carton to be shipped. A worker might also place the wrong item in a carton, and the system would think the correct item was packed.
Of course, cycle counts can help reduce the incidence of such errors, but your cycle-count procedure may be flawed. RFID can make this a lot better. For example, an RFID reader could be mounted above each employee’s workstation, where he or she packs items in cartons placed on wheeled carts. If the wrong item is placed into a carton, then a screen can signal that problem. If the item is correct, the system can update the quantity in the box and adjust the inventory count in real time. Next, if the DC has a conveyor system to move cartons to the shipping area, an RFID tunnel on the conveyor can audit every carton that is packed. This would allow you to ensure that the tags are encoded properly, as well as check for duplicate serialization and test each RFID inlay’s quality.
This is a great benefit for tags that are printed and encoded on an RFID printer, where the inlay is encoded and tested when it is very close to the reader. Although most printers perform verification upon reading an RFID inlay, a weak inlay can pass the testing process at such a short read distance. An inlay can also become damaged while being attached to an item, which is why this additional quality check can prove quite valuable. When a tagged item being loaded into a carton is identified as a non-read, encoded wrong, a duplicate serialization or the wrong item (this is determined by checking what the WMS software expects to be in the carton versus what is really in it), that box can be diverted to an area where the problem can be corrected before it arrives at your customer’s door.
For the cartons that are shipped directly from a reserve area or are cross-docked, installing an RFID tunnel through which all pallets must pass allows the same checks as the inline RFID tunnel on a conveyor. The same type of mobile wireless tunnel used during the receiving process can be utilized in the shipping area.
Many who live and breathe the day-to-day operations of a distribution center will quickly notice that I did not mention performing RFID reads within the reserve area. This is because if all cases of goods are checked as they enter the DC, the normal cycle count within the WMS software is more than adequate. Using an RFID label attached to each case would allow faster and more frequent cycle counts of that area.
Doug Harvel is an RFID consultant with more than 20 years’ experience in a manufacturing and distribution environment using Manhattan Associates‘ WMS software, and more than 12 years of working with RFID. If you have any questions or would like to discuss this article, please feel free to contact him at [email protected].