Why would any company want to track its employees? How does it work? Why do it?
What about Big Brother? What are the limits? Who should be tracked? Would the union support it? Is it a covert management strategy?
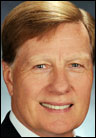
A lot of concerns and questions abound when talking about monitoring personnel in the workplace. However, there are many situations for which it is not only important to have a tracking system, but also in the best interests of both workers and the company.
Let’s answer some common questions about employee tracking.
When do you track workers?
If workplace operations involve any possibly dangerous tasks or materials that can potentially harm employees, it makes sense to provide for staff members’ safety, for the sake of the company, the workers and their families. If an “event” occurs, safety officers need to be able to immediately identify who is safe and who is not, and to provide directions to guide everyone to safe havens and muster stations.
Clearly, this is true for many operations in the oil, gas, tunneling and mining industries. This seems obvious—and yet, many facilities currently do not have an effective system in place to track personnel in the case of emergencies. Worse, it is true that many still use pencil, paper and a clipboard or a magnetic board to figure out who is onsite. Such manual systems are inaccurate, untimely and unreliable—especially during the “fog” of an emergency.
One region has mandated the use of RFID tags to track workers on offshore oil rigs in the North Sea. After a major accident at sea, the Scandinavian countries got together to pass regulations to protect employees. Knowing who is where during an emergency is something that should not be compromised when lives are at stake. Consequently, the North Sea oil industry is now among the world’s safest.
We have examples of tragic events occurring in the Gulf of Mexico, for which crucial minutes, hours and even days passed during which the companies had no idea who was affected, who was safe or even who was impacted.
What works for offshore oil workers is equally important for land-based facilities, including all types of chemical and process industries. If your facility runs periodic evacuation drills, then you can benefit from implementing a proper mustering and tracking system, since it would reduce the time and cost involved in conducting drills, quickly expose process weaknesses and, most important, ensure that you never have to call workers’ wives, husbands and children to inform them of a tragic accident at your worksite.
There are also security reasons for tracking workers, to ensure safety and security for all. Zones can be established to be sure that only authorized, qualified personnel are granted entry. Drivers and their vehicles can be monitored to provide visibility of all such traffic on company premises.
Overall, security is a growing concern that businesses need to consider, given the growing potential for theft and other criminal or even terroristic purposes.
What technologies can be used?
Traditionally, photo ID, magnetic stripe and passive proximity RFID cards (with a read range of a few inches) are used to identify and allow workers to pass through checkpoints, gates, doors and so forth. More recently, passive RFID cards are being used much like a highway toll tag to identify a worker within 5 to 10 feet or so of a reader at selected choke points, such as a turnstile.
None of them are effective in tracking workers at longer ranges, however, or during actual emergency situations.
If there is a problem and evacuation alarms go off, the last thing employees will do is stop to swipe or wave their ID cards, or walk in an orderly single file out the door. Forget about magnetic boards and clipboards.
During emergencies, everyone flees to safety through any exit they can find—dock doors or even bathroom windows—some grabbing whatever is close to them. Short-range passive RFID badge systems are simply unsuccessful at tracking personnel during the chaos of an evacuation emergency.
Field experience has proven that long-range active RFID is the only technology that can deliver the use case demanded for personnel evacuation and mustering systems.
What works? The case for active UHF RFID
Active UHF RFID tags have proven to be not only effective under harsh conditions and extreme weather, but also versatile enough in situations involving large, noisy metal structures with machinery, or in environments that may contain gases and vapors, high voltages and thick airborne dust.
Two versions can be supplied—one for routine operations in nonharzardous environments, and one that has earned “Intrinsically Safe” or ATEX certifications for continuous operation in the presence of flammable gas or explosive airborne particles. My company, Identec Solutions Inc., provides both types of tags in a product line optimized to track thousands of workers in many industries worldwide, in office-like conditions or outside in extreme temperatures ranging from -40 degrees to +85 degrees Celsius (-40 degrees to +185 degrees Fahrenheit).
While the tag’s physical characteristics are one consideration (form factor, ruggedness, shape and size), most important is that the tags can be detected at a long range—up to 1,500 feet (500 meters) away—while being carried by hundreds of workers, even those who are packed tightly together, running or carrying equipment. Employees carry their ID tags in many different positions: hanging or clipped outside on their clothing, stored in their purses or briefcases, cupped in their hand, tucked inside coat pockets and so on. Any system used for monitoring personnel safety must thus accommodate all of this uncertainty without interfering with the ability to read every tag, especially at times when people’s lives are at risk. This is a technical challenge that active ultrahigh-frequency (UHF) RFID tags have proven capable of meeting.
What is gained by tracking workers?
When employees wear active UHF RFID tags, their locations and identification can be monitored during emergencies or drills, in order to ensure that proper directions and guidance are given to safety officers, first-responders and management. Such visibility is immediate and automated, enabling a company to efficiently gain a handle on the situation and thus make intelligent decisions with urgency.
Even routine drills can be expensive, considering the downtime during the drill itself. It has been shown that automating the process for accountability can cut the amount of time required to conduct and report on drills by two thirds or more. This affects overall facility productivity. Reports on drills or events can be automatically generated to comply with regulations or other policies, and the system can automatically create a traceable record.
What’s more, if the active tags are part of an overall solution, such as Identec’s Watcher Suite, other actions can immediately be taken to address the nature of the emergency. This solution can be designed to automatically trigger the opening and closing of doors, turn on signage to offer directions to safe areas, and transmit alerts and alarms. In addition, it can incorporate the use of video to observe the affected areas, and present all the information on a map of the facility, thereby enabling quick, effective decision-making and guidance for first-responders and other personnel.
What about Big Brother?
A worker-location system does not necessarily track an employee’s every movement, nor does it need to record the worker’s trail. Typically, when there is a special reason to provide visibility of personnel within a facility, active RFID readers can be installed by zone.
Without a reader, there is no tracking. Many applications have no need to monitor workers in-building.
Once “emergency mode” is activated, a reader installed outside the building identifies workers as they leave the facility or approach a muster station. Such stations can communicate with each other wirelessly to ensure full visibility for all personnel, regardless of which muster station they use. However, once a staff member leaves the worksite and moves beyond the reader’s 1,500-foot read range, he or she can no longer be tracked. A smartphone-based system, by way of contrast, is capable of monitoring workers 24-7, anywhere on the planet.
Readers can be installed at a plant’s entry and exit points to capture every worker’s arrival on the grounds, even if an individual arrives or leaves by car. Company vehicles can also be tagged, in order to monitor their authorized usage. While the battery-powered tags worn by employees inside vehicles can be interrogated as they enter and leave, they can no longer be read once the vehicles travel outside the system’s read range of 1,500 feet.
Safety officers can rely on fixed readers installed at strategic locations to automatically capture data as necessary. As such, workers need not be tracked all the time while on premises. Systems can be turned off during normal operations, and be automatically activated during an event. With such RFID deployments, Big Brother becomes a non-issue.
Leaders or safety officers can also utilize a variety of mobile devices—tablets or smartphones—in conjunction with RFID readers. For example, Identec will soon be launching a new handheld reader (about the size of an iPhone 5) that can read Identec active UHF tags located up to 300 meters (980 feet) away and forward the data to a tablet or other handheld device via Bluetooth. Such a setup could be carried to a muster station, where it can easily read the tags of every worker gathering at that station.
What about the cost of such a solution?
Of course, every facility is different. Requirements are variable, and specific objectives can be paramount. The installation of a plant- or enterprise-wide solution involves much more than ID cards, tags and readers. It also requires architecture (including design, installation, integration and support for both hardware and software) that can deliver real-time visibility during practice and emergency evacuation drills. Such an advanced solution might cost up to $500 per worker, but the systems are proven, easily deployed and reliable, and the cost is normally recovered completely after two or three evacuation drills, due to the time saved during the drill while having an automated, audited system.
Other benefits of a worker-location system include lower insurance premiums, auditable compliance, and the simple confidence and peace of mind that comes from knowing there is an effective system in place to safeguard employees. This is attractive for existing staff members, as well as for the recruitment of new personnel.
Finally, for senior management, a company’s reputation is often at stake, and their commitment to worker safety using active RFID should clearly be more than a simple written statement, policy or poster. What’s more, the increased visibility provided by the technology might result in saving a worker from being injured or killed onsite. How much is it that worth?
John Shoemaker has spent the past 25 years in the AIDC industry and functioned at the C-level for several technology companies with wireless and sensor solutions serving many industries worldwide. Currently, he is the executive VP of Identec Solutions Inc., a supplier of active UHF RFID technology designed to increase people safety, productivity and efficiency in harsh environments.