RFID projects are uniquely challenging for most companies, because they require close collaboration between personnel in two very different departments: Operations—in factories, warehouses, stores or other environments—and IT. For an RFID deployment to succeed, operations and IT must take joint ownership of the project, and that may be an unfamiliar style of collaboration for both of them. The best approach is to get these teams working together at the beginning of a project, with a focus on a common deliverable: a detailed specification of the data that will flow between the tag and reader infrastructure and the IT systems.
Creation of a data specification is a two-phased process. In the first phase, all the operational processes that will involve RFID must be mapped out step by step. Tracking finished products, for example, includes shipping, receiving, warehousing and in-store operations. The processes for monitoring equipment, tools and other assets might include procurement, inventory, inspection, maintenance and repair.
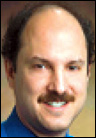
At this stage, it’s mostly the operations staff talking and the IT folks listening. Operations should describe all the relevant processes in which tagged objects are handled. But IT should ask probing questions, such as: Does it always happen that way? What can go wrong? What happens if that step fails? This ensures both the “happy path,” when things work as expected, and exceptions are covered. This stage can be tedious, but it’s necessary for the context of the RFID data to be fully understood. It can also be illuminating for both sides—a good outcome is, “I didn’t know that’s how we really do shipping and receiving.”
At the end of this stage, the team should have many detailed flowcharts showing all the relevant process steps, including exceptions. Now the team moves to the second phase. Here, the IT people do most of the talking. Their first task is to identify which of the many process steps must be visible to IT systems to achieve the overall business objectives. Then, they need to determine exactly what data will flow from the RFID readers and middleware in each step to provide that visibility.
For each step, IT people must identify the “what,” “when,” “where” and “why” facets of data the IT system needs. The GS1 Electronic Product Code Information Services (EPCIS) standard provides an excellent framework for designing the data in this phase. IT must work with operations to ensure the data design is implementable, given the capabilities of the RFID infrastructure.
When finished, the operations team and the IT team will have a concrete blueprint from which to work as they proceed to the detailed design and implementation of their respective parts of the system. More important, they will be working together with a shared understanding of what happens on the other side.
Ken Traub is the founder of Ken Traub Consulting, a Mass.-based firm providing services to companies that rely on advanced software technology to run their businesses. Send your software questions to [email protected].