Drug counterfeiting is a global problem that costs pharmaceutical companies billions of dollars and threatens the health of millions of consumers. The National Association of Boards of Pharmacy reports that an estimated 1 percent to 2 percent of drugs in North America are fraudulent. The World Health Organization (WHO) cites similar statistics for European and other industrialized countries, but says the percentage of counterfeit drugs is much higher in many African countries and in parts of Asia and Latin America.
Countries worldwide have been working to stem the flow of counterfeit drugs in their supply chains. For many years, the pharmaceutical industry has been considering radio frequency identification technology to combat drug diversion and counterfeiting, as well as to improve manufacturing and distribution efficiencies. Indeed, pharmaceutical providers in South Korea and several other countries have piloted or deployed RFID solutions (see RFID Makes Order Out of Chaotic Distribution Chain, Gador to Track Drugs in Argentina and Nigerian Drug Agency Opts for RFID Anticounterfeiting Technology).
RFID had significant traction in the U.S. pharmaceutical industry, which leads the world in prescription drug manufacturing, accounting for 39 percent of production. “Companies did think, back in 2005-2006, that we were headed toward everyone using RFID,” says Dirk Rodgers, an independent consultant focusing on health-care supply chains. In 2005, for example, Pfizer began RFID- tagging each bottle of Viagra sold in the United States. In 2006, drug manufacturer and distributor Cardinal Health completed a successful RFID pilot, which included pallet-, case- and item-level tracking of pharmaceuticals, and noted that it planned to start integrating RFID with its operational processes. And in 2007, Purdue Pharma began rolling out a full-scale RFID implementation, tagging every bottle and case of OxyContin it produced.
So when the California State Board of Pharmacy issued an electronic-pedigree law, with an initial 2007 deadline, drug manufacturers and wholesalers began considering using RFID to meet the mandate, and RFID providers began offering e-pedigree solutions. The law stated that bar codes or RFID could be used to create an electronic record for tracking the movement of prescription drugs through the supply chain.
Florida, Nevada and several other states also passed e-pedigree laws, each with different requirements. Then, in 2008, the U.S. Food and Drug Administration stepped in, and the push for a drug-authenticating e-pedigree system moved from the state to the federal level.
In September, the U.S. House of Representatives passed the Drug Quality and Security Act (H.R. 3204), and in November, the bill passed in the Senate. The legislation creates a uniform national standard for drug supply-chain security that would supersede all state e-pedigree initiatives. H.R. 3204 has many provisions directed at the drug distribution supply chain. These include encoding most prescription drug products at the smallest salable unit and sealed homogenous case level with a unique product identifier. Serialization provisions designed to identify products are combined with product tracing and verification requirements.
The federal regulations, which have the same aim as California’s electronic-pedigree mandate, do not use the term e-pedigree. And H.R. 3204 makes no mention of RFID. In fact, the law prescribes the use of Data Matrix (2-D) bar codes on packages, and Data Matrix or linear bar codes on cases, to contain serialization information—the standardized numerical identifiers (SNIs), lot numbers and expiration dates.
What Happened to RFID?
RFID’s momentum began to wane as California moved its e-pedigree deadline from 2007 to 2009, then to 2011 and then to the middle of the decade. While the pharmaceutical industry continued to explore how best to combat counterfeiting, as well as how to facilitate recalls, companies increasingly chose to use bar codes rather than RFID in their learning projects, says Shabbir Dahod, president and CEO of TraceLink, which provides global track-and-trace compliance and improved supply network performance for life sciences. There was a perception that RFID was still maturing and the per-unit price was high, he says. At the time, for example, there were concerns about whether ultrahigh-frequency technology worked with liquids or foil, materials that can be found in drugs or drug packaging.
Cost was and remains an issue. Small drug companies handle tens or hundreds of millions of units annually, and large ones can handle billions of units, Dahod says. The cost of RFID tags, and of implementing an RFID infrastructure throughout the supply network, is too high for this kind of volume, he says.
Data Matrix bar-code printing can be easily integrated into the labeling process. “Data Matrix bar codes are a low-cost, effective way to establish and capture unique information at the item level,” says Gary Lerner, founder and managing director of BrandSure, a supply-chain services and solutions provider that has managed more than 30 serialization projects, many of them facilitating California e-pedigree compliance.
The ongoing costs of maintaining a bar-code system, even if its initial design and deployment expenses can be high, also are much lower than the continual cost of RFID tags, Rodgers says. “The ongoing costs are higher for RFID because you have to buy those consumable tags,” he says. “People in the RFID industry see it costs $1,000 for a bottle of drugs, so how much more for an RFID tag compared to the benefits you get. But people in [pharmaceuticals] look at it by what is the cost of packaging today, and what it is tomorrow, and the consumables cost goes there.”
In addition, pharmaceutical manufacturers question the value of RFID-enabling their supply chains, says TraceLink’s VP of marketing Brian Daleiden. “Much of the primary initial value for the use of RFID tagging comes in downstream receiving, shipping and inventory-management processes,” he says. “So companies are always asking, ‘How much will I have to pay for RFID enablement vs. how much ROI will my company gain from the investment?’ This equation is different throughout the supply chain and is something that will have to be worked out before broad RFID adoption takes place.”
There’s also the issue of education—or, rather, lack of education—among people at the federal level, says Michael Liard, VP of auto-ID at VDC Research, reflecting on why RFID wasn’t included as a way to create electronic records. “It’s unfortunate and disappointing,” he says. “People don’t understand the technology still… and how performance has improved miles and miles even from a decade ago, when we first talked about passive UHF and open-loop supply chains. You need lobbying power to force the hand of government to look at RFID, understand its physical limits and the value adds and benefits it can bring to different applications and use cases.”
A Global Approach
Data Matrix bar codes are the lowest common denominator that everyone in the industry can conform to for track and trace, Dahod says. “Now, it has gotten to the point that there is enough experience that the entire industry well understands bar codes, particularly 2-D Data Matrix bar codes, for the business processes built around them,” he says, adding that a foundational infrastructure exists around them both broadly and globally. In work with major pharmaceutical companies such as Pfizer (TraceLink serves as its core global track-and-trace provider), all that Dahod sees reflects bar-code serialization at the item and case levels. “Companies that were doing RFID have gone back and removed it, and moved to bar codes for track-and-trace compliance,” he says.
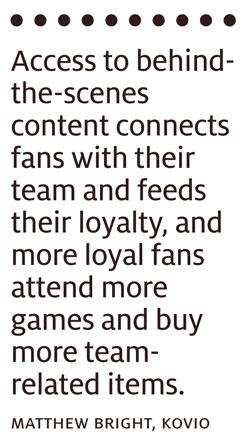
At the same time, dozens of other countries are drafting pharmaceutical serialization or e-pedigree regulations that spell out the use of Data Matrix bar codes. “These growing global requirements have caused companies to shift away from a country-by-country local solution approach,” Daleiden says. “They are now thinking about how to build a global IT, packaging and distribution infrastructure that can efficiently serve multiple countries and diverse supply networks.”
European Union members and India are among the countries that require or are about to require unique serial numbers on pharmaceuticals, says Ken Traub, principal at Ken Traub Consulting. They haven’t taken the additional e-pedigree step of requiring tracking every change of ownership through the supply chain, from manufacturer on out, he says. But Argentina, China and Turkey are moving ahead with full e-pedigree requirements, including serialization and change-of-ownership reporting to their respective health ministries. “If you are the manufacturer, the biggest part of the e-pedigree job is serialization,” he says. “So for manufacturers, they are looking at what to do to meet e-pedigree here and the laws of other countries, and it is pretty much the same problem.”
South Korea is unique in that it gives drug manufacturers the option of using RFID or bar codes for serialization purposes. That’s because the government has been funding track-and-trace pilots and required that a certain percentage of drugs be RFID-tagged as part of these efforts. “The biggest impetus in South Korea is that you had a really close private/public partnership in 2006 to 2009,” Daleiden says, “and the government’s sponsorship of R&D on RFID has kept that moving.”
Technology Standards
Pharmaceutical manufacturers or repackagers typically pack items into cases and seal them, and those cases may not be opened until they reach the pharmacy or the last distributor before the pharmacy, says Mark Harrison, director of Auto-ID Labs Cambridge, who works on technical standards development with GS1, which is trying to develop a global open standard for event-based traceability. “In between, there is reliance on visual inspection of tamper-evident security seals and trust that the items that were recorded as being packed in the case are still all present and correct,” he says.
“The industry calls this approach ‘inference,’ because they scan the case or pallet and infer the detailed information about which items are contained within it, instead of breaking open each case at each change of custody and scanning every individual item,” he continues. “So long as inference is considered suitably robust for use by the intermediate parties in the supply chain, there is no need for them to adopt RFID at item level.” RFID offers a significant advantage over Data Matrix bar codes only if there is a need at various stages in the supply chain to scan the items at high speed without opening each case.
GS1 EPCglobal‘s Electronic Product Code Information Services (EPCIS), which enables trading partners to securely exchange information regarding the location of products in the supply chain, has a role to play in pharmacy e-pedigree initiatives. “EPCIS was originally developed in the context of RFID,” says Traub, who was the editor of the EPCIS standard. “Because it operates at a business level, however, it doesn’t really take a position on whether the data comes from RFID, bar codes, manual data entry or any other source,” he says. “Pharma is moving strongly to the EPCIS data-sharing standard.”
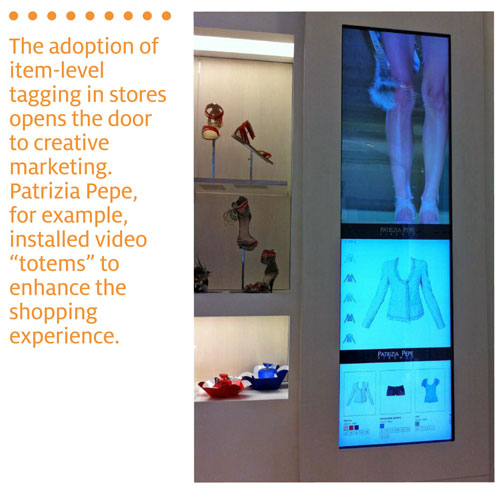
Rodgers noted recently in his RxTrace blog, “Over the last five years, the larger companies in the U.S. pharmaceutical supply chain have increasingly aligned around the EPCIS standard for holding and communicating serialization-based events.” While the federal government is not likely to mandate the use of EPCIS, the investments companies have made in EPCIS repositories are safe, he says.
GS1 is working on EPCIS v1.1, which will introduce additional capabilities intended to be applicable to many industry sectors—pharmaceuticals and food, for example—seeking to detect and eliminate counterfeits from legitimate supply chains. These include transformation events for relating input objects (such as specific batches, lots of ingredients or individually identified ingredients) to output objects (products composed of those ingredients). “EPCIS event data is the foundation for e-pedigree, because you can record every observation at every stage for a time-stamped piece of data of what was seen where, when and its business context (shipped, received and so on),” Harrison says. “EPCIS provides a standardized data model for that, and version 1.1 will additionally provide a number of enhancements, including a way for expressing events relating to the transformation of input objects into output objects.”
Checking Services, another GS1 standard under development, is designed to make it cost-efficient for retail pharmacies and distributors to verify serialized data on 2-D bar codes or RFID tags (see Checking Services). “We’re considering its role within the overall security framework,” Harrison says. “We expect to begin standardization of Checking Services and its interfaces, data model, etc., in 2014.”
Down the Road
The pharmaceutical industry has been focused on supply-chain visibility to meet track-and-trace compliance, Liard says. But he believes there is potential for drug manufacturers to use RFID technology within their own operations. “It’s going to take a little education and awareness building in the pharmaceutical manufacturing community to understand how RFID can have meaningful impact on operations today,” he says. There is an opportunity, he adds, for drug manufacturers to use RFID to improve their bottom line and help with efficiencies, whether that’s inventory visibility, asset management or other business-process improvements.
Someday, radio frequency identification technology may get another shot at the e-pedigree target, Dahod says. “I think RFID still sets the standard for the vision of where the pharmaceutical industry wants to be,” he says. “I believe the vision of the optimizations that can be made in inventory management, overall opeational efficiencies and improved safety. It’s there, but maybe it’s another 10 years out. Our hope and expectation is that RFID matures and becomes more pervasive. Initial learnings from specialty-type scenarios, such as cold-chain management, controlled-substance tracking and medication management, will be very helpful in providing the foundation for RFID to become the next lowest common denominator.”
RFID Apps That Are Working for Pharma
While RFID is on hold when it comes to pharmaceutical electronic-pedigree efforts, hospitals are beginning to embrace the technology to manage drug inventories and medication administration. The pharmacy department at the University of Maryland Medical Center, for example, is employing an RFID-based solution to manage medication kits used with patients in emergencies (see Hospital Pharmacy Keeps Emergency Medication Kits in Check). CaroMont Regional Medical Center deployed an RFID solution to track recalled medicines (see North Carolina Hospital Identifies Recalled Drugs via RFID). And Brigham and Women’s Hospital, which has used bar codes to manage its medication administration data since 2005, is evaluating a Near-Field Communication system to track the administration of patient medication (see Brigham and Women’s Hospital Tests NFC RFID for Patient Bedsides).
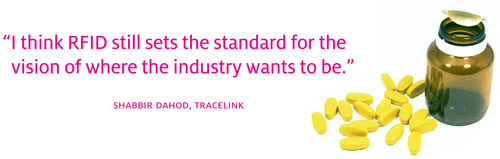
Some hospitals and logistics companies are also turning to RFID to track the temperatures of medicines. Memorial Healthcare hospital, for example, installed a real-time location system employing Wi-Fi active RFID tags with temperature sensors to monitor medicines in its pharmacy’s coolers. If a temperature is either too warm or too cold, the software sends a text message or e-mail alert to staff members responsible for the units. The system also provides a temperature record that can be provided to The Joint Commission to fulfill reporting requirements (see Michigan’s Memorial Healthcare Adopts Ekahau Wi-Fi Tags).
DHL Global Forwarding, the air and ocean freight specialist within Deutsche Post DHL, has commercialized DHL Thermonet, an RFID-based air-freight service allowing customers to track the temperatures of pharmaceuticals or biomedical items throughout the shipping process with an EPC Gen 2 passive ultrahigh-frequency RFID inlay integrated with a battery-powered temperature logger (see DHL Thermonet Tracks Drugs and Life-Sciences Goods With RFID Temperature Tag). Panalpina Group deployed an RFID solution to track the conditions of health-care and pharmaceutical products during transit or storage (see Global Logistics Company Monitors Shipments’ Temperatures).
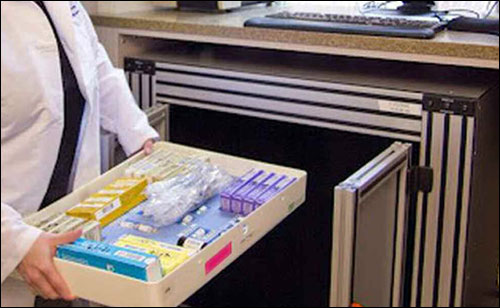
As pharmaceutical manufacturers and distributors begin considering RFID-tagging for inventory control or temperature monitoring, they should factor in the value add it could deliver to customers, suggests Michael Liard, VP of Auto-ID at VDC Research. “You could improve internal operations and enhance customer service,” he says. “It can differentiate you from your peers. That’s a key role and becoming a bit more attractive to pharmaceutical manufacturers.”