Manufacturing executives, recruiters and hiring managers know firsthand what we see in the headlines: there’s a shortage of workers to fill open manufacturing jobs, and that shortage is expected to grow in the next few years. This skills gap is caused by factors like low unemployment, a wave of worker retirements and what the National Association of Manufacturers calls “a massive perception problem” about manufacturing jobs among young adults.
Because of this, many companies are seeking Internet of Things (IoT) solutions to adapt to a smaller workforce. A 2018 Deloitte and Manufacturing Skills Institute report found that half of the manufacturers it surveyed were using new technologies to meet demand despite the talent shortage, such as machine learning and artificial intelligence, two key components of the IoT.
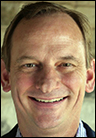
Many companies find that the IoT not only helps them keep going with a smaller staff, but also delivers improvements they couldn’t have achieved by simply hiring more employees. To get the most from IoT technology with fewer workers, it’s important to understand how the Industrial Internet of Things (IIoT) can impact areas like efficiency and productivity, worker instruction and training, and worker safety.
Efficiency and Productivity Growth
The area in which the IoT has had the biggest impact so far is efficiency and productivity. Remote wireless sensors can provide equipment data for analysis to enable predictive maintenance, which can increase uptime by as much as 20 percent. It can also reduce the amount of time employees spend on scheduled maintenance and on repairs following equipment failures.
Triaxial vibration sensors on equipment can chart utilization, which can vary from one shift to the next. In cases in which the data shows that equipment is underutilized, the solution may be better training rather than hiring more workers or adding more equipment.
Wireless remote sensors can also reduce the amount of time workers spend on repetitive tasks like manual temperature and humidity readings, so they can focus on higher-value tasks. As an IoT network builds a database of sensor readings and analysis, quality-assurance teams and management can mine that data to look for more opportunities to improve efficiency. Wireless equipment sensors offer other benefits, too. Manufacturers that produce equipment can monitor it remotely to support predictive maintenance, troubleshooting and real-time support for their customers. This can reduce the number of service calls their employees need to make.
Worker Instruction and Training
Wireless equipment sensor data can help experienced workers train new personnel on equipment. For example, someone who has been working with a piece of equipment for years may be able to detect subtle changes in sound that could indicate a potential problem. If that worker is approaching retirement age, his or her knowledge could be lost since new workers would lack that skill set. With sensor data, the experienced worker could show new employees visual cues that correlate with his or her experience-based knowledge, in order to help prevent unplanned downtime.
IoT-connected equipment can also be used to create a “digital twin” of a production line or piece of equipment that workers can experience by wearing an augmented reality (AR) headset. This setup lets trainees virtually experience the real-world setting in which they will work, without the risk of production errors and—in the case of high-risk work—the risk of injuries that could sideline those employees. It also enables one experienced worker or manager to train multiple workers in detail without reducing the quality of training.
For workers on the job, digital instructions with real-time data from the plant’s IoT network can feed them the information they need, exactly when they need it. This can make workers more productive by reducing the amount of time they need to spend looking for instructions and data. Moreover, real-time information and instructions can reduce errors that affect quality and uptime.
Enhanced Worker Safety
On-the-job injuries and illnesses led to at least 118,000 days away from work for employees of U.S. manufacturing companies in 2018. An IoT that includes wireless sensors, motion detectors and video monitors could help workers stay safe and reduce workdays lost to injury. For example, wireless IoT sensors that monitor temperature and vibration levels can generate alerts if there’s a potential safety problem with equipment or ambient temperatures, enabling workers to clear the area. Air-quality sensors, meanwhile, can report unsafe levels of chemicals before workers would be exposed.
Location sensors and motion detectors can alert personnel to the approach of heavy equipment as they move through a warehouse or plant. Wearable sensors can alert managers if a worker falls, overheats or moves into an unsafe area of the plant. Wearable location sensors can also help track employees in the event of an onsite emergency, so as to make sure everyone is accounted for.
Because the skills gap in manufacturing is a fact of life now and for the near term, it’s important to rethink what workers on the factory floor need to do and how they need to do it. By automating equipment data collection, analysis and display, a network of wireless sensors can enable efficiency gains, streamline training and workflows, and reduce time lost to workplace injuries. Together, these improvements can help manufacturers make the most of the workers they have and continue to grow.
Ray Almgren is the chief operating officer at Swift Sensors, a developer of cloud-based wireless sensor systems for industrial applications. Prior to his role at Swift Sensors, Ray was the VP of marketing at National Instruments. Ray received his BS degree in electrical engineering from the University of Texas at Austin. He is the founder and a current board member of FIRST in Texas, as well as a member of the National FIRST Executive Advisory Board, and has served on several engineering advisory boards, including The University of Texas at Austin, Southern Methodist University and Tufts University.