In the world of modern electronic devices, few products have seen faster adoption rates than wearable devices. With new sensor technology, multiple interface capabilities, customer-defined parameters and automated software updates, this market is expected to see continued growth for a long time.
Manufacturers are looking for new and permanent methods of authenticating their products, and for storing important information internal to those devices, without interfering with the products’ feel, function and overall aesthetics. (Aesthetics is a particularly important consideration, as today’s wearables not only have become more sophisticated, but are approaching designer status, with many fashionable options available.) One solution being adopted is radio frequency identification. This approach requires that an RFID tag be embedded into a wearable device during the manufacturing process.
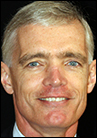
Today’s integrated RFID tags can be as small as 2.0 millimeters by 1.25 millimeters (0.08 inch by 0.05 inch), with 512 bits of user-defined memory. Their ability to withstand overmolding processes allows these tags to be embedded into the smallest wearable products available. Once a tag is embedded, it becomes a permanent fixture of the device and is readily able to store important information defined by the manufacturer. As such, it also removes the need for unsightly external markings or labels.
Since RFID is a wireless technology, communication to the tag is achieved using an industry-certified RFID reader-writer, along with a small loop antenna. Typical read distance of these ultra-small tags is 5 to 10 millimeters (0.2 to 0.4 inch). Since these tags are passive, energy is harvested from the reader-writer, allowing data to be added and retrieved at any time during the manufacturing process. Should this data require modification, a quick and easy process of updating is carried out via the same RFID reader-writer, without the need to open up the device. Information commonly stored on the tag includes product serial numbers, as well as production location and quality-control (QC) data. With high-security features, these small RFID tags also allow the wearable device’s manufacturer to lock down a tag, thereby preventing unauthorized access to data on the device to which it is attached.
RFID can also be used to verify a product should it be returned for warranty or repair work, as authentication can be quickly accomplished by verifying the tag’s information. If a tag is not found, the product can be returned to the consumer without proceeding further, thus saving valuable time. It also ensures brand protection, which is becoming increasingly important to companies since it affects sales, market position and company image.
Embedding RFID Summary
• Aesthetics improvement: Embedding a single RFID chip into a device can eliminate the need for external markings to preserve that product’s slick look and feel.
• Secure and permanent: The technology is capable of locking down tag data.
• Expandable: Multiple departments can utilize the features of using RFID (production, QC and so forth).
• Authentication: Product verification becomes feasible.
• Modifiable: Data can be updated or changed.
• Ultra-small: The small tag size allows for embedding in the smallest wearable products.
• Brand protection: Product and company image can be maintained.
As the next generation of feature-filled wearables hit the market, manufacturers continue to seek ways in which to define and differentiate their own products. Embeddable RFID tags represent an easy and efficient approach, well suited to the wearables industry.
Gerry Hubers is the North American business-development manager at Murata Electronics, a manufacturer of electronic components and solutions, including RFID.