It has been commonly believed, and widely repeated, that the barrier to passive ultrahigh-frequency (UHF) RFID adoption is the cost of the tags. Deeper investigation and critical thinking indicates that while price is a contributing factor in certain applications, there are other problems that the industry must address in order to accelerate the technology’s adoption. I believe that there are four challenges limiting RFID adoption: tag cost, industry fragmentation and segmentation, the cost of software infrastructure replacement, and the technology’s environmental dependence.
Cost of Tags
This isn’t generally the problem. Although tag cost is often cited as the biggest obstacle, it is really only an issue in open-loop applications. Such applications are those for which a tag is paid for and affixed to an object by a user that will then ship or transfer the item to another user outside his or her system, and thus lose the ability to gain additional value from the tag. An example of this is a supplier tagging a pallet right before it goes out the door to a distributor or end customer.
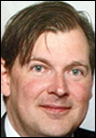
The cost of tagging or labeling is truly measured against the benefit gained each time the object is scanned. In open-loop applications, the opportunities to benefit from an RFID tag are limited, making the break-even tag price much lower. In contrast, closed-loop applications may offer hundreds, thousands or even tens of thousands of incremental benefits as a tag is used over and over again. A closed-loop application involving reusable bins or totes in which sanitization destroys bar codes is a prime example. Here, a bar code is good only for a single use, but RFID tags may be used for years. In this particular example, a typical manufacturer using RFID tags may save more than $100,000 annually versus the cost of utilizing bar codes, based solely on the benefit of RFID’s increased durability.
If tag cost were the only factor limiting adoption, we would have seen widespread deployment of RFID in closed-loop applications years ago. Since this clearly isn’t the case, the argument that price is the problem breaks down. Although price certainly matters in the wide array of existing open-loop applications, ignoring the other issues has been a significant factor limiting RFID’s adoption.
Industry Fragmentation and Segmentation
Industry fragmentation refers to the lack of dominant suppliers. There are so many choices for customers seeking RFID solutions that the selection task becomes daunting, and it is easier to hold off on making a change. Recent consolidation in the industry has certainly helped, but more is necessary.
Industry segmentation refers to the wide array of suppliers required to pull together a complete solution. Customers typically find their way to the suppliers of tags and readers, but tags and readers alone do not solve customer problems. A complete RFID solution requires design, readers, antennas, tags, brackets or enclosures, cabling, RFID middleware, application software, software-integration services, installation services and training.
The average project requires so many different suppliers and vendors that projects are difficult to manage, and the lack of any scale means the infrastructure deployment cost is significant. The project risk and the time required for completion increase with each supplier involved. A lack of systems integrators with RFID expertise has placed the bulk of this integration risk onto the end customer. It is like asking someone to buy all of the pieces of a vehicle separately and then build his own car. Although the industry is making an effort to assure interoperability by adding more standards, this problem will not be solved until the burden of system design, procurement of all necessary components, and installation and support is removed from the end customer and consolidated with a single vendor—an RFID integrator.
Cost of Infrastructure Replacement
The RFID industry evolved separately from the rest of the automatic-identification sector. The technology was first driven by semiconductor companies with a primary interest in the volume of tags that could be sold. In order to sell tags, these firms began producing reference designs and chips for the infrastructure, or reader, side of the transaction.
Although these semiconductor companies brought significant expertise in physics, technology and chip-level design, they lacked system-level experience and, more importantly, knowledge of current practices in the auto-ID industry. As a result, there was a significant technology gap between the output of RFID readers and the infrastructure that customers had to support bar-code scanners.
Software engineers with experience in high-level application and database software have attempted to bridge the gap with RFID middleware. This software has often been expensive, frequently limiting the end applications that a customer can use without significant customization expense, and typically has poor real-time performance. Creating and positioning RFID as a standalone solution, separate from the technology customers currently use, forces customers to repurchase perfectly good infrastructure. Additionally, RFID becomes an all-or-nothing transition from bar codes.
In contrast, look instead at the transition from bar-code scanners that use lasers to those employing image sensors—a nearly seamless transition with rapid adoption. The key difference is the backward compatibility and similar connectivity to existing infrastructure. Although the transaction between the target (a bar code) and the infrastructure equipment (the scanner) requires a completely different technology and front end, the back ends of these two types of bar-code scanners are the same. This allows customers to integrate either technology into their existing infrastructure, both technologies to be used in hybrid solutions, and one technology to be swapped for another without changing the infrastructure as the customer’s needs change over time.
To fix this problem, the industry needs RFID solutions that achieve both interoperability and backward compatibility with the bar-code-driven infrastructure that evolved over the last 40-plus years.
Environmental Dependence
In my view, the most difficult problem to overcome will be the technology’s environmental dependence. By this, I refer to the fact that no two RFID deployments are exactly alike since the 915 MHz RF energy used in the RFID transaction is impacted by the building and surroundings in which you deploy it. This impacts both the tags and the infrastructure. Tag vendors have made significant progress throughout the past five to 10 years in making the tags perform better in the presence of moisture and metal.
Service has improved to a level at which customers can now send sample items to a tag supplier and have the engineers there choose the proper tag and ideal placement. However, on the infrastructure side, customers obviously cannot send out their shipping dock to determine the proper power settings, shielding requirements, antenna selection, or mounting and angling of antennas.
This means an experienced RFID engineer or technician needs to physically visit the site. Ideally, customers enlist this level of assistance at the design stage so that business processes and technology capabilities can be balanced. In addition, this allows the selection of the correct reader, antennas and solution form factor. Many projects have failed and many customers have been left unhappy because the site-specific impacts were not dealt with. In my view, this factor alone has caused much of the negative publicity regarding RFID performance.
Again, compared with RFID, a bar-code deployment is much easier. Installation focuses on easily measurable distances and angles, and setup in all but the most complex applications does not require a Ph.D. or years of experience. In many applications, bar-code equipment can be purchased from distributors and deployed by the customer. This is unlikely to ever be the case for RFID. However, the industry can do a lot more to minimize this problem. Better, experienced systems integrators are needed, and customer awareness of the importance of proper upfront design and installation support must be increased.
Enabling Wider Adoption
Anyone who has been involved in the RFID industry knows that the rate of adoption has been a disappointment. Focusing on RFID tag pricing to solve the adoption problem is a mistake, especially since we will likely see diminishing price reductions from today’s tag cost. Instead, the industry should focus on fixing the underlying problems with infrastructure and deployment.
Specifically, we need further industry consolidation, better full-turnkey-capable systems integrators with RFID experience, an evolution of the RFID back end that is compatible with and embraces 40-plus years of bar-code auto-ID technologies, and improved customer education to help users understand that solution design and the deployment site greatly impact performance.
Jack Romaine, the CEO of Element ID Inc., is a member of AIDC 100 and has decades of experience in auto-ID. He is the co-inventor of a few integrated RFID solutions and an automated system of contactless dimensioning. He started the RFID group at Accu-Sort Systems in 1997, worked as a sell-side financial analyst for SG Cowen covering semiconductors and RFID, and was named Bloomberg Markets magazine’s “Semiconductor Analyst of the Year” in 2003.