Vendor-managed inventory (VMI) is a common business practice between suppliers and their customers. The inventory supplier (the vendor) is responsible for keeping inventory of specific products at an agreed-upon location and within established minimum and maximum levels. Vendors often retain ownership of the inventory until it is “consumed” by the customer.
Since this is a valued customer service, it’s essential for the vendor to maintain the set inventory levels, which requires timely visibility into what products are consumed and replenished. In practice, vendor representatives usually visit the site regularly to check inventory levels, or the supplier relies on customer consumption reports. The first method is costly and hard to time. The second is not always reliable.
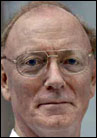
RFID can automate the overall process—providing suppliers with near-real-time visibility while reducing costs and errors. Suppliers and customers that adopt RFID for electronic proof of delivery, which I discussed in my last column (see An Impartial Observer), can build on that deployment to enable auto-replenishment. Suppliers would already be tagging goods so customers can track them automatically on the receiving dock.
Some companies store goods in a shared inventory area. But VMI requires a separate area with a fixed RFID reader. When goods are moved from the receiving dock, RFID confirms they are in the VMI inventory location. When product is moved out of the VMI location, RFID confirms exactly when the customer has consumed it and it is no longer managed by the vendor.
Supply-chain partners can use the Electronic Product Code Information Services (EPCIS) standards to share information securely. That way, the vendor can use the VMI data to trigger replenishment if the inventory level falls below minimum. The vendor would also know when to invoice the customer for what it just bought. In addition, there would be traceability in the event of a recall. EPCIS messages are generally sent and received in XML format using Web services, so little software development is usually required. Some enterprise resource planning software has this capability built in.
Suppliers could authorize their customers to use RFID handheld readers to facilitate picking of VMI, which would benefit both supply-chain partners. The customer would know it picked the correct items. Products with some form of expiry, such as coated heart stents, could be identified automatically when picked, and an alarm could be triggered if they should no longer be used. Picking could even be directed so the item with the shortest remaining period of use is picked first, minimizing inventory write-offs.
RFID-based auto-replenishment will not completely eliminate the need for suppliers to conduct periodic physical inventory checks. But it does create a valuable link between the vendor and the inventory it owns at the customer site.
Ian Robertson is CEO and president of Supply Chain RFID Consulting, a Texas-based firm providing services to companies that want to understand how to use and implement RFID internally and with partners. Send your supply-chain questions to [email protected].