I have offered presentations to many high-level executives at big companies looking to understand what radio frequency identification can do for their operations. I tell them they have squeezed so much inefficiency out of their organizations with the information technology they’ve invested in that there is little more than can be done without implementing a new technology, such as RFID.
Some organizations already get this. At RFID Journal LIVE! 2013, Balaji Suresh, the materials manager of UTC Climate, Controls and Security at Carrier, presented a case study about how his company took a highly efficient, highly complex, vertically integrated manufacturing operation and made it even better.
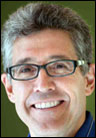
Carrier manufactures heating and ventilation equipment. The factory produces a wide variety of products, and finishes a unit every five seconds. “It’s a high-velocity environment, and we have applied a lot of lean manufacturing techniques,” he told the audience. “And we’ve been recognized for manufacturing excellence. In 2011, we were an Industry Week Best Plant.”
In 2009, the company conducted a trial of RFID technology on a production line, to confirm that every tag could be read every time. There could be no exceptions in a highly controlled factory environment. When testing proved that 100 percent tag reads were possible, Suresh decided to go ahead with the project. Its goals were to improve safety and efficiency in shipping, streamline assembly, make it error-proof and build an infrastructure that would support future factory enhancements.
The business benefits were clearly analyzed and quantified, and the team received approval to invest “hundreds of thousands of dollars.” It took nine months to take the system live. The company received a return on its investment in less than two years.
The goal of increasing safety was achieved. “There was a significant hazard reduction,” Suresh reported. “When it comes to shipping, we had operators interfacing with the units in high-traffic areas. We completely eliminated that aspect of the job.”
There was an 80 percent to 90 percent reduction in shipping errors, and productivity jumped 33 percent. “This represents structural cost reductions that we can reap benefits from down the road,” he said. “This was a very successful project for us.”
The benefits to the company are significant. But Suresh made a very interesting point in an interview after his presentation: the benefits could not have been achieved without RFID. “We had already reached a certain level of performance, so the traditional methods of bringing in industrial engineers to get more productivity out of this process was not going to work,” he stated. “We had to change our approach, and RFID was the only solution.”
I have been telling senior executives for several years that the only way to achieve significant process improvements, as well as major jumps in productivity and efficiency, given how much productivity has improved during the past two decades, is to focus on a new technology with new capabilities—namely, RFID.
Of course, RFID doesn’t magically guarantee a huge boost in productivity. Like Carrier, companies must take a disciplined approach. But RFID enables manufacturers to streamline processes, reduce errors and manage real-word objects—parts, raw materials, work-in-process, tools, finished goods and so on—in a way that was not before possible. Those who understand this will be able to take their operations to a higher plane.
Mark Roberti is the founder and editor of RFID Journal. If you would like to comment on this article, click on the link below. To read more of Mark’s opinions, visit the RFID Journal Blog, the Editor’s Note archive or RFID Connect.