Since long before Japan’s nuclear disaster focused the world’s attention on the potential dangers of nuclear energy, managers and researchers at Argonne National Laboratory, a U.S. Department of Energy (DOE) facility, have been concerned about tracking nuclear materials. The stakes are almost unimaginably high. If terrorists were to get their hands on just a single container of nuclear materials, it could conceivably result in the destruction of a major city.
Argonne National Laboratory, approximately 25 miles southwest of Chicago in the Argonne Forest section of the Cook County Forest Preserve, is a direct descendant of the University of Chicago‘s Metallurgical Laboratory, part of the World War II Manhattan Project. At the Met Lab, on Dec. 2, 1942, Enrico Fermi and some 50 colleagues created the world’s first controlled nuclear chain reaction. In 1946, the Argonne Lab, as it was then called, became the country’s first national laboratory, given the mission of developing nuclear reactors for peaceful purposes. Argonne designed, built and tested the prototypes for the commercial reactors that currently produce 20 percent of the nation’s electricity.
|
Today, Argonne employs approximately 3,200 staffers, including roughly 1,000 scientists and engineers. The lab’s three general research areas are energy storage, alternative energy and nuclear energy. In 2005, Argonne researchers began laying the groundwork for using radio frequency identification to accurately track and monitor storage containers of nuclear materials at multiple DOE sites.
“In the early 2000s, RFID was hyped very much,” recalls Yung Y. Liu, Argonne’s group manager for packaging certification and life-cycle management. In those days, Liu and his colleagues paid close attention to the tracking initiatives being organized by Wal-Mart Stores, the U.S. Department of Defense and several other large enterprises. “It sounded a lot like what we wanted to do,” he says. “If they can track their things, why can’t we track ours?”
With that in mind, Liu and his colleagues began thinking of ways to use RFID to automate an existing and largely manual nuclear materials management system. “It’s paper and pencil, and then data entry,” Liu says, describing the current process. “And then it goes to a spreadsheet… and then a file that gets filed in a filing cabinet.”
RFID would let DOE managers access a continuously updated database of nuclear materials, one that could be used to pinpoint the location of a specific container within seconds. The system would provide the visibility necessary to keep the nuclear materials safe and secure. It would allow, for the first time, item-level tracking and monitoring. “These drums—there are hundreds of thousands of them, and they’re all over the United States at DOE sites,” Liu says.
Pick Your Poison
DOE’s hazardous materials can be organized into three general categories. “At the top of the list are the nuclear materials,” Liu says. These include extremely hazardous substances such as uranium and plutonium. “Next you have radioactive materials,” he says. These substances, byproducts of a nuclear process, can be highly, moderately or mildly radioactive. “The highly radioactive materials carry the same concerns [as nuclear substances],” he says.
People with specialized knowledge and devious intentions can use stolen radioactive materials to create a dispersion device known as a “dirty bomb,” Liu says. Such a bomb could be used to contaminate a wide area, potentially harming people and rendering affected land or water unusable for years or decades. “We know we have international terrorists who target the Western society for violent acts,” Liu comments.
At the bottom of the hazardous materials list are chemicals and other types of materials that are neither nuclear nor radioactive, yet if accidentally or intentionally released could cause harm to people and/or the local environment. “Anything about which you care to know its whereabouts… is what we’re interested in tracking,” Liu says.
Developing a Strategy
The first step toward creating an RFID-based tracking and monitoring strategy for nuclear materials was taken in late 2005, when Liu and a colleague wrote a white paper describing a proposed system and submitted it to the DOE. After receiving a favorable review, the team began developing and testing prototype RFID tags to see how well they would perform in various situations, including radiation-saturated environments. “We needed to know,” Liu says, “if we have a tag in an actual storage environment with limited radiation exposure, how many years can we get out of it?”
From the outset, Liu and his staff knew that active tags were essential. The devices would have to be read over distances of at least 25 meters to 30 meters (82 feet to 98 feet), as well as from inside vehicles. “Because of the storage environments’ [radiation and distance], we can not use passive or inductive-coupling types of devices,” Liu says.
The team chose Savi Technology’s ST-676 tag as a starting platform for irradiation testing, because of its active design and successful track record in government applications. “Savi has sold many ST-676 tags to the Department of Defense,” Liu observes.
The stock Savi tag had some inherent shortcomings, including a single lithium battery with a three- to four-year operating life. While such a lifespan is adequate for most RFID applications, it falls far short of the time needed to track a container of dangerous materials that’s likely to hang around for decades. “So we came up with a design that uses four lithium batteries,” Liu says. “We also have a battery- management board that will run these batteries in series, so as one drops out it will switch to the next one.” The batteries are replaceable, he adds.
Argonne researchers also developed a pressure-sensitive seal sensor and a drum-compatible housing for the tag. “The ST-676 was designed for the ISO containers; you can’t attach it to a drum,” Liu says. The final device was informally dubbed “The Ph.D. Tag” because, Liu says, “it was developed by a bunch of Ph.D.s with a soldering iron.” The tag was later given the formal designation “MK-I.”
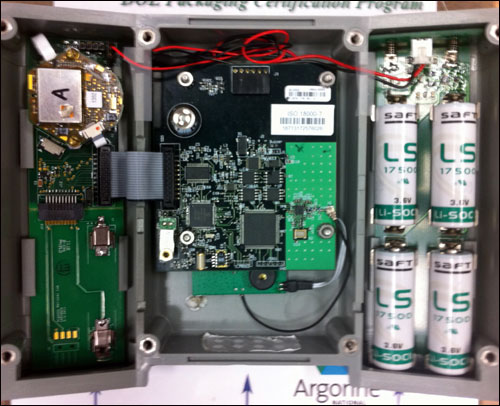
Trial Run and Pilot Project
In early 2008, Argonne launched a trial with 14 prototype tags attached to an equal number of empty drums. The drums were transported by truck on a round-trip journey from Argonne to the Savannah River National Laboratory, in Aiken, S.C. (including a stopover at the Oak Ridge National Laboratory, in Knoxville, Tenn., on the return trip).
Along the way, researchers experimented by reading the tags from within the trailer and relaying the information with satellite and cellular vehicle tracking devices in the cab, and staging a series of incidents to test the system’s automatic alarm notification and emergency response capabilities. Everything worked as expected, Liu says, with the system sending a steady stream of drum and vehicle location information to a central monitoring station at Argonne. More than 50 stakeholders across the country observed the trial run in real time via a secured Internet link.
After studying the trial’s data and making a few tweaks to the technology, Argonne hired a contract manufacturer to produce several hundred MK-II tags. The final design was patented under the name “ARG-US RFID Surveillance Tag” in January 2009.
Over the next two years, using the production-quality tags, Argonne researchers studied how their system would operate under various real-world conditions, including on the road and inside buildings and storage yards. The researchers then returned to the Argonne-Savannah River circuit for a pilot study, dubbed “Phase One, Category-I Vault Testing Program,” that lasted six months (from March to September 2010), during which the system functioned without any major problems, Liu says. Another pilot study, completed in November 2010, was the integration of the ARG-US RFID system with a long-established DOE satellite vehicle-tracking system designed to coordinate shipments of hazardous radioactive materials. The pilot monitored a pair of drum-carrying vehicles for 6.5 hours while they traveled separate 300-mile routes near Chicago. “If we can monitor two, then we can also monitor 50 or even 100,” Liu says.
Today, Argonne continues to refine its tag technology. “We are well on our way to MK-III,” Liu says. “MK-III RFID will have a radiation detection module added, and that’s going to open up a whole new area of applications.”
The technology, he notes, has the potential to become a standard for tracking and monitoring nuclear and radioactive materials at both government sites and commercial facilities. “This system, if we can get it adopted by the utilities, hospitals and industries, could be used not only in the United States, but potentially in other countries as well,” he says.
Liu reflects on the recent nuclear disaster in Japan. “Imagine if MK-III RFID tags were part of the infrastructure of the nuclear power plant in Fukushima that was hit by the giant earthquake and tsunami on March 11,” he says. “The recovery effort would have been made much easier, as the radiation field at all key locations of the plant would have been known in near-real time.” The stored sensory and history data in the tags would have allowed the plant operator to reconstruct the events and optimize the recovery strategy, he notes. “As the tags are battery-operated and located throughout, it would be unlikely that they all would be damaged and rendered ineffective by the same event initiator, such as the earthquake and tsunami,” he says.
Ready to Roll
Only one final obstacle prevents Argonne from rolling out the RFID tracking system—securing funding. Money, as it turns out, may prove to be the project’s most difficult challenge.
With the federal debt soaring and a growing number of lawmakers and administrators looking to cut expenses wherever possible, getting the funds necessary to launch the system won’t be easy. Yet Liu is optimistic. “I think it’s probably going to happen in the near future,” he says. “But I don’t know if it will happen this year.”
When the money finally does arrive, Liu feels he can begin a phased deployment of the system almost immediately. “I say three months, but I don’t envision this would occur all at once,” he says. “It’s likely that one facility that already has a large number of containers will be selected to begin the deployment. “Real-time, remote radiation monitoring at nuclear power plants is an area of application for ARG-US RFID that deserves very serious consideration,” he says.
To learn about this year’s other winners, see 2011 RFID Journal Awards: Excellence in RFID.