—Antolini Luigi & Co. S.p.A., an Italian producer and distributor of granite, marble and other stone products, is using RFID to track the manufacture and location of the 900,000 slabs of polished stone it sells each year, as well as the large blocks of rock from which the slabs are cut. The finished products are sold to a global network of distributors, and many end up being used as flooring or countertops in high-end interiors for luxury hotels or homes.
The system, which uses customized UHF EPC Gen 2 passive RFID tags, allows the company to determine its inventory with 80 percent more accuracy than before it used RFID and makes it easier for employees to locate the finished slabs—some of which are worth up to €10,000. The company also estimates that using RFID to track and trace its products within its facility reduces its labor costs by 40 percent, since many of the steps that used to be manual—such as counting inventory and generating reports—are now automated.
When a large block of unfinished material arrives at the company’s factory in Verona, Italy, a label in the European standard A4 size (slightly larger than a U.S. 8.5-by-11-inch sheet of paper) is attached, with an adhesive, to the slab. The label is covered in a waterproof material so that it can withstand exposure to weather and the dust and vibrations inside industrial stone-cutting machinery. Encoded to the passive UHF Gen 2 tag embedded in the label is a unique alphanumeric ID number used to identify the slab during each phase of its processing.
When the large block is ready to be processed, it is positioned in front of a cutting machine, where a Feig Electronic LRU2000 EPC Gen 2 reader is mounted, with its antennas positioned to capture the ID number encoded to the tag. The reader captures this code and sends it to a software application developed by the project system integrator F.C.S. Solutions. This software sends the ID number to Antolini’s production management system, which tracks all of the slab production at the plant.
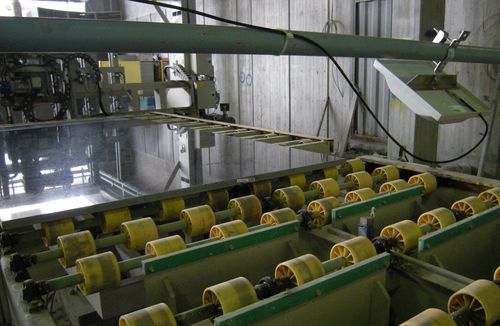
The machine cuts the large block into a number of smaller, polished slabs. These slabs vary from 90 centimeters by 155 centimeters in size to 205 centimeters by 340 centimeters, and their weight varies greatly based on the type of stone.
At this point, the cut slabs are put through other machines that give each slab the polish or surface treatment required to fulfill the order. Once this step is done, an Antolini employee uses a handheld EPC Gen 2 reader to collect the ID from the A4 label that is still attached to one of the cut slabs (an end piece). He or she then manually attaches a small EPC Gen 2 RFID label to the edge of each individual slab and uses the reader to associate the label places on the finished slab with the ID encoded to the larger label used to identify the large block from which the slab was cut.
Softwork, the provider of hardware for the deployment, had a third-party converter custom-make these small tags specifically for tracking the cut slabs. The tags, which contain Impinj‘s Monza 3 chip, are embedded in high-density polyethylene to protect them from weather and dust (the cut stones are stored outside). They are less than an inch wide, so they fit onto the edge of any slab produced at the plant.
The software running on the reader associates each of the ID numbers from the customized tags with the tag number encoded to the A4 label, and forwards this data to the production-management software through a wireless network. This way, the individual slabs will always be linked to the large, raw block from which they were cut.
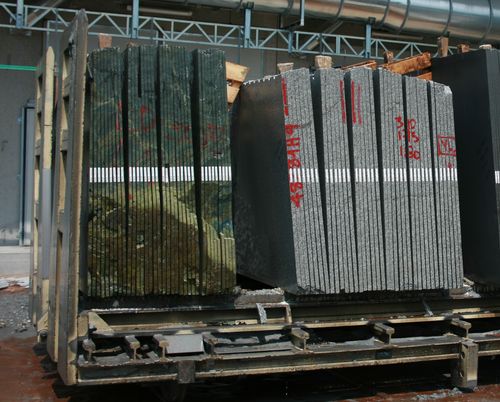
The individual slabs are stored in racks in the plant’s stockyard. A specialized EPC Gen 2 tag, made by Confidex and designed for mounting onto metal surfaces, is attached to each rack. After the cut slabs are placed onto a rack, the employee collects the ID number of the rack’s tag and associates it with the IDs from the slabs’ tags. Then, when an employee needs to retrieve a specific slab later, he can simply call up its rack number, which is saved to the production software.
To perform semi-annual inventory of every block and slab in the entire stockyard, which is roughly 200,000 square meters in size, employees use the handheld reader to walk up and down each rack in the stockyard and collect the unique ID from each tag. Before using RFID, it took two Antolini employees two days to manually collect the ID numbers used to identify each piece of stone. Now, it takes one employee less than three hours to take inventory of all its blocks and slabs, which includes up to 30,000 large blocks and 100,000 finished (cut and polished) slabs, on average.
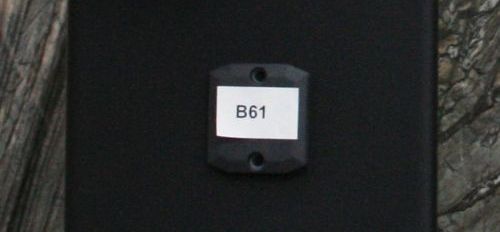
When fulfilling orders, Antolini also uses the RFID tags to find specific slabs in the stockyard. Workers know the rack location of each slab by referring to the inventory records in the stockyard management software. Once they find the rack, they use the handheld readers to collect the tag ID associated with the slab being purchased and automatically update the inventory records to show it is being retrieved to fulfill an order.
Antolini had earlier tested bar code and high-frequency RFID systems before settling on the passive UHF system, called StoneID, that it deployed. These other technologies did not provide the read distance or reliability that the UHF system provides, explains Paola Visentin, Softwork’s marketing and communications manager. The passive HF tags it tested required that the employees get very close to each tag to read it, so performing inventory of the tagged slabs or locating them was not as easy as the company had hoped. And bar codes, while the cheapest auto-ID option, are difficult to reliability read in a dusty environment such as the plant.
Minera Norge, a Norwegian company that manufactures slate tiles, blocks and related products, is also using RFID, as well as GPS technology, to track its finished products, as well as the forklifts used to transport them (see Slate Maker Adopts System to Track Products, Even When Buried Under Snow).