Thanks to an RFID system that tracks hotel furniture from the point of assembly until the moment it is shipped to a customer, Solid Comfort has eliminated the need for two full-time staff members, while also reducing the amount of shipment errors and confusion regarding what has been delivered. The system was provided by AbeTech, based in Rogers, Minn.
Solid Comfort had two challenges it wanted to address with an RFID system, explains Ryan Larkin, the furniture manufacturer’s VP—locating each piece of furniture (which includes bed headboards, mirrors, desks and credenzas) after it has been assembled but before it is shipped at the company’s 100,000-square-foot warehouse in Fargo, N.D.; and tracking when and where orders are shipped, in order to ensure they are complete and accurate. Historically, Solid Comfort had employed two full-time workers to manage that information. One walked throughout the warehouse and production area, tracking which items had been made for any specific order, as well as where they were stored as the orders were prepared for shipment. The other employee monitored the movement of product onto trucks, thereby ensuring the proper quantity of specific goods was loaded onto the correct vehicle.
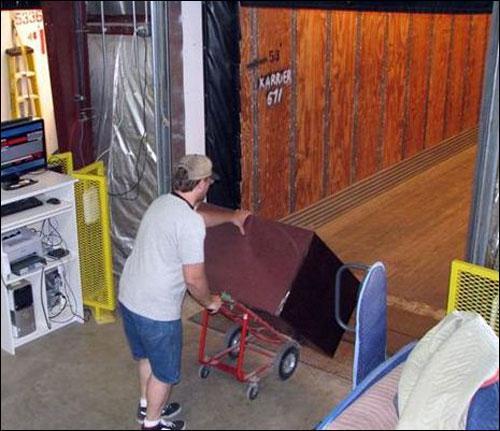
Even with these efforts in place, Larkin says, things still went wrong. If a hotel received a shipment and believed the quantity of pieces was inaccurate, for example, it would call Solid Comfort and request the items it believed were missing. In some instances, the manufacturer created additional pieces, putting its other production on hold, and shipped them to the hotel. “In that way, it can cost us $500 to replace a $200 piece,” he explains—and sometimes, the hotel located the missing furniture after the fact.
So in 2009, Solid Comfort began working with AbeTech to develop a solution. The companies went ahead with the deployment in two phases, Larkin says. With phase one, implemented at the end of last year, tags are attached to pieces of furniture after assembly, and are used to track when the items are complete and placed in the warehouse for shipment. When a hotel places an order, the staff inputs the information in an RFID software application custom-designed by AbeTech, and running on a back-end server. That information also includes the name of the firm that placed the order, along with the time and date when it was placed.
Later, when each piece is fully assembled, the production staff uses a Zebra Technologies RFID printer-encoder to write a unique ID number to an EPC Gen 2 passive ultrahigh-frequency (UHF) tag embedded in an adhesive label, and then print that same ID number, as well as the order information, on the label’s front. The tag’s ID number, stored in the back-end software, could also be linked to such information as the room in which the piece of furniture should be placed, and on which floor of the hotel, if that level of detail was provided with the customer’s order. Employees would then hand-write their own personal ID number on each label.
When the furniture is transported from the production area to the warehouse—typically being pushed on a pallet on wheels—it passes through a portal consisting of an Alien Technology reader wired to the back-end server. The reader captures each tag’s unique ID, and the AbeTech software interprets that number, links it to the order number and updates the item’s status as having been sent to the warehouse, explains Eric Soderholm, AbeTech’s account executive. Every time the portal reads a tag, a 24-inch monitor wired to it flashes green.
The staff now tags between 5,000 and 7,000 pieces of furniture every month. Initially, Larkin says, there was a problem reading the tags, though that issue was resolved when the firm replaced the printer-encoder, which was found to be defective.
According to Larkin, the first phase of the deployment enables him to view the progress of an order, and see how long it takes to fill that order, from the moment it is placed to when the completed pieces are moved into the warehouse. If a customer calls in for a status report, the AbeTech system can immediately show him whether that order was completed—and, if not, the number of pieces that still need to be assembled.
Once Larkin was satisfied with phase one, his company began working on the second phase—using RFID to track the loading of products onto trucks. AbeTech installed an Alien reader at the door to each of its two loading docks, in order to capture each item’s tag ID number. The AbeTech software knows through which door each furniture piece should pass, based on the specific vehicle being loaded and its destination. For example, if one truck is destined for Minneapolis, and another for Fargo, the system will recognize an error if an item intended for Minneapolis is loaded onto the Fargo-bound vehicle. If that happens, the portal’s 24-inch monitor displays an error message, alerting the staff that the wrong item is being loaded.
Once the loading process is complete, Solid Comfort has an electronic record indicating which items have been put on which truck, and can thus ensure that the order is complete and accurate.
When the truck arrives at the hotel, the hotel staff can begin unloading the furniture, and can use the printed text on the RFID labels to identify each piece, as well as the floor and room in which it belongs. If an item is broken or seems incorrect, the hotel staff can call Solid Comfort and provide the ID number printed on that piece’s label, which the company’s workers input into the AbeTech software. This enables Solid Comfort to easily determine which piece of furniture it is and where it belongs, in addition to which replacement parts might be required if it was broken.
The full system (both phases one and two) has been operating for the past six months, Larkin says. “It’s had a dramatic effect on how accurate we are,” he states. The use of RFID has reduced errors based on misloaded items, and helps organize the loading process if a large order does not fit onto a single truck. In the past, he says, this scenario could be especially challenging, since items might get put away, moved or incorrectly loaded onto one vehicle, while awaiting another truck to pick up the remainder of the order. With the RFID system, he notes, this confusion is eliminated.
Moreover, Larkin reports, he has been able to eliminate two full-time jobs that were previously spent tracking the location of finished product, and has reassigned those employees to other tasks. In addition, he says, there are now fewer calls from customers regarding incomplete or inaccurate orders. “I think my staff would lose it,” he states, if the system were uninstalled. He believes he has already recouped the cost of his company’s RFID technology investment.