Zimmer Ohio, which has exclusive rights to sell and distribute orthopedic products and instruments manufactured by Zimmer Inc., is installing an RFID system that it expects will reduce the labor hours of its inventory staff by several hours a day, while also increasing the visibility of its high-value items as they are shipped to hospitals and then returned.
Zimmer Ohio provides Zimmer’s line of orthopedic implants and surgery tools to Ohio-area hospitals. Typically, when a surgeon schedules a surgical procedure, such as a hip replacement, the hospital at which he or she works may place an order with Zimmer Ohio for numerous implantable parts that might possibly be used during such an operation, as well as trays containing the appropriate surgical instruments. It is not uncommon for the firm to send several hundred items for a single operation, with only a few actually implanted and the rest returned to one of Zimmer Ohio’s two warehouse facilities, located in Columbus and Hudson.
There is no room for shipment errors by Zimmer Ohio when it comes to implants or tools used in surgery, says John Reese, the inventory operations manager at Zimmer Ohio’s Columbus warehouse. For that reason, the company employs inventory specialists who spend hours every day checking over each order to ensure the correct inventory is sent in each shipment. The items are checked four times before being transported to a hospital.
The aluminum surgical tool trays (which measure 22 inches by 10 inches and range from one to eight inches tall) can be the most time-consuming, as there are often several hundred very small items—for example, a 2.5-millimeter (0.09-inch) drill bit—packed within them, all of which must be accounted for. The value of a single tray and its contents can range from $1,000 to more than $20,000, Reese says, so another concern is ensuring that the trays do not get lost. Following a surgery’s completion, the hospital sterilizes the entire tray and all of the tools it holds, then seals the tray in plastic film and places it on a shelf corresponding with its particular provider, such as Zimmer Ohio, for the driver to pick up. If the tray is inadvertently placed on the wrong shelf, it can be time-consuming to locate it. To identify which tray it is, Zimmer Ohio or the hospital may need to unwrap the tray and examine its contents, after which re-sterilization and rewrapping of the tray would then be necessary.
For several years, Zimmer Ohio had sought an automated solution that would reduce the time it spent ensuring each shipment was in order. But when the firm investigated RFID several years ago, Reese says, tag cost made the implementation seem too expensive. In September 2009, however, the company began working with RFID Enabled Solutions (RES), based in Dublin, Ohio.
Zimmer and RES representatives agreed that a typical tunnel reader—which would require that tagged objects be placed on a conveyor, one at a time, to pass through an RFID interrogator’s read field—would be inconvenient since it would require changing the existing packing process. While filling an order, staff members use a pick list to gather items, placing them on a metal cart that is wheeled around the warehouse. RES then developed an RFID tunnel that would accommodate the entire metal cart, with all of the ordered items on it, reading every tag on the cart simultaneously, says Neco Can, RES’ cofounder.
The tunnel includes an ultrahigh-frequency (UHF) EPC Gen 2 RFID reader and antennas. When Zimmer put the tunnel through a series of tests, Reese says, the tags attached to the implantable devices and trays were read with 100 percent accuracy every time. Tagging each individual tool in the instrument tray was feasible, however, because many tools are too small to tag, or would not function properly if tags were attached to them. Therefore, Zimmer and RES came up with a unique solution: The companies installed a scale with a built-in RFID interrogator next to the tunnel reader. Prior to sending a specific surgical tray to a hospital for the first time, the staff at Zimmer Ohio will commission that tray—meaning they check every item within it, record what is there, take pictures of the tools it contains, and then weigh it. The scales are so sensitive that later on, when a tray returns from the hospital, Zimmer Ohio can weigh it and determine if any tools are missing or incorrect.
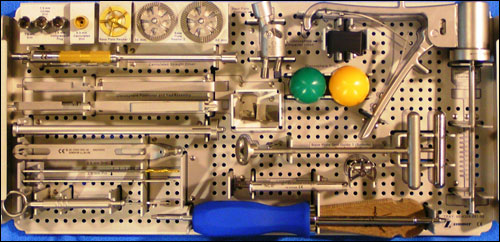
Once the system goes live—which is slated to take place in June 2010 at the Columbus warehouse, and in August at the Hudson location—all individual implantable items, as well as the trays filled with surgical tools, will be tagged with adhesive UHF EPC Gen 2 labels. Each label’s passive RFID inlay is encoded with a unique ID number, and that same number is printed in bar-code form on the front of the label. As each new item is tagged, workers can simply utilize a bar-code reader, installed at a desktop computer, to log that asset into RES’ AIMS RFID-enabled inventory- and order-management software system, running on Zimmer Ohio’s server, which receives and interprets data from the surgical tray scale and interrogators before forwarding that information to Zimmer Ohio’s existing inventory system.
When an order comes in from a hospital, a staff member will access the AIMS software to retrieve information about that order, and print a pick list of all items and tool-laden trays to be packed. The worker will pull the implantable items and trays from the shelf and place them on the metal cart. Once the order is fully picked, the worker will take the cart to a scale with a touch screen connected to it, and weigh each tray. An RFID reader under the scale captures the unique ID number on the tray’s RFID label, and AIMS software then displays a list describing each tool that should be in the tray, along with the loaded tray’s weight and a picture of each item that should be on that tray.
The scale, meanwhile, will determine the tray’s weight, and that data, along with the ID number encoded to the tray’s RFID tag, will be transmitted to the software via a cabled connection to a PC, and compared with the information already stored in the software regarding that tray. If the tray is not the expected weight (that is, if it is either heavier or lighter), the system will show an alert on the screen. Otherwise, it will approve the tray and displays the word “Pass.” The on-screen photo of the tray’s contents will act as a confirmation to ensure the proper items are in the tray.
The worker will roll the cart, loaded with the trays and implantable devices, into the RFID tunnel, which is a 7-foot-tall box, then shut its doors to reduce the chance of reading the tags of items located outside the tunnel. Once the interrogator captures all of the ID numbers, the AIMS software will compare the numbers with those on the pick list, in a matter of several seconds. If the order contains any mistakes, the system will display an alert. Otherwise, the AIMS will approve the order and inform the Zimmer inventory software that order has been completed and is ready for shipping.
When the trays and unused orthopedic implants are brought back to the warehouse from hospitals—typically picked up by a Zimmer Ohio vehicle—they will be put into the tunnel, and the AIMS software will update Zimmer Ohio’s software regarding which items have been returned. Those not returned can then be invoiced. The trays will also be reweighed, and that weight will again be compared against the specific weight expected for that tray, in order to verify that it is complete.
There were several challenges that RES faced in developing the system, says Kurt Domini, an RES partner and the firm’s director of sales and marketing. The company designed the tunnel reader to accommodate the metal trays, but also needed to ensure that the tags being used could withstand the rigors of sterilization at the hospitals, with exposure to temperatures of 375 degrees Fahrenheit (191 degrees Celsius) for three hours.
RES also provided the company with two handheld RFID readers, to use for conducting full inventories of implantable items and trays of tools in its warehouses. A full inventory, Reese says, currently takes 40 man-hours to complete, using manual checking or bar codes. With the new RFID system, he expects the inventory process to take approximately 20 minutes. What’s more, with the use of RFID, Zimmer Ohio’s staff no longer needs to check an order’s items four times prior to its being shipped to a hospital.
Zimmer Inc. has several dozen other distributors in the United States, Reese notes, and it may recommend that those companies install an RFID system like this one, though no specific plans have yet been made. He predicts that Zimmer Ohio will recoup its investment in less than a year.