Qew Orchards, the largest apricot producer in the southern hemisphere, is using radio frequency identification to increase efficiency and properly compensate its workers.
Qew’s trees are located on separate properties in Tasmania, Australia, and the company employs up to 150 itinerant fruit pickers each year during the harvest season. The employees are paid based on the number of crates they fill, to provide them with incentive to generate the maximum possible output.
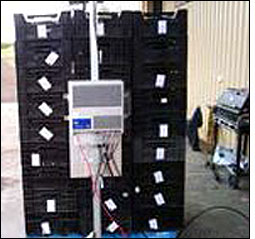
Previously, each fruit picker was given wax-coated paper picker tags, perforated into three parts, at the start of each day. Once a worker had filled a crate, he would attach one of the paper tags to it, then pull off one of the perforated pieces for his own record. When a tractor arrived to collect the crates, staff members would rip off the middle tag, which would be sent to the office to be counted that evening. The crates would then be taken to a refrigerated storage unit, and if any were incorrectly filled, or contained poor fruit, the company would be able to refer to the attached paper tag to identify the picker who had handled that crate.
According to Alistair Chong, a spokesperson for Qew Orchards, the paper tags were not reusable, and the system was time-consuming and inefficient. Radio frequency identification, he says, was the logical alternative. Bar-coded stickers had been trialed, but they faded in the sun by the time they were taken back to the shed and were stored in a cooler overnight, thus preventing the company from knowing who had picked a particular crate.
“RFID also seemed the most appropriate choice because of the large volume of transactions that take place in such a short space of time,” Chong states. “RFID would save us time, labor and aggravation, as we would no longer have to sit and count picker tags at the end of every night.”
Qew Orchards considered a number of RFID suppliers before eventually deciding on Ramp RFID Solutions, an Australian RFID software developer and systems integrator. The two companies tested the technology ahead of the rollout—specifically, the RFID tags’ performance, given the density and water content of apricots.
“One of the biggest challenges was to find RFID technology that would work through water and the density of the fruit,” Chong says. “The point of testing was to determine at which point that tag could be best read. Another challenge was the distance we required the system to run, as we needed to assign the tags in a separate place to the actual reading of the tags.”
Each picker is assigned a credit card-sized plastic ID card, as well as 100 cards for identifying crates. The picker and crate cards each contain an ultrahigh-frequency (UHF) EPC Gen 2 passive RFID inlay. A Convergence Systems Limited (CSL) CS461 UHF EPC Gen 2 four-port fixed reader, fitted with CS778 near-field antennas, assign lots of 100 tags per worker in seconds. The antennas are specially designed for tagging items high in water content.
Since there is a maximum of 150 workers at any particular time, there are 150 RFID picker cards, each marked from 1 to 150. Every day, using the OnRamp Freeway system, Qew Orchards places a picker card on the near-field antenna, and then assigns 100 RFID crate tags to that worker’s card. On the interface, the system shows the picker’s card number, as well as the number of tags assigned to that person. The assigner then confirms that they’ve been given to that employee, and the 100 tags are then linked to the picker card’s unique ID number.
When a picker fills a crate, he slides one of his assigned crate cards into a plastic sleeve riveted to that crate. Filled crates are then stacked on pallets, and are moved back to the weigh station by forklift. A portal measuring 4 meters high by 2 meters wide (13 feet by 6.6 feet) has been set up near the weigh station with four far-field antennas connected to the same CS461 reader, which is connected to a PC via Ethernet. Once the infrared sensors are triggered in the portal, the interrogator begins to read all of the RFID cards on the crates. OnRamp Access software then shows the number of cards read, which are linked to individual employees, and the user clicks on the “confirm” button to finalize the count.
All of the information collected is written to an SQL Express database. Qew Orchards’ administration staff can then generate a report showing the number of crate cards issued to each picker, as well as the number of crates filled with each picker’s cards, via the OnRamp Navigator browser application. The report can be printed or exported to the payroll system as an Excel document, or viewed with a local network or over the Internet.
Navigator is currently used for running the report indicating how many crates a worker picked during a particular day or week, though the system has been expanded to allow the uploading of information into the database and integration into a Toshiba Tec B-SX4 RFID printer for label printing with inventory- and asset-tracking reports.
Chong says he spent one day with sales and technical staff members from Ramp RFID Solutions as the system was installed in December 2008. The full deployment, and his training, took just two weeks. “I then trained the rest of the staff over time, as the season started and progressed,” he adds, “so we were testing on the actual product.”
According to Chong, the biggest benefit has been a reduction in time and labor spent counting the picker tags at the end of each night. “RFID allows us to allocate the number of crates picked per picker in a given day, and then pay them accordingly,” he states. “But it also allows us to work out exactly how much fruit we have to pack in the next given fruit-packing cycle.”
This has enabled the company to better allocate employees, as it now knows the precise quantity of apricots that need to be packed on any particular day.
Chong says he is not yet sure if Qew Orchards will increase its use of RFID down the line, as there are currently no plans to expand the orchard beyond its existing three properties. “However,” he notes, “that does not mean that we will not need to increase the size of the RFID deployment if the harvest gets larger in the future.”