The Bavarian State Mint is using RFID to track the production of euro coins from the time unstamped blanks arrive until the moment finished coins are shipped to banks. The system provides the mint with greater security, enabling it to control production more effectively than in the past. Before the system was implemented in 2005, the mint used paper routing slips to guide containers through production.
The system utilizes high-frequency (HF) RFID tags made with NXP Semiconductors‘ Icode SLI passive 13.56 MHz RFID chips, which comply with the ISO 15693 standard. The transponders are embedded in a plastic sheath resembling a luggage tag, attached to containers using a plastic cable strap. Schreiner LogiData and smart-Tec provided the tags and coverings for the deployment.
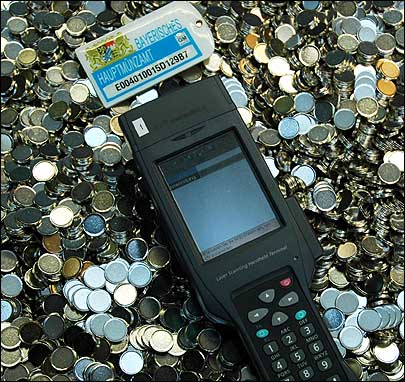
The tags are applied to about a dozen types and sizes of containers able to hold up to 50,000 coins apiece during production. Containers vary from 20 by 20 centimeters (7.9 by 7.9 inches) in width and length to 1 by 1 meter (3.3 by 3.3 feet). Production steps include stamping the coins, assembling those made of two separate materials—such as coins with €1 or €2 denominations—and performing quality checks. During the entire process, each container goes through approximately 20 interrogations.
Before a finished batch is loaded onto a truck for delivery to banks, the tags are removed for reuse. About 3,000 tags are in circulation, 2,000 of which are in use at any given time, says Michel Dorochevsky, chief technical officer of Softcon IT-Service, the Munich-based software developer and integrator that designed and deployed the system.
The coin blanks arrive in suppliers’ containers made of wood, metal or plastic. A worker transfers the blanks to one of the mint’s containers, using a Casio DTX 10 handheld computer with a standard RFID module to read the container’s RFID tag, and to key in basic information such as the supplier’s name and the ID number printed on the container. This information is transmitted to a database via wireless LAN, along with the tag’s unique ID—the only data stored on the tag.
Each container is subject to occasional quality-control checks. When instructed via the handheld to carry out such a test, employees first interrogate the tag on the container of coin blanks to be tested, then read a tag inside a thick plastic bag used to transport a sample of blanks. Next, they take out a scoop of coin blanks and place them into the plastic bag. The database is then updated with the blanks’ new location, and the system confirms that the transfer has been properly carried out.
After quality tests are completed at the lab, a worker uses a desktop interrogator to read the bag’s tag, which informs the system that the bag of blanks is headed back into production. The results of each test are linked to the bag’s ID number, allowing operators to track the quality of different batches. Upon return to the production line, a worker must once again scan the originating receptacle—in this instance, the bag—as well as the destination container. If the system notifies the user that a proper match has been made, the employee can dump the coin blanks back into the container. This process helps keep batches from getting mixed up, Dorochevsky explains.
Workers utilize forklifts to raise containers and dump their contents into the machines that stamp and process the coins. Before any blanks or coins are poured through the flap at the bottom of the container, the staff must first interrogate the container’s tag. Coins are not produced in assembly-line style, but rather through manual movement from one machine to another. Finished coins are packaged in paper rolls, loaded into a container, weighed and moved to a safe. The final reading of a container’s tag comes when the coins are loaded into special delivery containers and onto trucks. At this point, the RFID tag is snipped off the container.
Softcon IT-Service won the contract to develop and implement the system following a public tender. The system is based on the company’s LogIDSoft platform, which serves as middleware and production-control software. The project was rolled out in two phases, beginning in 2006. The first phase involved the interrogation of containers filled with blanks when they were received, along with the quality-control steps. In the second phase, Softcon IT-Service expanded the RFID application throughout production. According to Dorochevsky, the main obstacles during the project were setting up the wireless LAN network in the metallic industrial environment, and training workers on the system.
Presently, Dorochevsky is working to expand the system to reduce the mint’s paperwork. The goal is to provide authorized users access to a Web-based portal where they can determine the production location of specific batches of coins and download relevant documents, such as the results of quality checks or electronic routing slips. This process is now being defined, with plans to implement it by the beginning of 2009.
The German Federal Ministry of Finance, for instance, often needs to know the exact status of production, and may need to retrace production steps to learn what happened when, and where. In addition, Dorochevsky says, the mint foresees expanding the use of RFID to its supplier network so each container of unstamped coins, for example, will arrive already bearing an RFID tag.
The mint spent about €200,000 ($295,465) on the system, Dorochevsky says, adding that users consider the main benefits to be increased security and transparency of the production process. The production overview enables the mint to customize production steps based on needs. If demand fluctuates, for instance, it can slow down or speed up batches being manufactured. What’s more, by knowing how many coins will be finished at the end of a particular production cycle, managers can more easily calculate whether the mint should warm up or shut down additional machines to create an even production flow.
“RFID made this level of control possible,” Dorochevsky says. The mint has not calculated an ROI, given the qualitative nature of the application’s benefits.