For China International Marine Containers (CIMC), a leading worldwide supplier of containers to the shipping industry, tracking its products is no small task. Each year, the $4 billion company manufactures more than 1 million dry-freight containers for customers across the globe. It operates 20 factories and stores the containers at 40 different yards throughout China before delivering them to clients.
For years, CIMC’s inventory-tracking process was very labor-intensive. Workers used a mix of optical character recognition (OCR) technology, paper, pens, walkie-talkies and even binoculars in the container yards, to determine its products’ whereabouts. This system caused inefficiencies and waste—in fact, the company often did not know the exact location of its containers, and in some cases, it lost them or delivered the wrong ones to its customers. In an effort to cut costs and improve operations, CIMC launched an RFID pilot project last year to track containers from the factory to the storage yard.
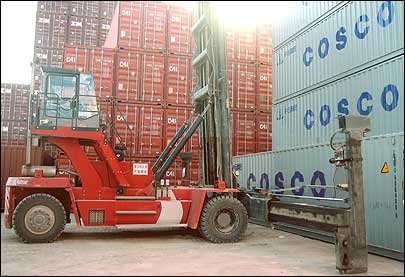
CIMC’s goals were “to speed up the efficiency of global supply-chain management and reduce the cost of asset management,” says Shouqin Zhou, director of CIMC’s Smart and Security Research Center. Aware of the potential benefits RFID offered, Zhou was convinced the technology could help lower costs and provide better reliability than OCR.
CIMC worked with Laudis Systems, a software firm in Edison, N.J., specializing in RFID systems, to devise a real-time locating system (RTLS) pilot for one container yard in Shenzhen, China. CIMC opted for a low-risk approach, integrating RFID into its existing shipping and storage processes so the technology could be tested without disrupting operations. While many RTLSs usually involve active tags, CIMC’s system uses passive tags because the price of active tags is prohibitive, the company says. The way the pilot was designed, the passive tags can achieve benefits on par with an active system at a fraction of the price, says Yuhong Zhu, chief technology officer of Laudis Systems, who was involved in the CIMC pilot. The passive tags cost $6 to $7 each, compared to $50 per active tag.
Since the pilot was launched in early 2005, 1,500 containers have been equipped with the passive tags for location-tracking purposes. Much of the work of accounting for the containers has been automated, with interrogators installed at the factory and storage-yard gates and on the forklifts used in the storage yard. Location information is transmitted in real time from a code division multiple access (CDMA) network to CIMC’s existing yard-management system. This allows CIMC to know where its containers are at all times. “It’s a major labor-saving tool for the company,” says Frank Ritota, Laudis’ CEO.
That’s a far cry from CIMC’s traditional method of tracking containers. Information about whether specific containers had left the factory grounds and were en route to the storage yard was hard to come by. The company’s products are all made-to-order, and while they may look similar, each has its own unique features and specific weights, depending on customer requirements. As such, keeping track of each one is critical. Before the RFID pilot, when the containers were ready for transportation from the factory to the storage yard, truck drivers had to check out at the gate with piles of paperwork. This created backups, with drivers forced to wait in line until their papers were processed.
Once the containers were unloaded at the storage yard, things weren’t any easier. For starters, the yard where the pilot was conducted spans more than 37 acres and can hold up to 30,000 containers. “It’s like a little city,” Ritota says. Forklift operators had to write down the location of the containers, which increased the likelihood of errors and slowed down the availability of location information.
Without up-to-the-minute information pinpointing containers’ precise locations, finding the right one was akin to picking out a particular grain of sand in the desert. When it came time to move a container for shipping, workers had to search acres of vertically stacked and similar-looking containers. At times, they resorted to using binoculars to read the identification number on the containers, some stacked eight or nine stories high.
Under the pilot project, CIMC and Laudis collaborated to develop a real-time asset-tracking and management system for the storage yard. The system provides three-dimensional mapping and task-management features, and utilizes two software components: Mobile Locator, which runs on a vehicle-mounted, mobile computer, determining location and collecting the asset-tracking data; and Position Server, which uses XML-based APIs to provide an interface between the mobile communication systems and CIMC’s existing yard-management system. Position Server can operate as a standalone server or as an add-on to existing systems. It includes a business-rules processor allowing customers to define their own rules or parameters for optimizing operations and workflow.
Using this information, the system can create alerts to correct problems or define the best routes and schedules to move products. At CIMC, for example, alerts are issued on the mobile computer if a forklift or crane operator picks the wrong container. Sensors connected to the vehicle-mounted computers via serial port also help track location.
Laudis’ software works with hardware from various RFID vendors, including Symbol, ThingMagic and several Chinese companies, and with mobile computers from a variety of vendors. CIMC says it deployed ISO 18000 6B-based passive tags operating in the 902 to 928 MHz range. Both the tags and interrogators were produced by a Chinese vendor, which CIMC declined to name.
At the factory, passive tags are attached to the containers by magnetic strip as they come off the assembly line. The tags incorporate a container’s complete identification information, including its weight, the date and time of manufacture and the intended customer. All of that information is written to the company’s central database. RFID tags are mounted on the windshields of the trucks hauling the containers from the factory to the storage yard. RFID interrogators at the factory gates then read the tags on both the trucks and the containers as they pass through, sending information about the movement to the central database.
When the trucks reach the container yard, interrogators scan both the trailer and the container tags, making check-in automatic. Based on the check-in data, travel time is calculated for billing purposes. The yard-management system, which CIMC developed, sends instructions to workers, via the CDMA network, regarding where to unload the containers. The forklifts that unload and stack the containers are equipped with touch-screen computers running Mobile Locator and an RFID interrogator, while the mobile computer and the RFID interrogator transmit data via the wireless network.
When a container reaches its assigned location, its RFID tag appears on the forklift’s mounted computer screen, along with the corresponding container identification information and a three-dimensional map of the yard. The forklift operator uses the touch screen to input the location of the container into the yard-management system, which is updated in real time. When it’s time to ship a container from the storage yard, the system sends work orders to the crane via wireless messages, telling them to move the containers to a staging area.
The computer on the forklift displays the location on three-dimensional, color-coded mapping software with zoom-in capabilities. Using such a map, forklift operators can see where the containers are stored, even when stacked one on top of another. Workers can also search the system for a particular container by entering its identification number onto the touch screen.
The trailers and containers are all equipped with RFID tags, which interrogators at the container-yard gate read. The system then confirms the customer and delivery information and updates the central yard-management database accordingly. With the discharge process automated, checkout time is significantly reduced, CIMC reports. The system then removes the tags at the storage yard exit gate before releasing the containers for customer delivery.
According to CIMC’s Zhou, the company spent more than $128,000 on the pilot projectand is saving about $126,000 annually as a result of the streamlined operations. The savings came about for a number of reasons: The number of lost containers at the Shenzhen yard has been reduced from four to zero. Delivery mix-ups have been eliminated, the leasing of forklifts at the storage yard—necessary at busy times to augment the company’s existing fleet—has been sharply cut down and workflow has been sped up.
Clearly, there is much need for real-time inventory tracking in the container industry. Approximately 17 million containers are currently in use across the globe, while annual production is in the low millions, according to ABI Research, a market research and consulting firm in Oyster Bay, N.Y. Robert Foppiani, a research analyst with ABI, says using RFID can help CIMC make operations more efficient. “It’s a step in the right direction,” he says.
The benefits of RTLS are expected to attract plenty of interest from companies looking to manage their inventory and assets better. Over the next 10 years, the RTLS market is anticipated to take off as equipment prices become more affordable and the technology becomes more portable. According to IDTechEx, a research and consulting business that focuses on RFID, the RTLS market will jump from $30 million in 2005 to $2.71 billion in 2016.
Laudis’ Ritota maintains that the benefits of real-time asset tracking go beyond better inventory visibility and management; he says they also include tighter quality control, theft prevention, improved customer service and safer working conditions at the storage yard since workers no longer spend hours using heavy equipment or walking around searching for containers.
Based on the success of the pilot project, CIMC wants to expand the use of RFID. To that end, the firm is eyeing another container yard in Shenzhen, even bigger than the pilot site, as a likely spot. Zhou says: “It can help CIMC save labor and costs.”