Eugene, Ore.-based ADASA first entered the RFID marketplace in 2004 to create a system of recovering and possibly reusing passive RFID tags, in order to divert them from landfills and extend their usefulness. ADASA has now introduced another new concept to the marketplace: a wearable RFID encoder (interrogator) called the PAD3500. Comprised of a cartridge that holds a roll of up to 500 1-by-4-inch RFID inlays, the PAD3500 also comes with a small, battery-powered RFID interrogator made by Boulder, Colo., RFID systems developer SkyeTek.
“The PAD3500 was developed in order to be used with whatever preexisting systems end users have in place,” says Clarke McAllister, ADASA’s CEO. A Fortune 50 company is in the early stages of testing the device, he explains, to see how it might be used to integrate the tagging of cases into its different order-picking scenarios.
According to ADASA, the device is designed to enable companies to integrate RFID tagging into any product-picking system they use. This avoids the need to divert goods to a separate tagging station, where (if already palletized) they would need to be depalletized, tagged and repalletized.
To comply with RFID mandates from their customers, many suppliers have installed RFID printer-encoders to produce shipping labels with embedded RFID inlays and printed bar codes, encoding them with shipping and order information. The ADASA encoder would be used in place of these devices, though end users would continue to use non-RFID label printers to generate the shipping labels needed to identify the cases through bar coding and human-readable data.
McAllister says that during the ongoing testing, the PAD3500 will be used with a number of order-picking processes, including voice-to-pick, in which the order picker receives computer-generated instructions transmitted to a headset, or directions from a mobile computer mounted on a forklift or other material-handling vehicle.
Using a built-in Wi-Fi link, the PAD3500 is designed to receive encoding commands from the user’s RFID middleware or device management software, which would interface with the user’s warehouse management software. The EPC encoded to each label would be associated with the SKU of the goods being picked, as well as the order information.
McAllister says using the PAD3500 might result in fewer damaged RFID inlays. RFID printer-encoders, he claims, generate enough electrostatic discharge during the printing process to damage a significant number of inlays. McAllister notes that an inlay can also be damaged when a label is peeled off a roll of tags while being dispensed.Exactly how many fewer nonfunctioning inlays the PAD3500 will produce compared with printer-encoders won’t be known until analysis of the test results is complete, later this year.
Integrated into the PAD3500 is a sensor, triggered when the picker places his finger in front of it, which advances the roll of tags inside the cartridge. The device pushes the inlay off the roll, adhesive side facing outward, so that the picker need only tap the adhesive side with a finger to remove the inlay. Before the device pushes the inlay off the roll, however, the SkyeTek interrogator verifies that the inlay has been properly encoded and is still functioning. If the inlay is damaged, the PAD3500 jumps to the next one without the label with the nonfunctioning inlay.
Once the cartridge dispenses its last inlay, an LED on the PAD3500 casing—which includes a belt hook so the device can be positioned at the picker’s waist—indicates the cartridge needs to be replaced. McAllister notes that the used roll, still containing the nonfunctioning inlays, can then be returned to the inlay supplier.
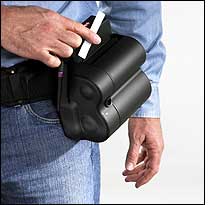
The PAD3500 is set to be available in production quantities later this year, after the trial has finished and any system modifications have been incorporated to improve performance, based on the test results. McAllister says ADASA expects to price the PAD3500 competitively with RFID printer-encoders.
Thus far, ADASA has worked with inlay maker UPM Raflatac to supply the rolls of inlays needed for the sample PAD3500 being used in the test. These will be UPM Raflatac’s UHF EPC Gen 2 inlays with the aluminum OneTenna antenna (see Rafsec Set to Produce Gen 2 Inlays).
McAllister says ADASA recommends the use of tags with aluminum antennas because they are environmentally friendlier and easier to recycle than etched copper or printed silver-ink antennas. He adds that ADASA has completed the design phase of its tag-recycling process, intended to help capture and recommission passive RFID tags (see RFID Goes Green). However, the company is waiting for the volume of tags in the waste stream to increase to the critical mass required to make the service commercially viable.