I’m a fan of the New York Giants, one of two professional American football teams that represent the New York area. On Sunday, Sept. 22, the Giants’ coach replaced long-time quarterback Eli Manning with a rookie, Daniel Jones, who had been drafted sixth overall in the offseason. Jones led the team to a stirring 32-31 win over the Tampa Bay Buccaneers.
Excited about our new star, I went online to order an official Daniel Jones jersey. I was fairly surprised, however, when I received my order confirmation and discovered that I would not receive the jersey (which cost nearly $90 with a special discount) for a month. Whenever I order from Amazon, products often arrive the next day. A month?
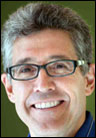
OK, so Daniel Jones jerseys probably were not in stock since he was a backup until Sept. 22. A month to print and ship a jersey still seems like a lot, but whatever. Two weeks went by and I received an email saying that my order had been delayed. It said: “Unfortunately at this time, we have not received a shipment update and are working diligently with our warehouse to obtain more information. We’re extremely sorry for any frustration this may cause and will notify you immediately regarding any shipping updates.”
They had no idea when my order might arrive. Perhaps after the season ended. Daniel Jones won his next game, but then lost two games. I decided to simply cancel my order.
I understand that running a supply chain is very difficult. I also get that sports-related goods are extremely prone to spikes in demand. When Odell Beckham Jr. was traded from the Giants to the Browns, there was a complete falloff in demand for OBJ Giants jerseys and a big spike in demand for his Browns jersey.
But in the current retail environment, fans and most young consumers want—frankly, expect—next-day service, and they don’t care about a retailer’s supply chain issues. That means companies need to be using RFID and other technologies to gain inventory visibility. Artificial intelligent would help to provide fast alerts: “OBJ was just traded to the Browns. Start making OBJ Browns jerseys.”
Without inventory visibility, companies don’t know what they have in stock or in the pipeline, and they cannot fulfill orders quickly and effectively. Given that many products are made overseas, the long supply chain makes delays interminable, which makes customers unhappy.
RFID can’t fix a broken supply chain, but it can help companies know what they have and where it is located, and it can enable them to be more responsive to their customers. Without the technology, a company risks losing not only orders, but customers. I probably will not buy another jersey from that online retailer again. A month is too long to wait—and who knows, my favorite player could turn out to be a bust or end up traded.
Mark Roberti is the founder and editor of RFID Journal.