The Tokyo Baycourt Club, a resort with four restaurants, each served by a stocked wine cellar, has improved its wine inventory accuracy and reduced stock-counting time by about 88 percent, thanks to an RFID-based inventory-management system. The solution, provided by SATO Corp., has helped the resort to digitize its inventory of thousands of bottles of wine, and to bring the inventory-counting process down to a matter of hours.
The Tokyo Baycourt Club, owned and operated by Resorttrust, is located in Tokyo’s Odaiba area. It features 292 guest rooms and four restaurants, serving Japanese, French, Italian and Chinese cuisines. The resort also features a bar, a lounge, a convention hall and room service, all of which serve wine from the resort’s wine cellar and refrigerators. Altogether, the resort manages an inventory of approximately 5,000 bottles of wine. Managing the wine was a laborious process that involved visually counting and checking inventory levels against paper forms. Finding a particular bottle of wine when a guest requested it could be a time-consuming process.
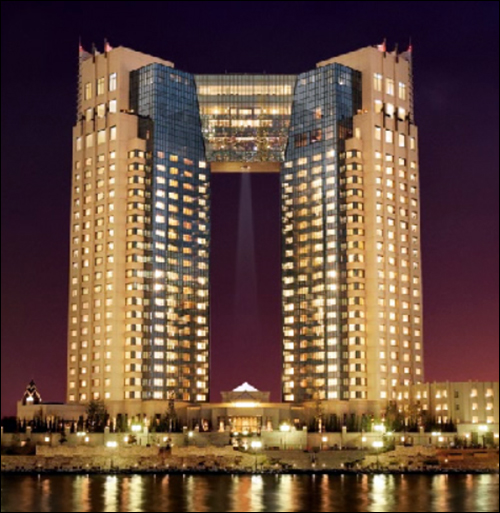
To reduce labor costs and the potential for errors, the resort began seeking a technology-based solution. “I wanted to reduce the workload with the goal of utilizing limited human resources for more productive operations,” says Katsuhiko Aihara, the Tokyo Baycourt Club’s beverages head. Ultimately, he says, his goal was to improve service and sales.
After some investigation, Aihara says, the resort’s management decided that RFID “was the best way to comprehensively solve our issues.” It found that SATO was the only solution provider able to deliver a complete solution, including RFID tags, readers and integrated software.
The resort had some requirements when it came to how the RFID solution could be deployed, however. Tags could not be permanently attached to the bottles—since a label affixed to each bottle, cork or lid could affect the wine’s appearance or quality—and the tags needed to be readable when stacked in the cellar or in coolers. The resort began working with SATO to come up with an RFID-based solution in October 2016, then began testing the technology in November of last year. Following the pilot, the system was taken live in January 2018.
The solution posed several unique technical challenge for SATO, one of which was the reliability of interrogating tags on wine bottles. “Liquids and metals greatly affect read rates for UHF RFID tags,” explains Shinya Nitta, SATO Material’s president. Additionally, the metal-sealing foil on wine corks poses another potential RF transmission block. “The effect is amplified,” he notes, “with wines closely packing into a wine cellar.”
To overcome these challenges, SATO visited the site to view the resort’s operations, including how the bottles were stored and how employees would typically hold the reader when conducting inventory counts. SATO eventually opted to develop a custom tag. “We devised a technology to counter the effect of the liquid and sealing foil that could be attached to the [bottles] with a metallic jig,” Nitta states. After experimenting with tag placement, the company was able to achieve stable read rates.
The reusable, form-fitting tag can be attached to a bottle’s neck without affecting the quality of the wine itself in any way. SATO also provided eight Denso Wave BHT-1281QULWB-CE RFID Handy Terminals (handheld readers) with CU-1233 cradles, along with two Denso Wave UR22-MR-01 RFID Table Readers. It also supposed its own management software, integrated in the resort’s purchasing software, says Hideyo Koide, SATO’s logistics sales senior leader for Nagoya, Japan.
When wine is received at the resort, it is first inspected to ensure there are no problems, such as damage to the bottle or cork. A tag is then attached and the unique ID number on that tag is captured by the SATO software, which links that data to purchasing information and forwards it to the in-house purchasing software. The tagging of bottles requires about 10 minutes for each new case of 12 bottles. Initially, the resort tagged about 3,200 bottles of its existing inventory.
Wine bottles are next placed into storage in a wine cellar or cooler. Resort personnel then use the Handy Readers to interrogate the tags for stock-taking purposes, both in the wine cellar and in the refrigerator. The Handy Readers can interrogate tags at a distance of up to 50 centimeters (20 inches). The software then compares the read data with inventory information, and any discrepancies are displayed on the reader, as well as on the software’s dashboard. That information is also forwarded to the purchasing software. The tags are read at the time of sale, in addition to when a bottle of wine is moved from one restaurant to another.
Since the system was deployed, it has reduced labor hours that employees previously spent counting inventory. For example, in one restaurant, two workers typically spent eight hours each to count all of the wine bottles, but since the RFID deployment, only a single staff member is required to read tags for two hours. That equates to an 88 percent reduction in labor time, the resort points out.
Moreover, the solution has enabled the resort to move toward a digitized wine list without the need for paper-based stock counts. This, Nitta explains, ensures transparency in inventory management, while also making stock-taking more efficient. “The synergy of the new operation and our custom RFID tag, with its stable read rates, resulted in labor savings and customer satisfaction,” Nitta states.
The system has also been found to decrease the risk of loss and theft, Aihara notes, due to the increased transparency of wine inventory. “Our time spent on stocktaking is only one eighth that of before, thanks to the RFID-tagged bottles,” he reports. “Since we do monthly stock-taking, this is a significant benefit for us.”
Next, the resort is looking into implementing the system at other Baycourt Club brand hotels. At the Tokyo Baycourt resort, the company is considering further leveraging data from the RFID-based inventory counts by providing wine inventory lists on tablet computers that employees could review in order to quickly identify whether a specific bottle is available, as well as where it is located. “I believe this could bring further improvements in customer satisfaction and employee productivity,” Aihara states.