A California Polytechnic State University (Cal Poly) research project has found that an RFID-enabled unmanned aerial vehicle (UAV), or drone, can read tags attached to steel drills or utility pipes at an accuracy rate of 95 to 100 percent. The year-long research project tested the technology at multiple sites, and in a variety of applications, as well as with several frequencies of RFID technology.
The tests all relied on a common feature, though: the RFID-enabled drone that swept over RFID tags in wide spaces. Solutions using RFID technology in drones for the oil and gas sector, or at other industrial companies, are now being developed and marketed by Process Expert, a company founded in 2007 by Tali Freed, a professor in Cal Poly’s Industrial and Manufacturing Engineering Department, the head of the research project and the director of the PolyGAIT-RFID Research and Development Center.
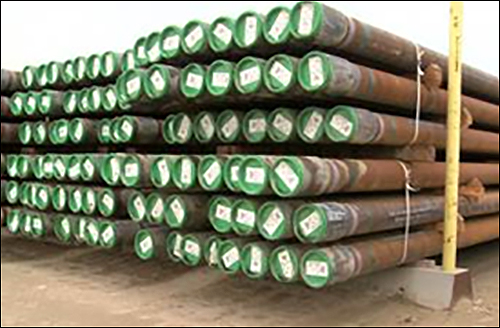
The research focused on capturing data from for the purpose of equipment inventory tracking in oilfields, but also included other utility-based equipment in storage yards or at construction sites. It also involved another use case, says Freed: tracking cattle grazing in an open field.
The project provided promising results when it comes to read rates, Freed says. Whether passive or active RFID tags are used, the group found that the read rate, adjusted according to the speed and height of an RFID-enabled drone, was high—typically, nearly all tags could be interrogated accurately. The scope of the project, which ran from March 2017 to March 2018, was to determine how effectively drones could be used to capture RFID tag reads for inventory or asset management.
Oilfields have a unique challenge when it comes to inventory management, based in part on the size of equipment, the way in which it is stacked, and the large expanse of some storage areas. Oilfields often require hundreds of thousands of tubulars (pieces of steel pipe used in drilling operations), which are stored across large fields, and counting them is a time-consuming process. However, manual counts have typically been the only tools available to site managers.
With RFID, items could be tracked as long as a reader remains within range of those tagged items. But in a large storage yard, a fixed reader deployment would not be realistic, and carrying a handheld reader throughout the storage yard regularly, Freed says—even with a vehicle—would still be time-consuming. The group speculated that this could open a possible use case for drones.
During the first experiment for oilfield equipment, the Cal Poly researchers attached 15-cent RFID tags from Avery Dennison, as well as Alien Technology‘s Squiggle tags, to each of several dozen pipe caps or three-eighth-inch foam insulators with a zip-tie. The experiment was carried out at Cal Poly’s experimental flight research test center, located near San Luis Obispo.
The team mounted a Process Expert RFID reader system on a DJI s900 Spreading Wings drone. The Process Expert reader includes an embedded ThingMagic Mercury 6e module and an MTI Wireless Edge reader antenna.
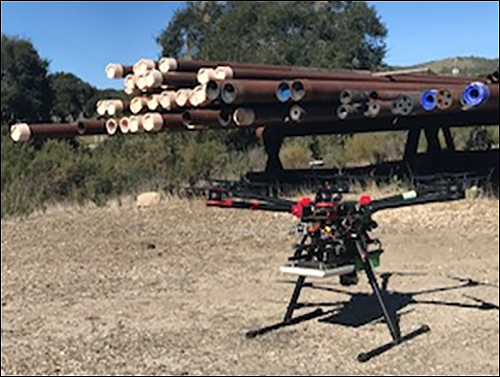
The group designed their own enclosure to house the system, which also included a host computer and a battery power source. The entire system weighed 7.3 pounds. They mounted tags on pipes, facing up, at six different heights and at two-foot intervals, ranging from ground level to 12 feet above the surface.
According to the university, the team found that the drone was typically able to read the passive UHF RFID tags at a distance of about 12 feet. At this distance, the group got close to achieving a 100 percent read rate, Freed says. The data was downloaded with a USB drive to Process Expert’s own software, hosted on a laptop. The tag IDs were linked to the drone’s GPS-based location, in order to assign a specific location to each tagged pipe.
The team conducted a second test at a Santa Maria Energy holding site for oil-drilling pipes. In this case, the tags were built onto insulation strips and were affixed directly to those pipes. With the drone hovering for about two minutes in each zone, it was able to read all tags at a distance of approximately 3 meters (9.8 feet).
During a third experiment, carried out at a Cal Poly pipe-storage area, the group set up a system to track hot water pipes. The tags were insulated and were attached directly to the pipes. With a two-minute hover time, at a 2.5-meter (8.2-foot) distance, they were able to read the tags at a 95 percent accuracy rate.
There were some limitations. Since the drone and reader system weighed about 12.1 pounds, the battery life was only around 15 minutes before recharging was required. That meant drones would need to be landed, and batteries would need to be replaced before the devices could return to the air. In a large storage area, Freed says, a dedicated person would be needed to “babysit” the drone, perhaps even using a truck to follow it and provide a landing point whenever battery replacement became necessary.
Because most oilfield sites may lack a Wi-Fi network, Freed explains, users would typically extract data from the drone following a flight using a USB flash drive. Passive RFID tracking is the most cost-effective solution, the group found, and the simplest to install, with tags that can be zip-tied or adhered directly to pipes. Tags with insulation and waterproofing would cost about $1 each, Freed estimates. The cost of a UAV with an RFID reader and software to manage the collected data would raise deployment costs to approximately $7,400, with an additional $1 for each tag.
The researchers sampled active RFID tags for use on cattle as well, where RFCode tags and readers were used. To simulate cattle in a field, tags were placed on the ground, or held by the researchers. The team then flew the drone over the cattle at varying heights. Next month, they will further test with tags attached to collars on cattle. They found that they could read the tags at about 40 to 50 feet above ground, but that if drones needed to decrease that elevation (based on terrain) to just a dozen feet or more above the animals, the tags could be read. Freed notes that drones don’t appear to disturb cattle.
For applications such as cattle tracking, Freed notes, “there are advantages to active RFID.” She adds that “you can store more data on a tag,” such as an animal’s health or immunization records, and sensors could be connected to the tags, such as pedometers to identify how much an animal has been moving.
Process Expert is just now releasing do-it-yourself RFID systems with readers that can be mounted easily to shelves, carts, forklifts, dock doors and portals, and data that can be retrieved as a Microsot Excel file via e-mail, Wi-Fi or a USB flash drive. It is now also offering the drone-enabled RFID tracking system.