SSI Schaefer Systems has released an automated system with a modular radio frequency identification-enabled pocket sorter that it is now selling to distribution centers worldwide. The system has already been installed at about 10 locations globally to manage the movements of millions of goods, the company reports.
The solution provides pocket sorter rails with RFID-tagged pocket or pouch carriers that enable it to automatically understand the exact location of each of hundreds of thousands of products that might be onsite at a large distribution center at any given time. The system can automatically deliver a particular item, via its pocket carrier, to the staging area, where goods can then be packed and shipped in order to fulfill a customer order.
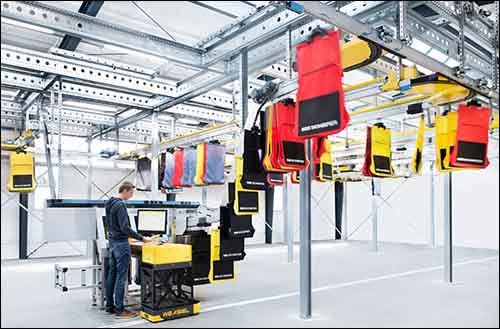
Traditionally, manual orders have required warehouse employees to collect a batch of orders, walk along the warehouse shelves, pick items for those orders, and then sort and pack them. But the demands on warehouses have been changing astronomically during the past decade or so, says Andy Williams, SSI Schaefer’s executive sales manager. Customers that previously processed 200,000 units daily might now manage 800,000 unit transfers a day in a similarly sized space. Warehouses can be up to one million square feet in size, but are not often larger than that. “As a result,” he says, “the way these systems work has changed quite a bit.”
Overhead conveyor systems allow the goods to be received and stored in a rail system so that they can be delivered directly to the area in which they are needed when orders are placed. However, Williams notes, without RFID, the identification of each item and the carrier pocket in which it hangs can be difficult to accomplish. Bar codes enable the identification of goods in such conveyor systems, but scanning them can be slower, and accuracy is not perfect. That matters, he adds, when products are shipped in large numbers. If only 99 percent of scans are accurate, that could still mean hundreds or thousands of potential errors each day. “Knowing with 100 percent accuracy exactly where everything is, is critical,” he says.
Therefore, SSI Schaefer is using UHF RFID technology with its SSI Carrier solution. The SSI Carrier consists of overhead rail modules that a warehouse can build into a single or multiple overhead conveyor systems, which are managed with SSI Schaefer software residing on its own back-end server, integrated with the firm’s management software or on the cloud. Each pocket or pouch is attached at a carrier point on the rail, and each carrier comes with an EPC UHF RFID tag. RFID readers are installed at key locations around the rail to identify the carrier within its vicinity. SSI Schaefer utilizes RFID readers from a variety of technology vendors, depending on a customer’s particular needs.
Typically, when goods are received at a warehouse, an operator opens the SSI Carrier software in which those items’ stock-keeping units (SKUs) are listed. The system instructs the operator to place each product or group of products into a hole, which accesses the pocket (also known as a pouch). These pockets are typically bags that average 600 millimeters by 400 millimeters (23.6 inches by 15.7 inches) and can hold approximately 6.6 pounds of products—which are, in many cases, apparel. A larger pocket sorter can accommodate goods weighing up to 22 pounds. In a typical large deployment, a warehouse may use the system with about 120,000 pockets, each of which has its own carrier RFID tag to be uniquely identified.
An infrared light curtain at the hole above the pocket enables a sensor to identify every time the light is interrupted by a product being placed into that pocket, and the software thereby identifies the SKU in the software. As the rail carrier and pocket pass away from the operator, they typically pass an RFID reader, which captures the carrier and pouch IDs and links them with the SKU of the item that the operator had placed into the hole. Then, as the goods move around the overhead system, their location on the rail is updated each time they pass a reader.
When an order is placed for a particular item, the software identifies its location in the rail system. It then forwards the specific carrier, based on its RFID number, to the shipping area. An RFID reader identifies when the proper pouch and carrier have arrived at that location so that an operator can take that product to fulfill the order.
This process requires only a fraction of the time required for manual labor, Williams says, and reduces the number of times that employees must handle the product, thereby decreasing costs and preventing the risk of errors. It also better enables the fast shipping services that retailers try to provide for customers, enabling them to fulfill a shipping order within a matter of minutes or hours rather than days.
Because some goods now arrive at warehouses with UHF RFID tags attached to them, some companies are already using (or are investigating how to use) those tags on the goods with the system as well. In that case, the RFID tag on a given product could be interrogated at the same time that the pocket carrier tag is read, automatically linking them and eliminating the need for the operator to associate a tag with the corresponding item’s SKU in the software.
The system reduces labor costs and enables fast shipping during most seasons, the company reports—at heavy activity times such as Black Friday, for example. What’s more, it can accommodate the increase without requiring the company to seek temporary help.