Meggitt Polymers & Composites (MPC)’s manufacturing plant in San Diego is taking the next step in a radio frequency identification and Internet of Things implementation that employs sensor and RFID data to gain visibility into the company’s work-in-progress (WIP) and the condition of the carbon-fiber composite materials it uses during manufacturing. The factory has spent more than a year using RFID to track the movements of one of the products it manufactures to the point of shipping. It now intends to expand its RFID deployment to monitor the out-time and aging of temperature-sensitive raw materials prior to their being heated and pressed during the component manufacturing process. The company initially used the technology to track the production of one type of aircraft component (known internally as a “value stream”), but it has now expanded to three, with more in the works, bringing the ultimate number closer to six.
The solution—involving ultrahigh-frequency (UHF) RFID technology, as well as wired and Wi-Fi-based wireless temperature and humidity sensors—is provided by IoT platform company GlobeRanger.
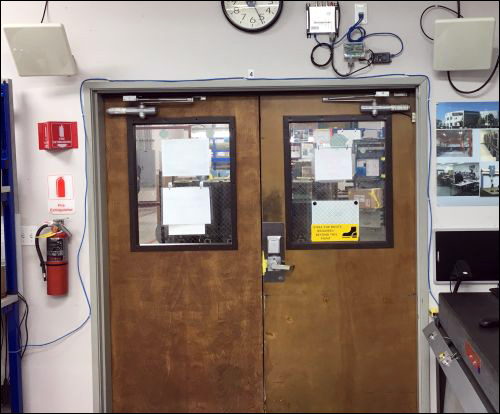
MPC’s San Diego plant makes carbon-fiber components for aircraft engines, including hot exhaust nozzles with aerodynamic features, in addition to missile airframe components. Altogether, it manufactures approximately 17 different products. The plant produces about 3,000 pieces for customers each month, says Daron Giles, the site’s management information system (MIS) manager, and each piece is high-value and labor-intensive. There are dozens of workstations that products pass, and each unique product has its own series of stations through which it must through before it is completed and shipped to a customer.
One of the plant’s customers, a manufacturer of engines for the F-35 Joint Strike Fighter (JSF) jet, had requested that MPC San Diego provide a weekly WIP report regarding its ordered components, in order to ensure that the delivery requirements would be met. The part counts required for this report were time-consuming to perform manually. MPC San Diego also sought a better sense of its work-in-progress, and a way to make the tracking of each part as it moved through the complex manufacturing process more automatic.
The company began conducting extensive research into RFID technology several years ago, Giles says, including reading RFID Journal articles and speaking with RFID vendors. From a list of Impinj‘s partner suppliers, it selected GlobeRanger. “I was attracted to the maturity of their offering,” he explains, “and they offered a largely commercial off-the-shelf system (COTS) with which they could build the application we required. My experience is that commercial off-the-shelf offerings give you the benefit of previous user learnings.” By opting for such a system, Giles notes, MPC San Diego would be able to save time and costs that would otherwise be required to build a custom solution from the ground up.
GlobeRanger began working to customize its iMotion system to meet MPC San Diego’s needs for the application, according to Mark Brown, GlobeRanger’s business-development director.
MPC San Diego operates two facilities that total 70,000 square feet, including clean rooms and machine shops. Raw materials, in the form of a carbon-fiber material (combined with resins and adhesives), must remain cold until the material is heated and molded. The material is cut off the roll, after which the resulting kit is placed into a ziplock bag. To identify that kit, a paper document, known as a “production traveler,” accompanies the kit as it moves from one station to the next. The kit moves through a series of workstations to be rough-trimmed, machined and inspected before a final product is shipped. Prior to the RFID installation, staff members wrote on the paper to record which employee performed which process, as well as when, and how long the material was out of the freezer.
For the RFID system, GlobeRanger and MPC San Diego installed 18 Impinj R420 readers (using power-over-Ethernet) and antennas, as a flat panel under workstations, above doors (as directional thresholds on both sides of the doors) and on ceilings, with an overhead antenna reading tags throughout an entire room. Readers were also installed at the entrances to two freezers, as well as at the press and heating machines, where components, placed inside molds, are formed. Each Impinj reader comes with four antenna ports, but in some cases, MPC San Diego has installed a multiplexer to enable as many as eight antennas to be used with a single reader.
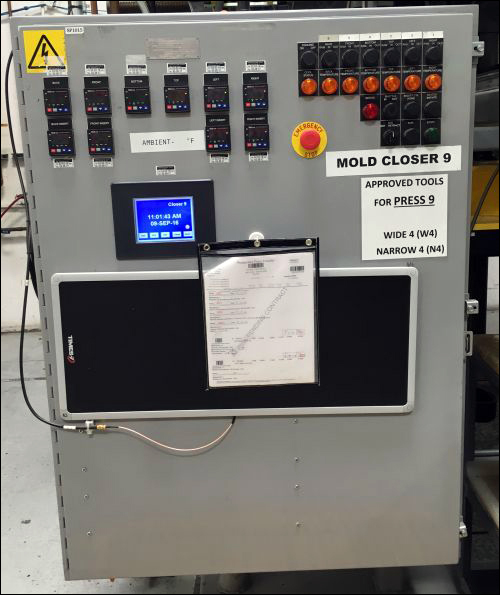
Readers automatically capture data as each kit moves through the workstations, freezers, presses and ovens. A magnet is used to fasten the paperwork to the exterior side of an oven or press, so that an RFID reader can capture its tag ID number.
After the composite material leaves the oven and press, it is moved to the remolding area, where the resulting component is removed from the mold and its surfaces are sanded down (hand-finished). The process results in a great deal of dust, Giles explains, so the reader and antennas were installed high up on a pole.
If, at any time during the process, a piece is found to have a quality problem, it is relocated to a “quality clinic,” where a material review board (MRB) team checks that item in and reviews it to assess the problem, identify the root cause and implement corrective actions. The RFID system tracks pieces as they move into and out of the MRB area, generating a dashboard view of the number of pieces in MRB, how long each part has remained with the board and each part’s age. “This helps us achieve our goal to disposition [resolve] all MRB [issues] within 30 days of discovery of the non-conformance,” Giles says.
At the shipping area, when an item is sent to a customer, the corresponding traveler paperwork is removed from the component and placed in a stationary box containing a built-in R420 reader. The reader captures the tag ID and forwards that information to the iMotion software, thereby updating the product’s status as shipped. The application employs GlobeRanger software to capture and interpret read data, which is then sent to MPC San Diego’s own enterprise resource planning (ERP) software.
Workers are also using Zebra Technologies handheld readers to conduct audits if a question arises about the data provided by the fixed readers. Additionally, in the event of a quality issue related to a specific aircraft component being manufactured, personnel can use a handheld reader, in search mode, that acts like a Geiger counter to quickly locate and quarantine that item. This can be accomplished within a matter of minutes, Giles says, whereas manually searching for an item in the past could take several days.
Since the system was installed in May 2015, Giles reports, it has saved at least one hour daily in labor required to fill out paperwork, thus freeing up employees to work on the products themselves. “We generate a ‘line of balance,’ report that the value-stream [product] manager receives every day,” he says. That data—which, according to Giles, includes the quantity of components currently in production, along with the stage of production for each individual component—can then be shared with the customer. After the system was first taken live, the company’s management wanted to confirm the results manually, so as to ensure that they were correct. Since then, the firm has gained confidence that the RFID-based data is accurate.
In the assembly area, a large screen displays data from the iMotion dashboard that indicates each part’s location and status: red, green or yellow, based on how long a particular part remains at a given location, as well as its in-process time and overall age.
The company expects to use the RFID-based location data to better resolve bottlenecks in the future, now that the information is revealing where work might be backing up.
Because of MPC San Diego’s success with the RFID system for manufacturing the single JSF jet component, Giles says, the firm plans to expand the system’s use to other products as well. It has gone live with three value streams so far, and is currently working on using the technology for two or three more. “The incremental cost of adding readers and antennas is relatively small,” he states.
The next project, Giles says, is an integration of the WIP system with the operation of the oven and press machines. The iMotion software already collects each kit’s temperature data and location, in order to monitor its temperature and determine how long it has been exposed to any specific temperature level.
Giles says he also envisions using the RFID solution to track the calibration of tools, automatically identifying when a tool is calibrated, based on an RFID read, and then alerting personnel when the next calibration is due.