During this year’s harvest season, fruit orchards in Washington State have been testing an RFID-based solution to track the quantity of cherries picked by each worker. The system is intended to provide an automated and reliable method of determining how much each individual picks and will thus be paid. The solution includes an RFID reader built into a scale for weighing harvested fruit, as well as passive tags embedded in wristbands for identifying pickers. Mike Omeg, the owner of Omeg Orchards, located in The Dalles, Ore., says that based on the results of the 2014 and 2015 seasons’ test, the farm intends to implement the system in several phases, with some of its labor force using the technology for harvesting operations in 2016, and all workers utilizing it by 2017.
FairWeigh is a Washington State University (WSU) spinoff founded by researchers who originally developed the technology to help conduct tree physiology research in the field, according to WSU associate professor Matthew Whiting, the technology’s lead developer and one of the company’s cofounders. The research, which took place about six years ago, centered on studying the productivity of cherry pickers, as there was little data indicating how productive each individual worker had been. The researchers needed a way to measure how many cherries each worker picked, and when. In that way, they could learn such details as when pickers may become fatigued, what demographics affect a worker’s productivity and other conditions that might influence how well they picked the fruit.
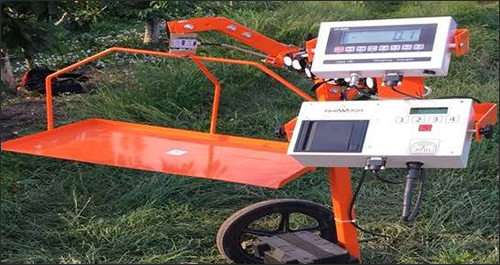
The WSU team built a solution consisting of a pallet scale and an RFID reader mounted on a wheeled frame, hooked to a vehicle that was driven onto the orchard. Individual pickers were assigned RFID wristbands. A bin was placed on the scale, and each time a picker brought a container full of cherries to the bin, that person tapped his or her RFID-enabled wristband near the reader and poured the cherries into the bin in order to weigh the fruit.
WSU presented the details of the research to area farmers in 2011, and several of those invited suggested that the technology could serve other purposes as well. “They came to us at the industry event and suggested the technology could be used as a payroll solution,” Whiting says.
Most fruit pickers are paid not by the hour but by the quantity of fruit they pick each day. Therefore, tracking the amount harvested produce is important both to the farmer and to the picker. In most cases, growers use a manual method to track workers’ productivity. The system requires that a checker stand near the bin of fruit, and that paper punch cards be distributed to pickers. As each worker fills a container of cherries, he brings it to the bin and presents it to the checker, who must visually confirm that the container is full and thus ready to have its contents dumped into the bin. The checker then punches a hole in the picker’s card for each container of fruit picked. At the end of the day or picking period, the worker turns in the card, which has his name on it, and the farm’s office staff uses it to calculate his pay.
This manual method poses a variety of potential problems, however. Checkers and pickers can often end up in arguments or have bad feelings related to the checker’s decisions regarding what constitutes a full container. If the checker decides the container is not filled sufficiently, the picker may need to lug it back to a tree, carry it up a ladder and finish filling it. On the other hand, pickers may argue with the checker and try to convince him that a container is full when, in fact, it is not.
The manual method also carries the risk of checkers or other staff members cheating for a friend and punching more holes than the picker actually earned.
In some cases, pickers could be more productive than they realized, and pick more than the required amount for each container. But in that case, the worker would not be credited for the additional fruit he had picked.
The FairWeigh solution, which was piloted for the first time as a payroll system in 2015, consists of a mobile unit that can be rolled to the specific section of the orchard in which it is needed. It has a built-in electronic weight scale, a SparkFun RFID reader and an onboard computer to capture and store the weight and worker ID data, which is then saved onto a SIM card to be taken back to the farm office at the end of the day. The unit also comes with a battery that provides the power necessary to accomplish these tasks.
To identify each individual, the orchard provided every worker with a card or wristband containing an embedded passive ultrahigh-frequency (UHF) RFID tag (Whiting declines to identify the specific make and model). The picker’s name and Social Security number were linked in the farm’s own payroll system to the unique ID number encoded to the tag. The office staff typically distributed the tags to workers, and then used a desktop reader to interrogate the tag ID and pair that data with the individual’s name and Social Security number.
After filling his container with cherries, a worker walked to the bin, where a checker visually inspected the container and hung it on the scale to measure its weight. The picker tapped his wristband or card near the reader in order to capture its tag ID number, and that ID was then stored along with the cherries’ weight, which is also displayed on the device’s LCD screen. In that way, there was no room for argument regarding the amount of fruit picked.
The FairWeigh system can also be used for checking employees in and out of work. A worker taps his card near the reader upon arriving to start his shift, and again at the beginning or ending of any breaks he takes, as well as when he leaves. At that final tap of the tag at the end of the shift, the device can display how much fruit the individual has picked that day, in addition to printing out a report. That information can then be used to calculate his pay, and to determine his hourly pay rate. The hourly rate is also used to determine how much that individual is paid during breaks.
The system can be utilized not only to ensure that pickers are credited for exactly what they pick, but also to control the amount of volume within each container. For instance, says Mark De Kleine, one of FairWeigh’s co-developers, if the fruit could be crushed by excessive weight, a farmer could require that containers only be loaded with, say, 16 pounds at a time, rather than the usual 20 pounds. The scale could then identify if a picker went beyond the maximum amount, so that he could be alerted to that fact.
The system frees workers up to deliver whatever they have in their containers, when needed, De Kleine says, and ensures that they will be fairly credited. If a worker goes on a break, for instance, and his container has only a few pounds of fruit in it, he can still turn in that amount and receive credit for it.
Whiting says he and Yiannis Ampatzidis first launched the FairWeigh company in 2014. “We spent some time trying to find a commercial partner,” he says, but were unable to find anyone interested in building and selling the product. “We decided instead to do it ourselves.”
The partners opted to employ UHF RFID technology since it was relatively low-cost. The enclosure protecting the reader against inclement weather also reduces the read range to a few inches, thereby ensuring that multiple tags are not read at once, but instead requiring an individual to present his card to the reader.
“We have many workers—hundreds—in the field each day, working together in small teams,” says Omeg, who used the system for his cherry-picking operations throughout this past summer. “We must track the productivity of each worker separately, as we pay on a piece-rate basis—in our case, pounds. Each worker can pick over 1,000 pounds in a day in 18- to 20-pound increments. Every worker and pound must be accounted for separately, which creates a substantial amount of data to track in an outdoor, variable, constantly changing environment.”
Omeg tested the technology for the past two harvest seasons in small groups of 15 to 20 workers. He says he is now ready to deploy the system for all pickers for the 2016 and 2017 seasons.
In the meantime, Whiting says he is making some improvements to the system based on experience, including adding a larger LCD touchscreen. He says the company intends to offer a cloud-based solution in the future as well, that will allow data to be stored on FairWeigh’s hosted server for a farmer to access as needed. This system, which is currently in the prototype phase, would include a Bluetooth radio that would forward weight and worker ID data to a checker’s smartphone, and a FairWeigh app on the phone would prompt it to send that information to the server via a cellular connection. In that way, he explains, the data could be stored on the cloud, and could be collected from the orchard in real time.
“Some growers are very interested in learning more” from the system, Whiting adds, such as how productive different parts of an orchard are. By using the GPS data on the checker’s phone, he adds, the solution could identify the picking operation’s exact location each day, and this data could be paired with the amount of fruit picked. Farmers could then better understand how conditions at any part of an orchard might affect a tree’s productivity.
The system was designed for cherry orchards, Whiting says, but could also be used to harvest grapes, berries and vegetable crops.