French nuclear plant service provider SPIE Nucléaire is employing radio frequency identification to locate containers at the Centre Nucléaire de Production d’ Electricité (EDF CNPE) nuclear power plant in Fessenheim, France, and is creating and managing records not only about where those containers are, but also any status changes related to radiation levels (which must be managed according to regulations).The system, provided by RFID technology company Nexess Solutions, using Xerafy passive EPC Gen 2 ultrahigh-frequency (UHF) RFID tags, has reduced the amount of time staff members spend locating containers by 70 percent, and the time used by regulatory agents to prepare reports by 80 percent. This has led to a 60 percent improvement in overall forklift operator efficiency, SPIE reports, and a 50 percent gain in storage space efficiency. The system was taken live during the fourth quarter of 2013.
SPIE is a logistics and maintenance provider for nuclear facilities, including the one in Fessenheim, for which it manages hundreds of large metal containers used to store tools, supplies and equipment for the plant’s management. SPIE’s task includes ensuring containers can be quickly located by nuclear plant personnel and inspection agents, and that they are moved as needed by either party.
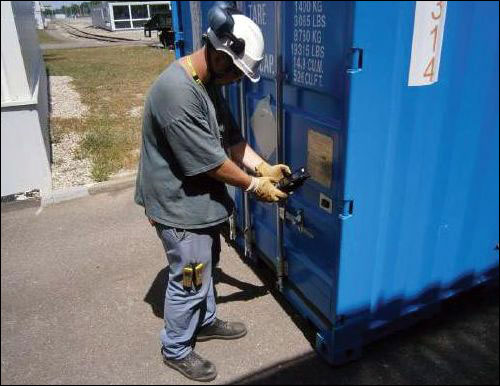
SPIE also ensures that the containers—which are loaded with hand tools, ladders, lifting equipment and other items—are in their proper locations. This requires that SPIE work closely with plant managers to anticipate the containers’ usage and stage them accordingly. For instance, a container that will be required the following day should not have others stacked on top of it.
Prior to adopting the RFID-based solution, SPIE tracked containers’ locations via a blackboard filled with Post-it notes, each representing a particular container’s location within the facility. The data was also managed on a Microsoft Excel spreadsheet.
When containers needed to be moved, forklift operators were given a piece of paper indicating those containers’ ID numbers and locations, or they might receive a phone call if an order came in while they were already moving around the facility. Inspectors arrived onsite with pen and paper, as well as a device for measuring radioactivity. They then wrote down each container’s location, along with the results of the radioactivity measurements, and later input that data into a computer and shared it with SPIE.
Olivier Ventron, a SPIE field operation manager, sought to automate this process. “I was looking at solutions to be able to manage container move requests easily and dispatch these requests to the logistic agent on the field,” he says. “The idea was also to be able to see, in real time, the status of the container storage area.”
Initially, Ventron says, SPIE was investigating two RFID solutions, including NexCap, a system designed by Nexess for industrial and nuclear facilities. “I found Nexess’ RFID solution better adapted to nuclear constraints and processes,” he explains, “and the team was more motivated and involved.”
By the third quarter of 2013, Nexess was working with SPIE to install the automated system that would help make container tracking easier and ensure a better record of where the containers had been, as well as the amount of time during which they might have been exposed to radiation. There were several constraints, Ventron reports. Tags needed to be readable in a heavily metallic environment—in some cases at a distance, since containers were often stacked atop each other and were thus difficult to read from the ground.
For the SPIE installation, Nexess chose Xerafy’s MicroX II tag and Psion Workabout Pro 3 handheld reader, according to Olivier Rouault, Nexess’ product marketing manager. NexCap also features Nexess’ Mobile Assets Management software, which collects and stores read data, in addition to managing it for inspection reports.
Each of several dozen metal containers has a MicroX II tag attached to its door. The tags are designed to withstand shock, vibration and extreme temperatures, and to be readable in the presence of metal. The ID number encoded to the tag is linked in the NexCap software with data about that container, including the items stored within. Tags were also applied to each outdoor storage area in which containers could be placed. In that way, every time an inspector or forklift operator interrogated the storage location’s tag, along with that of the container, the system’s software automatically recorded that container’s location.
Each forklift operator receives a daily list of tasks on his Psion Workabout Pro, running the NexCap software. He can view not only which containers to move, but also each container’s location, based on the storage area’s tag ID. Upon reaching that location, he reads the storage tag ID; if it is the wrong tag, he receives an alert. Otherwise, he proceeds to read the container’s tag ID as well, and then moves that container to its new location, where he reads the tag installed at that storage area. Because the use of Wi-Fi is not allowed at the facility, the collected data is stored on the handheld unit, and can be uploaded at the end of the worker’s shift via an Ethernet connection.
Inspectors use the Psion handhelds in a similar way. However, they also input the radiation measurements into the Workabout Pro 3 while conducting their tests, both inside and outside of the container. If a photograph is required to illustrate a specific report, they use the camera built into the device. This process spares the inspectors from having to fill out reports manually, or to carry paperwork or their own cameras.
Employees onsite, as well as agents, can use the Psion handhelds to read container tags in the event that a question arises regarding a specific container. If a container must be sent for maintenance or cleaning, workers in these areas use handhelds to create a record of each service provided.
The software resides on a dedicated server onsite, accessible to both SPIE and the power plant’s management. Due to the increased efficiency of its container-management process, SPIE reports that it can offer customer a faster response to container need at specific locations, as well as reduce the incidence of delays caused by misplaced containers.
“The RFID solution provided by Nexess has shown efficiency and accurate tracking of every container move,” Ventron says, adding that the system enables SPIE to better manage its operations and improve efficiency for its customer—the nuclear facility. With the data gained from the NexCap system, he says, SPIE can determine which processes could be improved in order to gain further efficiency. SPIE is also considering the use of Nexess RFID solutions for other applications, Ventron states.