In 2009, Disney deployed a radio frequency identification solution to manage costumes at one location within the Walt Disney World resort in Florida. Since then, it has expanded the solution to all costuming locations at that resort—and at Disneyland Resort in California, the Disney Cruise Line, Hong Kong Disneyland, Shanghai Disneyland and Disneyland Resort Paris (see RFID Helps Disney Employees Get Into Character).
From 2010 through 2012, Cisco Systems deployed an RFID solution to track fixed assets at 70 U.S. data centers and research and development labs, as well as at facilities in China, India and the Netherlands (see Cisco’s Business-Driven RFID Strategy).
In November, Checkpoint Systems announced that it had worked with a retailer to roll out an inventory- management solution at 1,000 stores in 100 days (see RFID News Roundup: Major North American Retailer Adopts Checkpoint Systems’ RFID Solutions).
How did they do it? To find out, we talked to the people who led these deployments and to systems integrators who have helped other companies roll out an RFID solution at multiple sites. It is not a simple endeavor, they say. It involves careful planning and the ability to handle practical and technical challenges. But based on their experiences and the learnings they shared, there are common best practices that all companies, regardless of industry or application, should follow. Here, then, are eight strategies that can boost the odds for success.
1) Assemble a Business Plan
Every RFID expansion project requires a roadmap. If you have deployed several RFID applications at, say, a manufacturing plant—you’re tracking assets, tools and work-in-process, for example—introduce one application at a time at the new location. The business plan should help you decide which task or business process to begin with, says Jason Warschauer, sales application engineer for HID Global‘s industry and logistics division.
A successful business plan takes into account physical site components, installation, costs, resources, training, solution components and post-implementation support, says Sue Flake, RFID director of business development at Motorola Solutions.
The business plan must be based on a sound methodology that focuses on up-front planning, understanding functional requirements and getting customer acceptance for the end solution—before testing and prestaging the software and hardware for each location, says Sarabjeet Chhatwal, senior director of professional services at OATSystems (a division of Checkpoint Systems). In addition, he says, you must be sure it is possible to accept items into the system and have the ability to tag and encode at a high volume.
Cisco worked with business and deployment teams at 60 locations—and set up a concierge service to ensure that any and all issues were addressed—before introducing a solution over an 18-month span, says Maryanne Flynn, director of IT. When locations were ready to go live, they plugged in the new system.
Once Disney saw the value of expanding its RFID costume management solution to other locations, its business plan began with a cost/benefit analysis, says Vinny Pagliuca, director of creative costuming. “The size of this project warranted funding through a capital authorization request,” he says. After receiving input from the finance, operation and technology teams, building an integration strategy and gathering formal cost estimates for equipment, software and labor, he developed a presentation for senior management justifying the project and explaining its benefits. By doing the “heavy lifting” up front—including negotiating pricing and discounts with suppliers—Pagliuca was able to gain support and quick approval. A bonus: The project ultimately came in under budget.
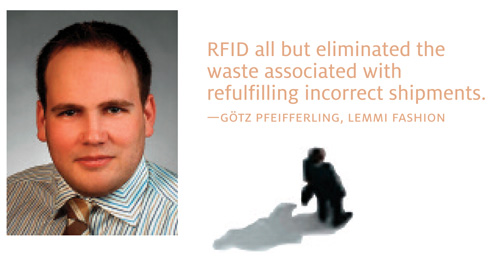
2) Develop a Deployment Plan
Once you’ve decided where to roll out the RFID solution, you need to address how to do it, and that involves asking a number of critical questions. Should you demand that the site use the same hardware and software as the initial site or provide some latitude about specific technology? Are workflows and processes the same at all sites or will adjustments have to be made? Can you transition to RFID without interrupting current business processes? Does the new facility have any unique characteristics?
It’s crucial to view a rollout in a comprehensive and holistic way, Flake says. Organizations, particularly retailers, can benefit from pilot projects that are set up at a limited number of sites and deliver information, including return on investment, that can be compared with older systems. This can provide clues about how to design a deployment strategy—including a phased rollout versus an all-at-once approach—and manage everything from the design and build-out of systems to site surveys and training. “It’s also necessary to have post-deployment support in place and help workers get up to speed with new processes,” she says.
To roll out an inventory management solution at as many as 200 stores per week, Checkpoint developed a detailed deployment plan. It’s important to have a plan for dealing with essential variations and adjustments to hardware and IT infrastructure, Chhatwal says.
Typically, he notes, you don’t need a separate plan for each location—though it’s critical to understand the requirements and limitations of each location. “A retailer with 1,000 stores would have a limited number of site variations, based on store format, use cases and RFID hardware, so visiting a few stores representative of these variations would be enough,” he explains. It’s also wise, he adds, to “conduct a multistore pilot with representative stores to test the configuration and business metrics, making adjustments before rolling out an enterprise deployment.”
The process must balance enterprise requirements with local requirements and preferences. “With any enterprise software deployment, regardless of regional variations, it’s important to RFID-enable existing store processes, instead of starting from scratch,” Chhatwal says. “It makes for easier training, employee engagement and compliance, resulting in a more successful deployment.” Checkpoint attempts to standardize and provide plug-and-play components. “In the case of a recent chainwide deployment, we were able to load preconfigured software on RFID handhelds shipped to each store, and provide Web-based training tools to store associates,” Chhatwal says. “Store managers were literally able to ‘open the box’ and get started. Software updates are all managed automatically with change-management tools.”
A deployment plan must also consider available resources. Checkpoint works with customers to ensure adequate employee training and support is in place.
Disney split its project into two phases, each of which lasted approximately 12 months. Because of the magnitude of the endeavor, the company wanted to ensure user adoption every step along the way. “The phased approach allowed us to make minor design and process improvements as we saw how our cast and guests were actually using the new systems,” Pagliuca says. It also allowed the firm to adopt a change management-centric strategy, he adds.
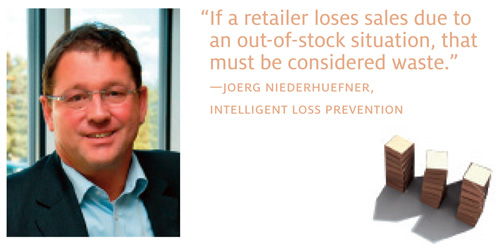
3) Conduct a Site Survey at Each Location
In most cases, it’s critical to conduct a site survey prior to installing even the most proven technology. RFID equipment may not work as anticipated because each facility’s physical layout—and the way items move through it—is different. Another potential problem is metal shelving and fixtures, which could cause RF interference. “If you are deploying with handheld devices, then a site survey may not be required,” Motorola’s Flake says. “If an organization relies on physical portals for receiving items, transitions or outgoing shipments, a site survey is probably required.” Key factors include network connectivity issues and power requirements.
A site survey should also identify which technology components, tools, software and resources to use at specific sites. And what type of data and how much data can and should be stored on the RFID tag, HID Global’s Warschauer says. “You can’t just toss technology at a location—even if it has worked well elsewhere,” he says. “It’s crucial to have high-level confidence about what will work effectively.”
Checkpoint relies on a worldwide field services team that conducts hardware site surveys. “Hardware site surveys are not required for RFID handhelds,” Chhatwal says. “For RFID hardware installed in ceilings, fixtures and entry/exit doors, each store needs to be surveyed individually to assess electrical, environmental, construction, shielding and operating frequency requirements.”
A starting point for a site survey is to document and photograph each area to fully understand how the technology will function in a particular space, Flake says. Once on site, it is critical for the systems integrator to review the site layout and validate the expected product flows. It may be necessary, for example, to understand how dock doors function and how they are used. “This determines the proper location of RFID readers and antennas for optimal read performance,” she explains. “A systems integrator should be able to provide a report detailing the work that must be performed for installation of a system, the bill of materials needed at each site and all RFID read point locations, as well as the methodology to ensure the readiness of the system.”
Disney’s integration partner, a major hardware vendor, assisted with site reviews to ensure the system would work as billed at different locations, Pagliuca says. In addition, Disney placed a project manager on site to work with contractors, oversee permits, handle inspections and review IT installations. “Testing at every site was necessary to ensure there was no interference,” he says. “In some cases, we modified designs to add shielding to protect against interference… but were able to keep to the same basic equipment designs at all locations.” No two locations are identical, he adds, so varying levels of customization—such as construction to mount equipment—was needed to implement the technology.
4) Take a Team Approach
The success of any initiative is heavily dependent on obtaining buy-in from management at each location. Without this, a company is likely to encounter pushback and problems that could ultimately derail an RFID deployment. Experts say it’s wise to adopt a team-based approach and rely on it throughout the planning and deployment phases. (For tips on getting front-line managers and other end users on your side, see Gaining Project Buy-in From Company Employees.)
Disney initially established a crossfunctional team to design and build its RFID solution. The team included staff members from the costuming workroom, costuming warehouse, laundry facilities, costuming metrics and systems, IT and costuming operations. It now insists that RFID project teams “stay connected with regular meetings to share technology ideas as well as discuss how to effectively benchmark site to site,” Pagliuca says. The teams also address training, tagging issues and managing everything from equipment installation and upgrades to scheduling new RFID deployments. They examine the specifics of a park or other location, its operating hours and available labor.
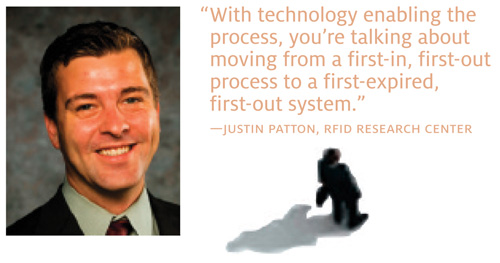
Cisco also adopted a team approach when it launched its RFID initiative to track IT equipment, and as the company rolled out its solution at other sites, it formed and consulted with teams at those locations to understand their business processes and any local idiosyncrasies and challenges. Flynn and IT executives continue to engage with local finance, human resources and IT teams to ensure the organization is addressing all challenges and issues. “They are our eyes and ears,” she notes. “They create a controlled environment that minimizes risk and maximizes the odds for success.”
5) Be Prepared to Make Some Changes
When Cisco expanded its RFID solution, it adopted a global standard for a passive RFID tag. The company identified ways to apply the tags using adhesive stickers and zip ties, but also gave executives some discretion in how they approach practical, regulatory, security and other requirements. “We learned a lot by conducting pilots and proof of concepts before expanding the program,” Flynn says. “Teams have had a chance to review deployment successes and challenges and make necessary adjustments.”
“We partnered closely with the costuming and development teams in Hong Kong, Paris and Shanghai,” Disney’s Pagliuca says. “They all use our proprietary software system. Hardware varies from site to site, but functionality is similar enterprise-wide.”
Disney conducts ongoing analysis of its RFID system, Pagliuca notes, and has made changes based on a number of factors, including safety, ergonomics, system speed, read rate accuracy and efficiency. Metrics are a key part of the equation. “You cannot underestimate the value of testing, testing and more testing,” he says.
Each retail store is different, OATSystems’ Chhatwal says, but system changes don’t have to be traumatic or expensive. In some cases, it’s possible to swap out one reader for another or reposition devices to make things work. He believes it’s wise to opt for hardware based on established RFID standards, to build in greater flexibility and ensure long-term system and data compatibility.
“Some changes are inevitable,” Flynn says. “The key is to build a platform that allows you to make changes to technology and processes without a great deal of disruption.” (For strategies on how to design and manage an RFID system that will keep pace with evolving technologies and business demands, see Futureproof Your RFID System.)
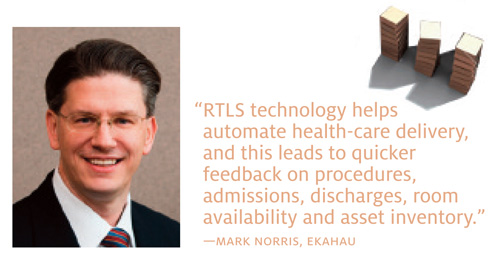
6) Manage the Transition to RFID
Moving from bar codes and manual tracking to automated RFID systems requires a good deal of oversight. At times, some parts and items may be tagged while others are not. It may also be necessary to keep a bar-code system in place for a period of time as a backup. As Disney rolled out its RFID solution at various facilities, it left the bar-code technology operating until the scheduled go-live date, Pagliuca says. “At no time during the project did we close an operating location during scheduled operating hours in order to implement the system.”
The same issues apply to software systems and data, Warschauer says. In many instances, hosted and cloud-based systems make the switchover from legacy technology more easily. “One of the advantages to the cloud is that it allows an organization to collect and push data anywhere in the world with fewer resources,” he explains. It’s also important to devote adequate time and attention to middleware during the transition period, he adds. “Fortunately, the software that manages the data is becoming more agnostic,” he says. “It is becoming easier to link systems.”
7) Expect Unforeseen Challenges
Comprehensive planning and state-of-the-art project management cannot prevent unexpected events and circumstances—there’s simply no way to plan for every possibility. When Disney expanded the use of its RFID system across the company and extended it out to cruise ships, it discovered that carbon fibers and other RF absorbing materials in some costumes created “unforeseen challenges” surrounding effective and accurate reads, Pagliuca says. The result was a need to adjust tag placements—and continue adapting costumes based on the role of the employee, environmental factors and other criteria. “Cruise ships also presented several new issues, predominantly due to metal surfaces onboard,” he adds. “During our first installation attempt, we burned through a record number of readers due to bounce and static.”
Cisco’s Flynn says when the company launched its initial RFID program, “There were tags that would work in one country but not others. During the first few months of the U.S. rollout, a world tag became available.” While it’s crucial to stay abreast of changes in the industry and a company’s specific RFID rollout, she says, it’s important to build flexibility and adaptability into processes. “Things can and will change, and you have to be ready when this happens,” she adds. It’s during these trying times that executive sponsorship, a clearly defined change-management strategy and ongoing communication pay dividends. “Teams and employees must stay informed and remain confident,” she says.
8) Don’t Overlook Training and Post-Deployment Support
To ensure employees will accept a new RFID application—and use it correctly—training must be built into the scope of a project from the outset, Flake says. While some or most sites may sail through deployment smoothly, she says, other locales could experience specific challenges that could torpedo the entire project. It’s essential for employees to understand how hardware and software works, be equipped to deal with potential problems and know where to seek help when a glitch or failure occurs.
Cisco provides training and certification to key personnel. “It isn’t necessary for everyone to become an expert, and people don’t require a Ph.D. in RFID,” Flynn says. “It’s simply important to make sure the right people have the right knowledge.”
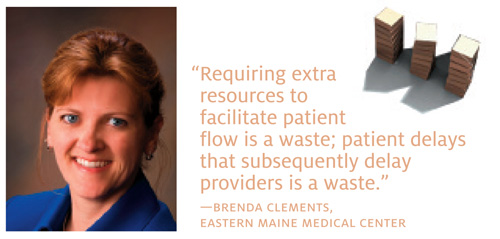
For tips on training the people who will be operating, managing and maintaining the system, see How to Develop an RFID Training Program.
“Organizations that take a best practice approach to build a targeted strategy for deploying the technology to multiple locations are far more likely to succeed,” Warschauer says.
“Come up with a realistic timeline and be prepared for it to change,” Pagliuca says. “Establish a small core group of key partners, and work closely with them on defining project scope, roll-out plans and process changes. The biggest word of advice, however, is communication and awareness. Before you try and get approval to make this level of change, talk to and showcase the changes to all levels of leadership in IT, finance, operations… anyone who may be touched by the technology. In the end, this will make the entire project run very smoothly.”
Editor’s Note: In our March/April issue, we’ll examine best practices for adding applications to an RFID infrastructure.