The management of medicines, blood products and vaccines can prove challenging for hospitals, physicians and distributors. Patient care providers want to have the right medications or biopharmaceuticals on hand when their patients need them, but many of those products, often valued at thousands of dollars, have sensitive temperature storage requirements and short shelf lives, making onsite storage unfeasible. FFF Enterprises, a major distributor of plasma, vaccines and biopharmaceuticals in the United States, has developed the Verified Inventory Program-Consignment (VIPc) system, an RFID-based solution intended to make it possible for the company’s customers to track these sensitive products, as well as the conditions in which they are stored.
VIPc, commercially released in December 2013, uses the Intelliguard Inventory Management System from MEPS Real-Time, an RFID medication-management solutions provider based in Carlsbad, Calif. MEPS Real-Time installs its RFID-enabled cabinets at FFF Enterprises’ customer sites, such as at a hospital or a physician’s office. FFF then supplies plasma, vaccines and biopharmaceuticals fitted with passive EPC Gen 2 RFID tags. The cabinets begin reading tagged medications stored within, and transmitting each tag’s ID number, along with the collected temperature readings, to Intelliguard software hosted on a server by MEPS Real-Time. The software, known as Cloud Connect, records when an item is removed and, if it is returned, how long it remained out of the cabinet. It also determines which expiration dates are imminent, and can help FFF and its customers identify goods that need to be reordered.
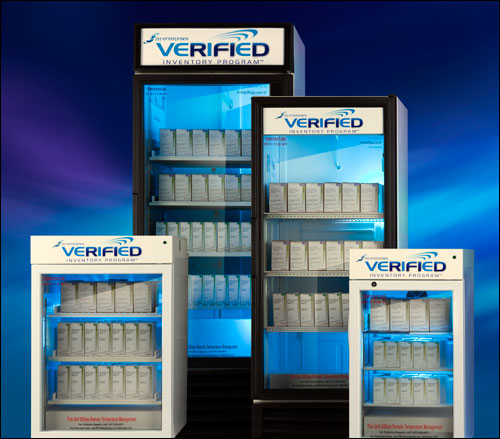
One hospital is currently installing the VIPc system, says Patrick Schmidt, FFF Enterprises’ CEO, while numerous others plan to launch the technology during the coming weeks.
Historically, FFF Enterprises has discouraged its customers from pre-ordering vaccines, plasma or other biopharmaceuticals to be stored for use on patients on an as-needed basis. The products, often valued at between $2,000 and $5,000, are very sensitive to temperature changes, and have a short enough shelf life that there is the potential for an item to expire before being administered. If a hospital were to pre-order goods and then perceive that they might expire without being used, Schmidt explains, the facility would want to return those products to FFF Enterprises, but that would lead to other potential problems. FFF would not be able to send a soon-to-expire product back to its manufacturer, and shipping that item to another hospital more likely to use it soon would pose problems for that receiving hospital. One issue, Schmidt says, is that FFF Enterprises would not be able to guarantee that the item had been stored at the proper temperature by the previous customer, or know how much time it had spent outside of a temperature-managed cabinet.
As a result, FF Enterprises has encouraged customers to refrain from ordering a product until a specific patient has an imminent need for it. In the event of an emergency, however, a hospital could face delays while waiting for a product to be delivered.
With the VIPc solution, the products remain visible to both the customers and FFF Enterprises in real time. The cabinet, available in sizes of 2.3, 5.2 and 26 cubic feet (a fourth size of 12 cubic feet is now in development), is temperature-controlled, and also comes with built-in RFID readers and antennas, explains Shariq Hussain, MEPS Real-Time’s CEO. Each cabinet is sized specifically for the use case of a customer that will be using it. MEPS employs readers from such manufacturers as Impinj and Trimble’s ThingMagic division.
To track its products, FFF Enterprises utilizes Avery Dennison RFID tags and labels that can be read when items, especially those filled with liquids, are densely packed together.
When a customer adopts the VIPc system, FFF Enterprises works with that company to identify appropriate PAR levels, by determining which goods need to be stored within the cabinet and when they would need to be reordered. The resulting recommended-size cabinet is then brought to the customer and installed.
When FFF Enterprises prepares a shipment of biopharmaceuticals for a customer, a tag is applied to each product and its unique ID is linked to its description and expiration data in the Intelliguard system. The goods are then shipped to the customer, which receives the items and places them within the temperature-controlled cabinet. As soon as the products are placed on the shelf, the cabinet’s reader identifies each item’s RFID ID. Every cabinet requires an Ethernet, Wi-Fi or cellular connection to the server, and thus continually sends updates indicating its temperature, as well as the tags being read on its shelves. MEPS offers two types of cabinets—both temperature-controlled—one that chills products at between 2 and 8 degrees Celsius (35.6 and 46.4 degrees Fahrenheit), and another that keeps the items at an “ambient” temperature between 20 and 25 degrees Celsius (68 and 77 degrees Fahrenheit).
If a product is removed from the cabinet, the reader will no longer detect that item’s tag, and the medication’s status will be updated in the software to indicate its removal. If not returned, the item will be presumed as having been used on a patient, in which case the customer can be billed for the product and, if PAR levels have been reached, an order can be processed for a replacement. If it is returned, the software can determine if it has spent an excessive amount of time outside the cabinet’s controlled temperature—and, if so, issue an alert to both FFF Enterprises and the health-care provider’s management, notifying them of the problem. In this way, both parties know the quantity on-hand, as well as the expiration dates and—if items have been removed from and returned to the cabinet—whether quality has ever been compromised. In addition, if a customer receives a product that has been at another facility, FFF Enterprises can provide a record indicating that the item has been stored appropriately at all times and is not due to expire.
For patients, Schmidt says, the solution provides the advantage of allowing hospitals to keep medications ready on an emergency basis, which could potentially save lives. What’s more, he adds, FFF Enterprises can leverage the system should one of its customers have an emergency need for a specific product. With the VIPc system, he explains, FFF Enterprises can determine which nearby facilities have that product, and then deliver that item quickly to the required site—a feature that could also save lives.
Additionally, FFF Enterprises intends to share usage data with the manufacturers of the products it distributes, including how quickly they are being used for patients, and when they are not being utilized. For manufacturers, Schmidt notes, this would be of great value once a large number of customers began using the technology. He says he fully anticipates large-scale adoption of the solution by his customers, stating, “We have a grand vision with this technology. The interest level is palpable. I’d say the momentum off the announcement is very clear…. We’re very excited about this program.”
Schmidt declines to indicate the billing model, but does report that the cabinets would be owned by FFF Enterprises, and not leased or sold to users.