Banana Belt Liquors keeps its prices low by buying liquor in bulk and storing it within a warehouse prior to selling the product at its adjacent retail store in Woodland Park, Colo., located approximately 18 miles north of Pikes Peak. Tracking the cases of product in the warehouse, however, is a major task that can lead to confusion regarding what is or is not in stock, since it is not feasible to conduct complete inventory counts on a frequent basis. Therefore, Banana Belt’s owner, Carla Clausen, has installed an RFID system that has eliminated the problem. Thanks to a solution supplied by Truecount, which the beverage company installed itself, Clausen says she now knows product is in the warehouse, and can conduct quick inventory checks to determine if that has changed at any given time.
Without an automated solution, Clausen says, she would print a spreadsheet and carry that around the warehouse, looking through product stacked from floor to ceiling, in order to see what she had on hand at that facility, as well as in the store. The process took many labor hours to complete, she notes.
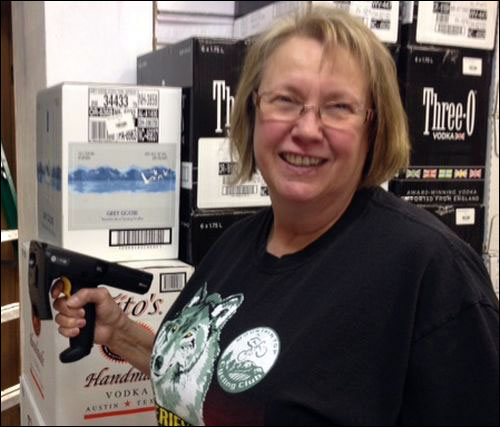
Clausen’s daughter, a computer science college student, had been reading about radio frequency identification and suggested the technology might solve the company’s inventory problem. She says she approached multiple RFID vendors and discovered that the available options were more expensive than the solution she sought.
When Clausen explained her challenge to Truecount, the company replied that it could provide a reader workstation for interrogating tags via a PC storing Truecount’s Essentials software package, as well as a handheld reader and passive EPC ultrahigh-frequency (UHF) RFID tags, to be affixed to cases of product. This simple solution would be low-cost, she explains, and could be expanded to the store over time.
Truecount shipped the products to Banana Belt in September 2013, and spoke with Clausen over the phone as she and her IT representative installed and began operating the standalone system. (Flying an employee from Truecount’s New Hampshire headquarters to Banana Belt’s Colorado facility would have added time and costs to the project.) Initially, Truecount encoded and printed the tags that it provided to Banana Belt. Clausen, however, says she quickly realized she needed to be able to print and encode tags onsite in order to keep up with the high volume of goods entering the warehouse each week. Truecount then sent her a Zebra Technologies RZ400 RFID label printer-encoder, which she began using in November.
With the technology in place, as cases of new product arrive at the warehouse, Clausen or her staff use the RZ400 device to print and encode RFID labels made with Alien Technology Squiggle tags, pairing each label’s unique ID number with data about that product stored in the Essentials software. Personnel then apply a label to each case and store it in the warehouse.
When Banana Belt needs to replenish stock on the store’s sales floor, personnel locate and remove the appropriate case from storage, says Zander Livingston, Truecount’s CEO and cofounder. The workers then read its tag using a Motorola Solutions MC3190-Z handheld reader with a Wi-Fi connection to the PC, or an FX7400 reader cabled to the PC at the RFID workstation provided by Truecount. In this way, the software is updated to indicate that the product is no longer in the warehouse and has been moved to the store.
To conduct periodic inventories, Clausen says she can select a specific product line to search for, or simply walk through the warehouse, reading tags on all products, to gain a complete inventory. That list can then be compared against the inventory she expects to have in the warehouse.
With the solution in place, Clausen reports, Banana Belt now has a much more accurate record of which products are on hand at any given time. If something is discovered to be missing, she adds, it is thus easier to determine when and how this occurred, since the inventory checks take place much more frequently.
The next phase of the deployment, which will take place during the next few years, will be to tag each individual bottle of liquor or wine so that Clausen can track goods on the sales floor. Clausen says she also intends to install a reader portal at the front door, in order to deter shoplifting by identifying when a customer walks out of the store with a case of liquor or wine he or she has not paid for. (Clerks would remove the tags at the point of sale.) In the future, she says, she may also apply a tag to each bottle of high-value liquor. In addition, the company plans to eventually install a reader at the point of sale, and to integrate the Essentials software with the company’s own POS software. In that way, the firm will be able to create an automated record as soon as each item is sold.
Currently, Clausen says, the technology’s benefit is simply knowing what she has in the warehouse on a regular basis. She likens the solution to a security system that requires some investment to install, but that offers cost benefits difficult to measure. Human error may still occur, she notes, since personnel have occasionally forgotten to read the tags prior to moving product from the warehouse to the store. However, she adds, “That’s just a matter of further training.”
Initially, Clausen says, 1,000 cases were tagged at the warehouse. Banana Belt has since ordered several thousand additional RFID labels.