The Minnesota Department of Transportation (MnDOT) is employing radio frequency identification to pinpoint the locations of sensors buried within roadways. The sensors, which measure strain and pressure levels, are used to test the performance of a variety of roadway materials, mixes and application methods. To date, the agency has installed only four tags into its pavement test tracks as part of its MnROAD project, says Bob Strommen, a research systems integrator at MnDOT, but now that the tags have proven their performance, the agency intends to deploy them to locate new strain or pressure sensors as they are installed, and it may also opt to use the technology for other purposes as well.
The solution was provided by EMKAT, a mobility solutions provider based in Plymouth, Minn., and includes Portable Technology Solutions‘ TracerPlus software and a Motorola Solutions‘ MC9190-Z handheld reader to interrogate the tags. “EMKAT uses our software to create this mobile application,” says Kristen Comeau, TracerPlus’ channel account manager.
The MnDOT says that MnROAD is one of the few projects in the world—and perhaps the only one operating under such cold conditions—in which roadways are laid in a variety of concrete or asphalt mixes, and are then examined to determine how they wear as the weather changes and vehicles pass over them. The objective, Strommen explains, is to finds ways in which to make roads last longer, perform better, cost less to build and maintain, be constructed faster and have minimal impact on the environment. The agency shares the results of its work with other state DOTs across the United States. Thus far, the project consists of thirty 500-foot-long sections of roadbed composed of a variety of roadway mixes, at two locations northwest of Minneapolis and St. Paul—a 3.5-mile-long section of active roadway running parallel to Interstate 94 and used by 28,000 vehicles daily, and a 2.5-mile closed loop of roadway. Testing on the 2.5-mile loop, designed to simulate a rural road, includes an MnDOT 40-ton, five-axle tractor trailer passing over the embedded sensors, in order to quantify the effect that such a heavy load has on pavement structure.
Altogether, the MnDOT has embedded 9,000 wired sensors into these two stretches of road over a span of 20 years, which connect to data processors mounted on the sides of the roads. The agency had no way to verify the precise locations of the strain and pressure sensors. Knowing these devices’ locations is critical, since the MnDOT is tracking the effects of each individual passage of a vehicle over a specific spot on the road. The strain sensors are designed to indicate the conditions that lead to cracks or fractures in the asphalt or concrete, while pressure sensors simply detect the amount of force being felt under the roadway. The MnDOT truck’s driver is instructed to drive as close as possible over each sensor, so that the agency can determine the effect on the road immediately under the vehicle’s tire. The truck is equipped with a GPS system to identify its whereabouts, but the agency had no way to determine exactly where the sensors are once they are covered by pavement.
In the past, to identify a particular sensor’s location, the road crew had to paint an X on the pavement—or cut one into it—after the sensor was embedded. However, that method was not always precise. For example, a sensor’s location might move 12 inches or more from its original spot during the road-paving process, or the true location could simply be lost as the paving took place. Then, as a truck passed over the site of a buried sensor, it may, in fact, not have been as close to the actual spot as was thought.
To better pinpoint the sensors’ exact whereabouts, Strommen’s supervisor suggested implementing RFID. “I ran with that idea,” he says. He discussed the concept with EMKAT, which then selected PTS’ TracerPlus software to receive and store location data on a Motorola handheld reader.
The agency required a tag capable of withstanding the high temperatures and pressures created during road construction, and thus chose William Frick & Co.‘s WF-SM-25S silicone-coated wire tag, a flexible, rugged, 6-inch-long tag made with an inlay developed by Technologies ROI (TROI) and containing a passive EPC Gen 2 ultrahigh-frequency (UHF) RFID chip from Impinj. Strommen says he was initially skeptical about the RFID tags’ ability to be read through concrete or asphalt. However, when he placed a tag directly under a 9-inch-thick block of concrete, he found that it could, indeed, be read.
The tag is attached to the frame on which the strain sensor is mounted via a tie-wrap. It is important that the tag not interfere with the strain gauge’s functioning, Strommen explains, which is why the agency opted to attach the tag to the frame on which the sensor is mounted, rather than on the sensor itself. The tag can then be located within approximately 2 inches of the sensor, he says.
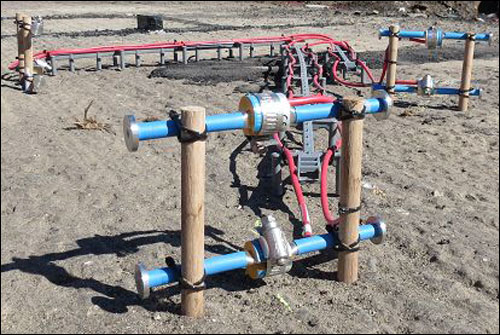
The staff embedded the tags, along with the sensors and the frames on which they were mounted, 6 inches below the road’s surface in August of this year, after which they completed the laying of the pavement, and then put the handheld reader in Geiger counter mode. The TracerPlus software on the handheld also married the sensor ID number with the unique ID on the tag itself. By waving the handheld in the area in which the sensor should have been placed, they were able to read precisely where each tag was located, and then cut a mark in the pavement to identify that location visually.
MnDOT now plans to begin attaching tags to all new strain or pressure sensor mounts as they are embedded in the MnROAD roadways. The use of RFID under the test roadways “was the start for us,” Strommen says. “It’s something we needed to do, and I think it worked out very well.”
Strommen says he is also considering other use cases for RFID by the agency. For example, tags could be attached to signs that are also being tested for reflection degradation, based on the amount of exposure to weather and sunlight over time. If workers inspect the signs periodically, he says, they could write data to the tags using a handheld reader, indicating what they had done and when, and thereby creating a record that could be stored onsite. The tags could also be used in the agency’s warehouse, he adds, where road construction materials—such as soil or asphalt samples—are stored in large buckets. Tags could be applied to those containers, and software could store the tag’s unique ID, along with a description of the material stored within each bucket. Users could then locate a specific material using the handheld’s Geiger counter mode. However, he notes, both ideas are still at the conceptual stage.
The TracerPlus system is designed to be low-cost and easy to install, according to Kate Lloyd, Portable Technology Solutions’ TracerPlus account manager. With the TracerPlus software residing on the handheld, Strommen says, he can input data related to each tag’s ID, as well as the location where it would be installed. Although the software could also be used to collect data on a back-end server, Strommen says he currently does not have a need for that function, since the agency simply wants to identify a sensor’s location with the handheld, not accumulate historical data.